Bringing a new generation of cars onto the road requires new solutions and applications that will better integrate engineering disciplines to help engineers look at vehicle performance in a new, more holistic way. Learn more at our dedicated page, Trust the Drive.
Passenger comfort is important in all vehicles, but in electric vehicles there needs to be a special focus placed on the noise and vibration behavior of the electric drive system, as the general noise level is much lower than compared to internal combustion engine vehicles. Electric drive units, which are typically an integration of an electric machine and a gearbox in the same housing, are complex mechatronic systems and prone to producing tonal noises.
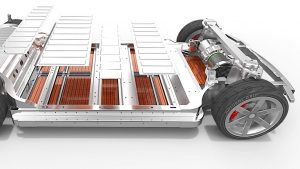
These tonal noises are caused by mechanical vibrations with each mechanical system having a characteristic set of eigenfrequencies excited by many different mechanisms. The two main effects for electric drives are the electromagnetic forces inside of the electric machine and the dynamic gear contact forces. If the frequency of the excitation mechanism is matching an eigenfrequency, then this can cause a vibration response with high amplitudes, described as a resonance. These vibrations are then either directly radiated from the gearbox housing or transferred indirectly through the mountings into the vehicle chassis.
The simulation models for solving the vibration problem can become very large and difficult to solve if only finite element methods are considered. To achieve high efficiency in the simulation process, and being able to cover the entire operating range of the system in a reasonable time, it is necessary to build reduced models with exactly the same level of detail required for this type of system analysis. Multibody system (MBS) simulation is perfectly suited for this purpose. It also uses reduced flexible representations of all structural components and efficiently provides application specific modeling elements with analytical formulations for including nonlinear effects from the gears and bearings. It also provides interfaces to other simulation domains, for example, it includes electromagnetic forces coming from an electromagnetic finite element simulation. These multibody systems will then have a relatively low number of degrees of freedom, which makes them very efficient to solve while containing all necessary information to accurately cover the system dynamic behavior in the desired frequency range.
Further, for engineers to easily run design trade-off studies, parametric optimizations ultimately arrive at an optimal design configuration, the holistic use of parametric models and standardized processes are essential. Structural, electromagnetic, MBS, and acoustics simulations can be integrated using the 3DEXPERIENCE platform as a coupled multi-physics simulation framework for the multi-domain noise and vibration analysis. Additionally, the framework places emphasis on automated model updates and process execution, which dramatically reduces the time and effort to study numerous design alternatives and reduces the risk of incorrect simulation results due to mistakes in manual process execution.