2020 forced manufacturing companies to rethink every aspect of business operations. Collaboration is now a high priority, not just for engineering but for every department. Supply chains were put under severe pressure, to keep up with logistical challenges, to balance supply with demand, and to keep the supply chain fully informed and responsive.
“In this time of great flux, we must dare to take bold steps and discard what is not future-proof,” says Wilfried Vancraen, CEO and founder of Materialise, a leading additive manufacturing services and software provider. “We need to harness the core values of technologies like additive manufacturing to move towards new ways of thinking and doing that have meaningful impact.”
Companies who have been moving slowly into additive manufacturing (AM) found reasons in 2020 to accelerate. For some, it was the need to invent new products faster, for others it was to help augment traditional manufacturing without having to deploy additional traditional factory resources.
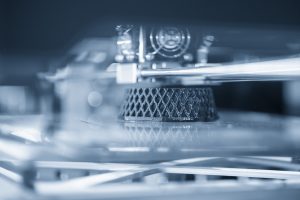
The result is a general consensus that “Business As Usual” is transforming into “The New Normal.” This New Normal requires agility, from concept design to sales and service. Much of figuring out The New Normal in 2021 will be about increasing the use of additive manufacturing. This presents several challenges, which I believe will be recognized as AM’s significant trends in 2021.
Additive Manufacturing Fueling New Opportunities
The first trend is (re)discovery of AM’s best purposes. Additive manufacturing can enable new choices and meaningful new opportunities. Using AM only for prototyping or initial production runs ignores the best possible purpose of the technology, which is to create things that no other manufacturing process can accomplish. AM can print novel designs, print them with fewer components, and potentially with less waste.
Using AM smartly also has the side benefit of opening a new path to the second trend, sustainability. But gaining sustainability is not as simple as switching from traditional methods to AM. “If you assume 3D printing is by definition sustainable, then you are greenwashing,” claims Vancraen. Lower environmental impact must take into consideration energy use, pre- and post-production issues, and printing waste. Some current AM methods generate significant material waste, which generally cannot be reused.
Materialise, mentioned above, and materials developer BASF recently conducted a lifecycle analysis, taking a close look at an additive manufacturing software print run of 1 million pairs of midsoles. They compared the environmental impact of three 3D printing technologies with the conventional manufacturing process, which uses polyurethane casting. The analysis showed that for large series of identical products, 3D printing is currently not the most sustainable choice. The study was one factor in leading Materialise and BASF to introduce a new specification for laser sintering that allows material reuse.
Growth in Design for Additive Manufacturing (DfAM)
Value is created at the beginning of the chain. The second trend that will emerge in 2021 is significant growth for Design for Additive Manufacturing (DfAM) solutions. Earlier this year I wrote two columns here based on a conversation with Dr. Michael Grieves, Chief Scientist for Advanced Manufacturing at Florida Institute of Technology. He says DfAM must be as much about materials as it is about geometry.
“The future is going to be about using custom materials that match the capabilities of the job. You print based on the custom materials.”
He foresees manufacturers will ask the materials makers for raw 3D printing materials that fills their needs for various issues (temperature tolerances, flexibility, compression strength, etc.), “and then they will custom make it.” DfAM becomes even more important, Dr. Grieves says. “We will tailor the material to the idea,” and not the other way around. “Today we worry about geometry, but we should worry about design for a specific material on a specific 3D printer.”
The Moonshot Approach
The third trend is not about a specific product or service, but about a way of thinking about manufacturing. In 2021 many forward-thinking manufacturers will bypass incremental application of AM and apply the moonshot approach to product development. In this context, a moonshot is an ambitious commercial project that is both exploratory and ground-breaking.
One current example of a moonshot approach to AM is currently happening at Airbus. The aerospace giant recently revealed plans to accelerate the development of hydrogen-powered commercial jets. Their ambitious agenda bypasses the intermediate step of creating a hybrid engine. The goal is to have the first zero-emissions, climate-neutral hydrogen-powered jet in service by 2035. Additive manufacturing will play a big role in the design of this new generation of aircraft.
Climate change is an example of a global crisis that provides manufacturers with incentive to think outside the box and fast-track technological innovation. The need for radical reinvention is an opportunity for AM to step into its own as a manufacturing method that will help invent the future.
#
Editor: Dassault Systemès has an on-demand online seminar, called “Cognitive Augmented Design for Additive Manufacturing.” Learn how to leverage the 3DEXPERIENCE platform to design and simulate highly optimized parts based on a variety of competing factors and build methods, including additive manufacturing.