This post originally appeared in the Navigate the Future blog.
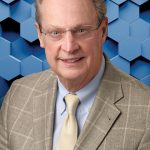
We recently hosted a webinar, Additive Manufacturing Process and Performance Simulation of Composite Tools in an ongoing series called Innovation that Inspires. Now available on demand, the webinar is a great showcase of our partnership with Purdue University’s Composites Manufacturing & Simulation Center (CMSC). Dr. R. Byron Pipes Executive Director of CMSC and the John L Bray Distinguished Professor of Engineering, along with graduate student Eduardo Barocio deliver an inside look at how the Purdue center has simulated and validated the Extrusion Deposition Additive Manufacturing (EDAM) process used in systems like Large Scale Additive Manufacturing (LSAM) developed by Thermwood, a leader in CNC routers.
The webinar features a real life, complete end-to-end additive manufacturing software story from concept through complete fabrication of a 3D printed boat hull.
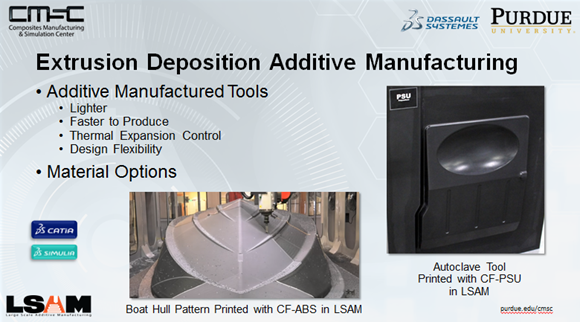
In exploring EDAM for Composites, the Purdue team shares a number of critical key extrusion factors beginning with CAD geometry (in this case CATIA), and then looking at how 3D printers layer and slice and ultimately produce the final part.
The team also shares their simulation capability and capacity as related to additive manufacturing, and how they leveraged simulation technology (in this case with SIMULIA) into their additive manufacturing process. By utilizing both process simulation as well as performance simulation the team is able to ensure that the the final 3d printed parts meet production standards (exploring 3d printing factors such as heat transfer and polymer crystallization).
As Dr. Pipes and Eduardo Barocio share throughout the “boat hull” story, it is clear that by leveraging the right technology, the team is able to be smarter and more efficient – as they continued to learn and advance from their 3D models to final part production. Watch the on demand webinar to hear the full story.
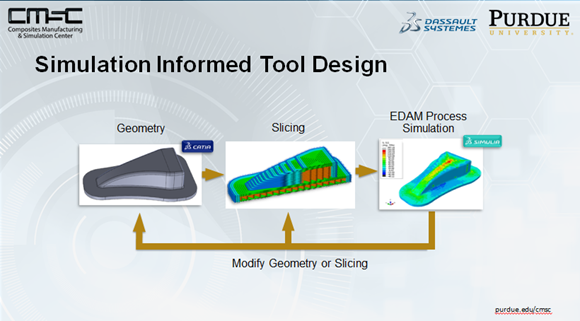
Different industries have different needs in the manufacturing of carbon fiber composites. Purdue’s CMSC works with a range of industries to ensure they have the control of material microstructure to achieve specific stiffness and lifetime performance of their product. As a Purdue University Center of Excellence, the CMSC is also a leading academic center focused on training the next generation of engineers.
According to Rani Richardson, technical sales with Dassault Systèmes CATIA brand:
“Additive manufacturing empowered by generative design is revolutionizing how production parts are being conceived and produced. Dassault Systèmes provides a digital thread that connects, integrates and intuitively captures design, materials and manufacturing, backed by multiphysics-based simulation to reduce the time it takes to conceive and produce production parts. 3DEXPERIENCE provides a full portfolio of integrated applications for additive manufacturing that work seamlessly across design, manufacturing, and in-service performance.” – Rani Richardson
Click here to watch this OnDemand webinar and to learn more:
What to learn more about Dassault Systèmes’ simulation solutions for additive manufacturing? Visit: go.3ds.com/Print2Perform