The sharp rise of automation and a shortage of skilled laborers have contributed to increased demand and a growing market for robots. Robot manufacturers can leverage this rising demand by offering their customers an alternative to the traditional ownership model: the robot-as-a-service (RaaS) model. In the RaaS model, manufacturers provide robots to customers on a subscription or pay-per-use basis and oversee their service and maintenance to ensure maximum uptime.
This model opens a new revenue stream for manufacturers, eliminates the need for customers to make a large up-front investment, and ensures better service and maintenance outcomes for robot end-users. Many startups in the robot manufacturing sector have already embraced the RaaS model, as it presents their customers with a low barrier to entry that makes it easier for them to adopt robots for automation.
But this model represents an opportunity for robot manufacturers of all sizes, and many small, medium and large robot manufacturers are considering their own RaaS offerings to stay competitive. It is essential, however, that any company adopting a RaaS model undergo extensive preparation to ensure effective implementation.
Keep reading to learn more about the level of planning required for manufacturers to implement the RaaS model as well as the benefits it provides robot manufacturers and their customers alike.
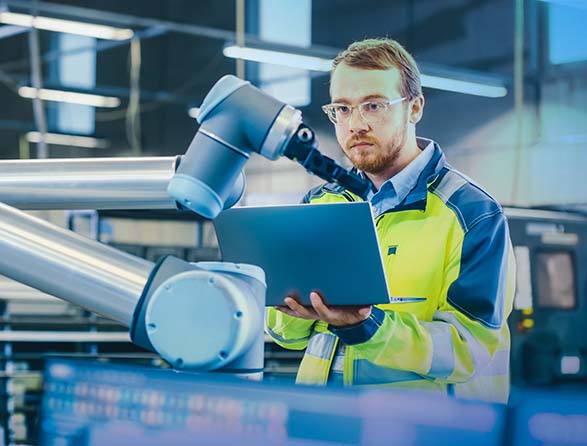
Adopting RaaS Requires Extensive Planning
The RaaS model is both a significant opportunity for today’s robot manufacturers and a major change from their traditional business models. Traditionally, robot manufacturers employ standard product development and sales processes: they gather requirements from the field, design and manufacture their robots, and sell them to their customers in a single transaction. They typically give little thought to service planning when designing their robots.
Some manufacturers also offer their customers contracts that cover periodic service and parts replacement, but these agreements bring in relatively little revenue for the manufacturer and are often limited in scope. The RaaS model in contracts, enables manufacturers to ensure regular, recurring revenues in the form of subscription-style payments while guaranteeing customers higher levels of robot uptime and faster service delivery than with the traditional agreements.
Adopting a RaaS business model is not, of course, as simple as drafting new service agreements. It requires extensive planning on the part of robot manufacturers, beginning with the robot design process. To enable the model’s promised service improvements and increased uptime, engineers must integrate capabilities related to data collection, service and maintenance early in the design process. These capabilities are essential for providing robot manufacturers with the operational data they need to analyze the health of an asset and act quickly in the case of an unexpected failure.
In addition, robot manufacturers must account for the business impact of shifting to subscription-style RaaS agreements, which represent a significant change from traditional sales and service models:
- Selling robots as a service means robot makers receive less money from customers up front but have a guaranteed cash flow in the future.
- Because robot manufacturers retain ownership of their robots in the RaaS model, they must keep these assets on their books for the duration of their lifecycles.
- In the RaaS model, manufacturers are also responsible for service and maintenance, which means they must keep the robots in working condition throughout the robot’s life. RaaS agreements typically include stipulations that connect customer payment to agreed-upon amounts of equipment uptime, so robot companies must provide fast, responsive service and maintenance to maximize revenue. If the manufacturer fails to satisfy those stipulations, it receives smaller payments from their customers.
From design through the delivery of after-sales service, adopting a RaaS model requires robot manufacturers to make significant adjustments to how they do business. If these adjustments are not planned carefully, companies may find themselves unable to fulfill the terms of RaaS agreements and put their businesses at risk.
How to Make RaaS a Reality
To implement an effective RaaS business model, robot manufacturers must incorporate robust data collection capabilities into their designs, improve service documentation to facilitate more efficient service and repairs, and continuously monitor and improve robot functionality and sustainability. Dassault Systèmes’ 3DEXPERIENCE platform on the cloud provides robot manufacturers the comprehensive capabilities they require to accomplish these goals and provide their customers with greater value for their investment.
Robots Need Integrated Data Collection Capabilities
Robot manufacturers that implement a RaaS business model must continuously gather and analyze the robots’ operational data to gain insight into their condition. This data is critical for manufacturers as they make decisions about service to ensure their robots’ uptime and functional efficiency. Engineers must therefore integrate into robot designs sensors and components that enable operational data gathering and analysis.
Specifically, these integrated components must be able to stream data to the cloud, which enables remote monitoring and more robust predictive maintenance capabilities. These capabilities ultimately empower manufacturers to minimize unplanned robot downtime for their customers.
To further improve robot serviceability, manufacturers can shift from standard design practices to a modular design approach. A modular approach enables designers to create interchangeable modules or components, which means they can customize builds to meet customer specifications without redesigning the entire robot. Modularization also promotes quick, less costly development cycles; makes it easier to identify and address failures; and empowers engineers to continuously and incrementally improve robot designs and efficiency over time.
Better Service Documentation Promotes Better Outcomes
Robot manufacturers can leverage computer-aided design (CAD) data to improve service documentation. Using this data, engineers can create accurate build records and maintain an as-built virtual twin for each robot. This helps to customize and personalize digital service documentation.
Building a virtual twin of a robot unlocks multiple key capabilities that improve service outcomes and help optimize asset performance. Feeding real-world operational data from a physical robot into a virtual twin allows manufacturers to monitor robot health, assess potential maintenance needs, and make adjustments to optimize robot performance. The virtual twin can even empower manufacturers to apply service and repair procedures in a 3D virtual reality (VR) environment. As a result, they can train service technicians and conduct repairs remotely.
Planning for Service Improves Robot Functionality and Sustainability
Robot manufacturers can also leverage a plan-for-service approach to improve the efficiency and functionality of future product designs while also making them more sustainable. Engineers use operational data from robots in the field to better understand how components perform over time. This understanding allows them to identify design changes that improve performance, reduce service and maintenance requirements, and extend robot lifespans. Adopting a modular approach to robot design can make these improvements easier to implement, as engineers can quickly replace old modules with minimal disruption for end-users.
In the same way that engineers design for service, they can also design for sustainability. Design for sustainability involves analyzing data to identify components that can be designed to make reuse, repair, refurbishment, refinishing, reselling and recycling simpler and more efficient. With this approach, engineers can also make designs more fuel efficient to reduce emissions and optimize them to reduce material waste during production.
The 3DEXPERIENCE Platform Provides the Capabilities That Enable RaaS
The 3DEXPERIENCE platform on the cloud empowers robot manufacturers to implement RaaS business models and deliver key advantages to end-users. With the platform’s Virtual Twin Experience, engineers can create virtual twins of their robots, enabling them to identify potential failures and address them before they result in lengthy, costly periods of robot downtime. In addition to these improved service outcomes, the 3DEXPERIENCE platform allows robot manufacturers to integrate advanced technologies, such as VR or augmented reality (AR), into their service offerings.
As a result, these companies can troubleshoot problems remotely and provide better training to new technicians, both of which help reduce service and maintenance costs and increase robot uptime. Furthermore, the 3DEXPERIENCE platform supports modular design, so engineers can make incremental improvements for functionality and efficiency and address failures by simply replacing or upgrading the faulty module.
The 3DEXPERIENCE platform also supports the continuous improvement of robot designs. Manufacturers can leverage robots’ operational data and the virtual twin to identify design changes that improve sustainability, simplify service and maintenance, extend robot lifespans and enhance functionality. Robot manufacturers that adopt the platform can therefore offer customers RaaS agreements that provide them with leading-edge products and improved service outcomes that maximize robot uptime and efficiency. This approach enables robot makers to increase profitability, grow their market share and stay ahead of their competition.
Summary and Recommendations
The RaaS business model represents a significant opportunity for both robot manufacturers and their customers. Manufacturers can increase revenues while ensuring more efficient service delivery and, therefore, more overall robot uptime for end-users. But this model is only possible through careful planning and a re-envisioning of the machine builders’ design process.
Manufacturers must integrate operational data collection capabilities into their robot designs, develop more comprehensive service documentation and plan for serviceability and sustainability early in the design process.
The 3DEXPERIENCE platform on the cloud provides robot manufacturers with the capabilities they need – including the creation of virtual twins – to accomplish these goals and offer customers the numerous benefits of the RaaS model.
Robot manufacturers looking to implement a RaaS model should do the following:
- Evaluate existing approaches to after-sales service and calculate the costs and revenue associated with this approach.
- Promote the benefits of RaaS to customers to raise interest levels in that model.
- Adopt the 3DEXPERIENCE platform on the cloud to create digital twins of their robots and execute planning for service initiatives that make RaaS possible.
- Work with end-users/customers to capture the real-world benefits of RaaS and promote those advantages to other existing and potential customers.
For more information on the end-to-end process of robot manufacturing, check out Accelerate Your Robot Development
This article was done in collaboration with Mathieu Piquemal