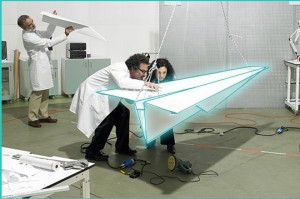
第5章 不確定性を掌に置く【製品ライフサイクルで考える不確かさと定量化の方法】
“不確かさは、モノづくりのあらゆるところに顕在/内在する“ということを、カテゴリーに分けて整理した前回記事からの継続として、今回は、製品ライフサイクルという観点でのさまざまな不確かさを再整理し、どう扱えばよいか、をまとめてみます。まずは、“不確かさ=>予測できない=>何もわからない”のではなく、正しい考え方をすれば、不確かさを定量的に取り扱うことができるということを示します。シミュレーションの予測能力は、これまでお話ししてきた精度に、“定量化された不確かさ”を加えることになります。英語では、Uncertainty Quantificationと表現され、一つの学問体系になっています。インターネットで検索するとたくさんの情報が出てきます。定量化するために把握するべきことは下記のように定義されています。
【予測能力=精度+定量化された不確かさ(Uncertainty Quantification)】
A) 不確かさの要因の特定=CTQ (Critical to Quality)
B) 不確かさの大きさの同定=標準偏差、上下限値
C) 不確かさの影響度評価=信頼度、ロバスト性
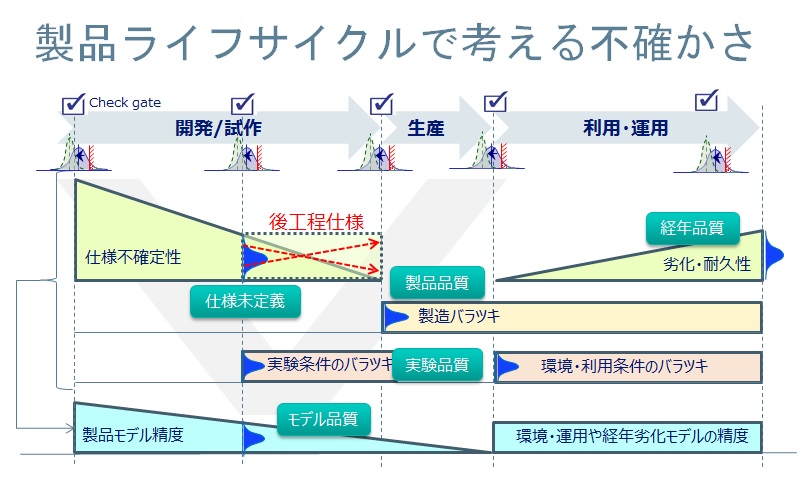
この定義は非常に強力です。まず、不確かさは、定量化可能であると言っています。定量化のためには、その要因を把握と大きさを把握し、性能にたいする影響度がわかればいいのだということを言っています。定義されてみると当たり前のように見えますが、さもなければ、“不確かな事象”を扱うことは到底難しいでしょう。これらの3つの定義の意味するところを見ていきます。
(1) 不確かさの要因の特定
今回は、製品ライフサイクルという時間軸で見た場合にさまざまな不確かさがどういう場面で登場するかを見てみましょう。添付の図を見ていただくのが一番わかりやすいので、その順番で説明します。要因はじつにさまざまです。シミュレーションを対象にする場合、主には5種の要因が考えられます。
① 製品品質:製品生産のバラツキで、製品自体が持つ不確定要因です。材料物性、公差や加工時の物性変化・溶接品質のバラツキなどがあげられるでしょう。
② 実験品質:実験条件や環境のバラツキで、性能を測定する際の条件変動、測定の誤差、実際に稼働している状況や操作の変化などがあります。
③ 仕様未定義:開発中における、後工程仕様が未確定であることによる、性能の変動可能性です。この要因は当たり前すぎるのであまり着目されることがないのですけれど、実は後工程で手戻りが起こる重要な原因の一つではないかと、思っています。
④ 経年品質:長期使用時や経年劣化などによる性能低下やリスクです。過去数十年前に生産・設置された建築物の耐性が大きな問題になってきており、今後ますます検討の重要度が増していくでしょう。適切な交換や修繕を必要とする長期運用建築物やプラント・輸送システムなどが主な対象になります。
⑤ モデル品質:シミュレーションモデルの計算精度に影響するモデルの品質です。モデル化に内在する仮定や近似、メッシュサイズや境界条件、物理モデルの表現の正しさなどです。この項目は、不確かさではなく上記の式の“精度”というくくりで定義されていますが、予測能力に大きく影響し、不確かさと同様に常に考慮する必要があるので、改めて記載します。 どんな製品も上記の5種のバラツキ要因の影響を免れないので、厳密には、すべてを考慮して設計する必要があるわけですが、現実的に与えられた状況と段階の中でどのような要因を考慮しなければならないかのあたりをつけるのが、不確定性に対応するための設計者の仕事になります。図を見ると、製品ライフサイクルで、どういうバラツキに関する品質を考慮しなければならないかを概観できます。開発段階の途中においては、仮に製品と実験のバラツキがないとする理想状態だとしても、モデル品質と仕様未定義の問題は必ず考慮しなければならないことを示しています。しかし、実際のところは製品と実験のバラツキは必ず存在しますので、すべての要因を一緒くたにするのではなく、要因カテゴリーごとに分けて検討し、無駄に多すぎず、見逃しリスクがない程度に少なすぎない不確定性の要因を選択し考慮することが大切なのです。ただ、いずれの要因カテゴリーも突き詰めていくと具体的な、パラメータや物理量で特定できるものなので、不確定現象を取扱う第一段階は通過可能なのです。
(2) 不確かさの大きさの同定
要因によってその大きさの定義の仕方が異なってきます。よくある正規分布に従うバラツキででれば標準偏差、一様分布であれば上下限値といった具合です。いずれにせよ、計測しなくてはわからない大切な定量化なのですが、測定が難しいとか、どの量を測定すればいいかわからないという問題も出てくるでしょう。ここで、シミュレーションならではのバーチャルな方法を適用できます。たとえば、材料物性のバラツキを考慮すべきかどうかわからない場合、その標準偏差を大中小といった3水準ぐらいに仮定し、その正規分布のバラツキをシミュレーションに与えて実験計画法もしくはモンテカルロ法で計算し、性能のバラツキ影響を調べることで、物性バラツキと性能バラツキの定量的な相関を把握することができます。小さいバラツキでも性能に影響するようであれば、きちんと物性バラツキを測定する動機になりますし、逆に大きいバラツキでもそれほど影響がなければ、他のバラツキ要因との相対的な影響度(寄与度)を考慮すべきという結論になるでしょう。
(3) 不確かさの影響度評価=信頼度、ロバスト性
バラツキ要因を入力とすると、性能バラツキはシミュレーションの出力になります。その定量化は、実験計画法やモンテカルロ法用いて、感度や寄与度、SN比、標準偏差、信頼度などの量を計算して評価することになります。ここまでの方法が確立しさえすれば、不確定性を定量化し、その影響を少なくする方法論を得たことになります。その著名な手法が、タグチ・メソッドやシックスシグマ手法なのですね。これらの手法の使い分けについては、後の記事で説明する予定です。
【SIMULIA 工藤】