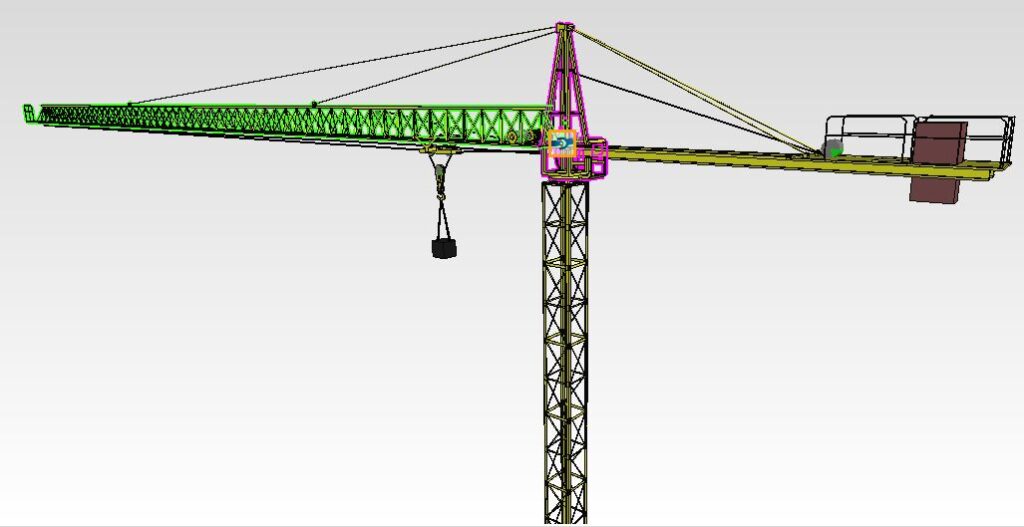
Introduction
A tower crane is a modern form of a balance crane with the same basic parts. Fixed to the ground on a concrete slab (and sometimes attached to the sides of structures), tower cranes often give the best height and lifting capacity and are used to construct tall buildings.
The conditions under which the crane operates determine its general dimensions very largely. The height is fixed by the height of the tower it is constructed and the radius at which the maximum load is to be lifted, as determined by practical considerations and the construction site.
During the design of these cranes, static loads are generally considered based on utility requirements/load-carrying capacity, but forces and torques on components resulting from motion simulations can also serve as useful input for detailed structural analysis.
Below is a concise overview of a tower crane workflow, highlighting the tools and processes used.
Workflow Overview
1. 3D Modeling:
– We created detailed 3D models of each component using 3DExperience CATIA:
– Part Design App for individual components.
– Assembly Design/Mechanical Systems Design App for assembling the crane.
2. Dynamic Simulation:
– Using the assembled model, we employed the Motion Analysis App to create mechanisms and perform dynamic simulations, analyzing the crane’s movement and interactions.
3. Structural Analysis:
– To analyze the structural integrity of the hoist:
– We used the ‘transfer loads’ command from Motion Analysis to generate a simulation object that includes load data.
– This object is compatible with structural analysis apps like Structural Model Creation and Mechanical Scenario Creation, where we finalized couplings and computed structural simulations.
4. Cable Modeling:
– Since the Motion Analysis app currently lacks the capability to simulate cables:
– We utilized Simpack to model the cable elements.
– We exported our assembly from 3DExperience to Simpack using the connector, which converts the model into a format compatible with Simpack, complete with mass and inertia data.
5. Enhancing the Simpack Model:
– In Simpack, we extended the model to include:
– Pulleys for cable support.
– Connections and excitations to represent motors.
– The cable element itself.
– This allowed us to simulate the full behavior of the Tower Crane, including cable dynamics. We reviewed results and animations within Simpack to analyze crane performance.
To view the full workflow, visit the SIMULIA Community post, which includes a PowerPoint presentation and a video that provide a more detailed explanation of the workflow and findings.
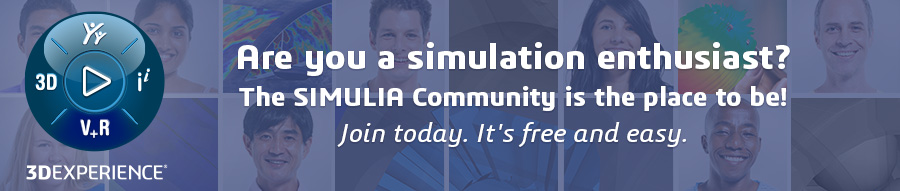
Interested in the latest in simulation? Looking for advice and best practices? Want to discuss simulation with fellow users and Dassault Systèmes experts? The SIMULIA Community is the place to find the latest resources for SIMULIA software and to collaborate with other users. The key that unlocks the door of innovative thinking and knowledge building, the SIMULIA Community provides you with the tools you need to expand your knowledge, whenever and wherever.