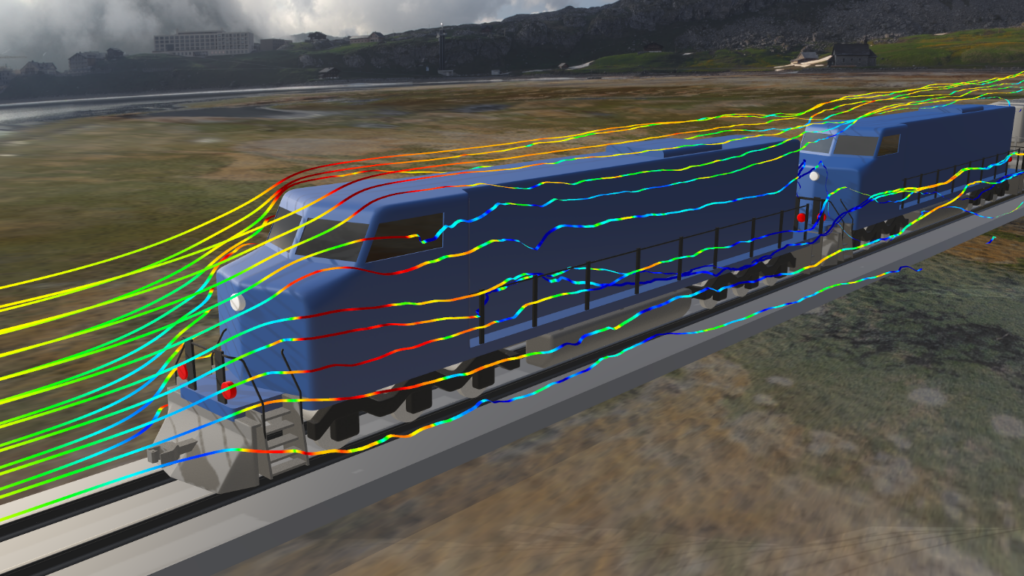
Train aerodynamics has a significant impact on energy efficiency and fuel consumption. Computational fluid dynamics (CFD) simulation (PowerFLOW) allows engineers to design trains to minimize air resistance, and to analyze aerodynamics long before wind tunnel testing.
The railway industry was one of the first to realize the importance of aerodynamics and drag. In the 1930s, iconic “Streamliner” locomotives such as the American Pioneer Zephyr, British Mallard and German Flying Hamburger reached speeds well in excess of 100 mph thanks in large part to their sleek designs, which reduced drag. Later, the success of the Japanese Shinkansen and French TGV made the streamlined “bullet train” nose famous and inspired a renaissance of high-speed rail that is continuing around the world to this day.
The importance of drag on high-speed passenger trains is obvious – aerodynamic drag scales with the speed squared, and it completely dominates other sources of resistance at high speeds – but it also affects the performance and efficiency of lower-speed trains – even freight.
How Fluid Simulation Helps the Rail Industry?
Simulation is the use of numerical methods to model physical behavior of systems. Simulation methods exist for many physics disciplines. In the rail industry, structural simulation and multibody simulation are well known for modeling the strength and dynamics of rail vehicles, but fluid simulation, or CFD, is also an important discipline for rail.
CFD models the flow of fluids such as liquids and gases around solid bodies and inside hollow bodies. The fluid flow gives rise to complex behavior such as turbulence vortices, boundary layers, wakes and jets, which need to be resolved with accuracy needed for engineering design. Among the simulation techniques used to capture this complex behavior are Reynolds Averaged Navier Stokes (RANS) and Lattice Boltzmann Method (LBM).
Computational fluid dynamics (CFD) simulation helps the rail industry to analyze and optimize the drag on locomotives and rail cars during design, well before prototypes and wind tunnel testing. Improving energy efficiency helps the train operator to reduce fuel costs and meet emissions targets. It also finds its way into analyzing many other areas of rail design, from reducing wind noise to optimizing air conditioning. This blog post will explain how SIMULIA PowerFLOW is used across the rail industry to power the CFD simulations that help them produce innovative new designs and remain competitive in the ever-changing transport landscape.
PowerFLOW for Rail CFD Simulation
The examples in this blog post were calculated using the Lattice Boltzmann technique in the tool SIMULIA PowerFLOW fluid systems.
SIMULIA PowerFLOW, developed over decades as a high fidelity and powerful fluids built for aerodynamics, aerothermal and aeroacoustics simulations of highly complex vehicles, such as an entire train with wakes and slipstream. It is highly automated, scalable to 1000s of compute cores, can work with complex imperfect geometry and does not require volume grid generation. PowerFLOW supports GPU acceleration to tackle even extremely large problems such as rail vehicles.
Benefits of Simulation in Train Design
The earlier a problem is identified, the easier it is to fix. By the time a prototype has been built and track testing starts, significant resources have been sunk into the design and there are numerous dependencies in the design. If an aerodynamic issue is discovered at this stage, substantial parts of the train might need to be redesigned, delaying the project and increasing costs significantly. Simulation allows a shift left approach – rather than waiting until the end to test the design, engineers can bring analysis forward (shifting it left on the timeline), reducing the risk of late-stage design changes and spiraling costs.
Simulation can also reveal the causes of effects that are difficult to understand through conventional methods. SIMULIA PowerFLOW offers clear, high-resolution, 3D visualization that makes air flow, heat distribution and noise propagation visible, allowing engineers to understand the root causes of problems and develop effective mitigation methods. Automated design of experiments (DoE) and optimization can explore numerous different scenarios quickly, including ones that are hard to test experimentally, and find optimal solutions to maximize efficiency across many operating conditions.
Overcoming Wind Resistance on Trains
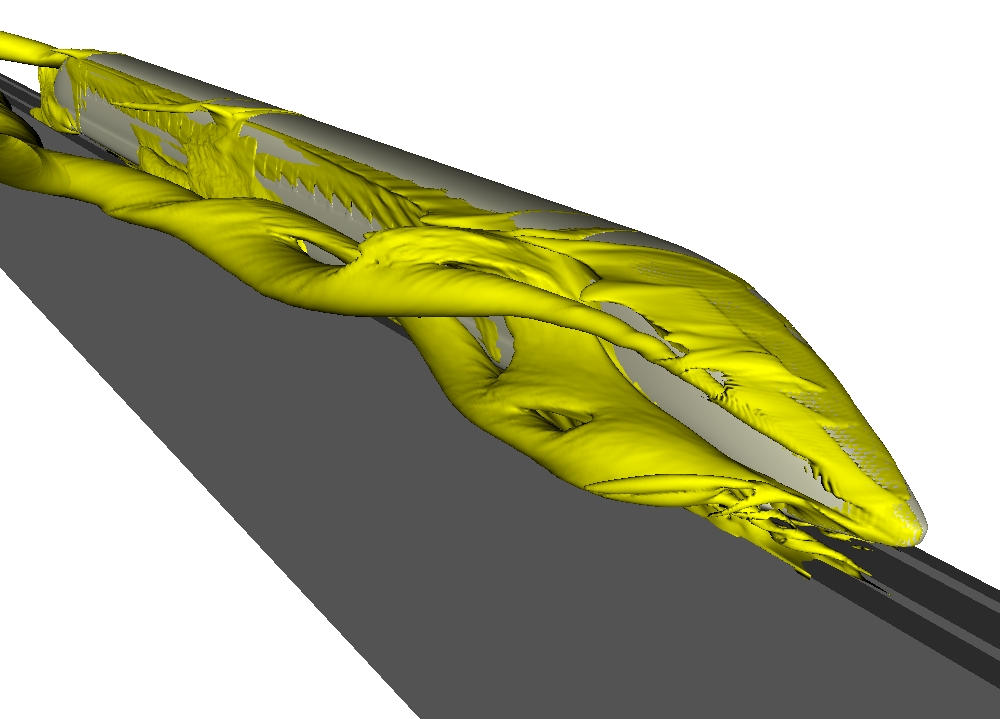
There are many potential sources of drag on a train – not just the front, but also the rear, the gaps between carriages or wagons, the underbody of the train, the pantograph on an electric train, and cargo on a freight train. Freight trains can be over a mile long and haul hundreds of containers. Each container will contribute a little bit of drag from the turbulent eddies that forms behind it, and the total drag can be significant.
Rail vehicle manufacturers can use SIMULIA PowerFLOW to optimize the streamlining of the locomotive and wagons, but railroads can also use it to optimize performance and save fuel in different operational scenarios. Simulation helps freight operators to optimally organize the containers and the space between them, and choose add-on aerodynamic fixes to reduce drag. Competing industries such as trucking are already using PowerFLOW to improve the aerodynamics of their vehicles, meaning the rail industry will need to improve drag too to maintain its competitive edge.
Aeroacoustic Train Noise Simulation
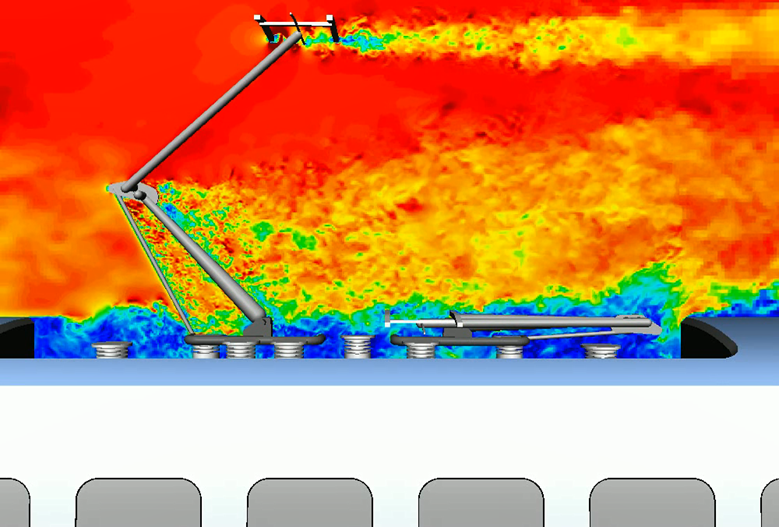
When the first dedicated high speed lines started operation, nearby residents complained of gunshot-like noises. Engineers realized that when passing through a tunnel the front of the train compressed air in front into a shockwave. Locomotives had to be redesigned to change their aerodynamics and tunnel entrances protected with hoods and perforations that act like a silencer. Aeroacoustic noise is one of the main sources of noise on a train.
Noise can be generated on any part of the train that causes turbulent airflow, as well as from the interaction of the train’s aerodynamic wake with trackside structures like bridges and overhead electrification. Simulation identifies these noise sources and helps designers to mitigate them through aerodynamic improvements or insulation. SIMULIA PowerFLOW has aeroacoustic simulation capabilities tightly coupled with aerodynamic. User can calculate the noise levels at any point around the train – and even listen to the simulated noise of the train itself to understand the passenger experience precisely.
Thermal Management and Climate Control on Trains
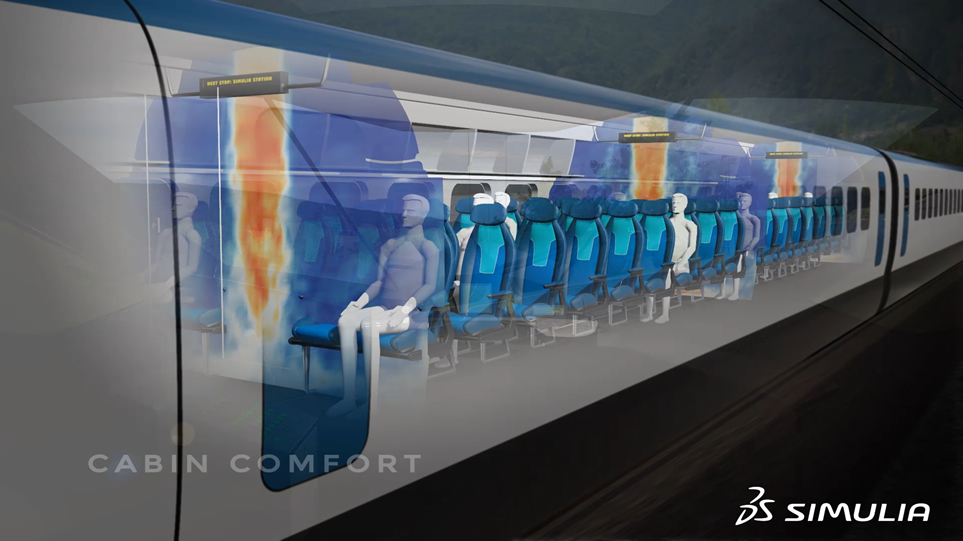
Engines, motors, transformers and brakes can generate massive amounts of heat, and need to be cooled efficiently in all climate conditions, both at speed and while stopped. Simulation can be used to design the fans and cooling systems of heavy machinery, modeling air flow and heat distribution within the engine. SIMULIA PowerFLOW can also model fan and vent noise. Simulation reduces the risk of thermal failures and allows engineers to right-size the cooling system to minimize cost and weight while still meeting targets. Even the noise from cooling system fans can be simulated and mitigated.
SIMULIA PowerFLOW can also be used to design the heating, ventilation and air conditions (HVAC) systems inside the cab and passenger space of rail vehicle. Here, crucial design requirements includes even distribution of treated air, the ventilation of the cabin, and the noise perceived by the passengers.
Conclusion
Aerodynamics is a crucial consideration in the development of rail vehicles – even at lower speeds, drag has a significant impact on energy efficiency and fuel consumption. Computational fluid dynamics (CFD) simulation allows engineers to design trains to minimize air resistance, and to analyze aerodynamics long before wind tunnel testing.
CFD simulation can also be used to analyze and optimize noise from trains in order to improve the passenger experience and increase acceptance by local communities. Coupled CFD-thermal simulation can also be used to design the thermal management systems for locomotive systems and to ensure that HVAC systems provide safe, comfortable environment for passengers.
SIMULIA PowerFLOW offers a full range of CFD simulation capabilities for rail vehicle development. Integrating CFD simulation using PowerFLOW into design workflows can accelerate locomotive development, increase KPIs such as fuel efficiency, right-size cooling and HVAC systems, and reduce the risk of late-stage rework that can add to design costs.
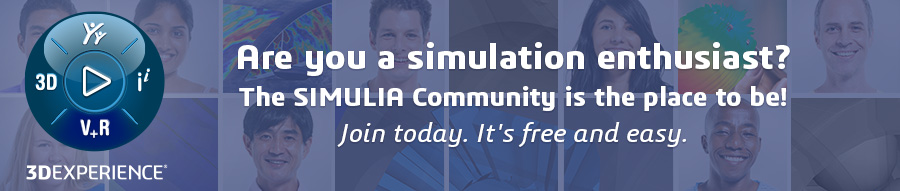
Interested in the latest in simulation? Looking for advice and best practices? Want to discuss simulation with fellow users and Dassault Systèmes experts? The SIMULIA Community is the place to find the latest resources for SIMULIA software and to collaborate with other users. The key that unlocks the door of innovative thinking and knowledge building, the SIMULIA Community provides you with the tools you need to expand your knowledge, whenever and wherever.