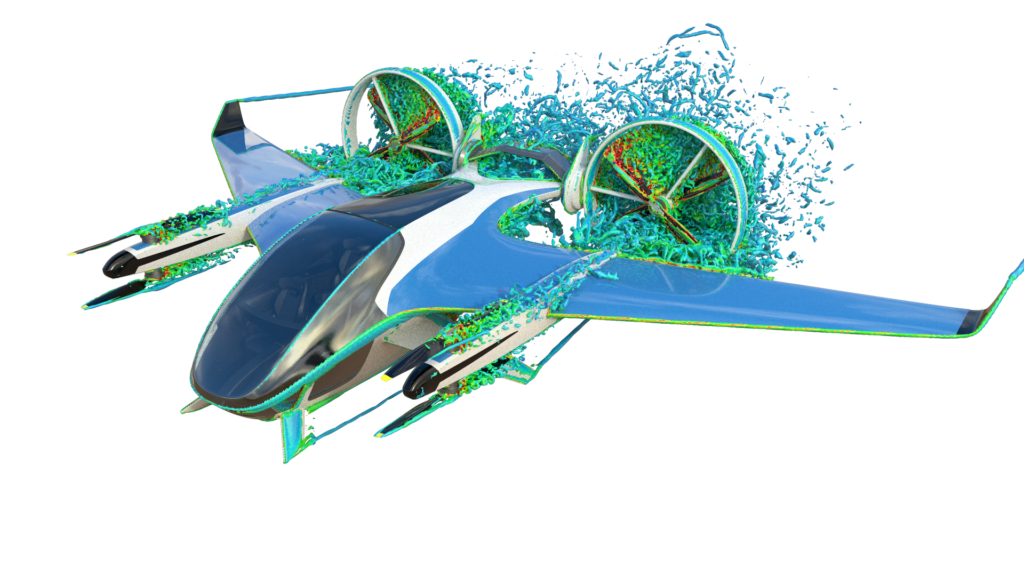
Design, Build, Test
In the beginning, before simulation, products were produced using a “design-build-test” approach in which physical prototypes are built, then tested in a lab or proving ground, to determine how the product would function in the real world. While this approach is still widely used today, design-build-test no longer best serves the needs of industry as many processes, requirements and regulations change and evolve.
Problems Industry Faces
There are several challenges that the industry must address when designing products. One problem industry faces is schedule and cost risk. A producer has no way to know how long or how expensive the design process will be – there is no way to predict how many back-to-the-drawing-board cycles will be needed to clear all of the design issues discovered during testing.
A second problem is testing expense. Testing requires a large investment in time, people, expertise, and facilities. Separate organizations, personnel, equipment, and locations are required, all with their own schedule. And in order to maximize the productivity of that investment, testing capabilities must be kept fully booked, implying that any particular product designer is going to have to wait his or her turn on the test calendar.
Another more subtle problem is liability. The history of commercialism is replete with examples of shoddy, dangerous products, exaggerated performance claims, and empty promises of benefits not delivered. With the Magnusson-Moss Warranty Act of 1975 in the United States (and similar statutes in other countries), producers became liable for products that do not live up to their claims. This liability cannot easily be managed by a design-build-test approach because you cannot possibly physically test all the ways a product will be used.
Enter Simulation
It is a remarkable coincidence that at the same time that producers began feeling the heat of poor product quality, computers became more capable, and simulation software became more powerful. Simulation began to address the cost, expense, and gap between the test lab and the real world.
At first, Simulation was employed as an afterthought to design, often to help firefight warranty issues when a product didn’t work correctly. Simulation was deployed in corporate research centers far from the design department, running on expensive in-house mainframes by experts with advanced degrees.
Gradually, as the software became more capable and computers became affordable at the department level, simulation began to be used to certify product performance as a complement to testing and became more trusted. Simulation users were still dedicated experts with a different reporting line than designers, but were more accessible.
Today, computers are everywhere. Design is done by powerful computer-aided design systems. Corporate research centers are mostly a thing of the past, and simulation has become a common part of the engineering toolset, available 24/7/365, and recognized as a value-added activity to improve product design and performance in most industries.
The Future: MODSIM
Yet still, simulation and design are separate activities, often separate personnel, separate departments with separate expertise, separate software experience, and separate budgets. Simulation and design remain siloed.
Companies want to remove this barrier. They want to take the next logical step to left-shift simulation into the core of design – to use simulation to its fullest potential to eliminate risk, bring products to market linearly (no design re-cycles), and have these products perform as expected and last as long as planned. They want simulation to help the entire product life cycle from ideation to end-of-life and recycling. And they want simulation to help reduce the recurring problems of risk, expense, and liability.
Unfortunately, our siloed engineering culture still currently prevents this. Simulation will only fulfill its potential when it shed its siloed legacy and become central to design. For this to happen, simulation methods need to be embedded in the design environment and become a part of the design experience. Simulation tasks need to be automated. Simulation expertise needs to be captured. Simulation best-practices will still need expertise to be developed. But once developed, those processes will need to be codified, maintained, and provided appropriately to accelerate design.
Design methods also need to transform. Design exploration in a virtual environment (using simulation to explore hundreds or thousands of design alternatives) will be commonplace. Learning will have to be embedded in design so that the design system will organically become more powerful with time. Designers will need to see simulation as an extension and amplifier of their own capabilities. In short, simulation will become design. And industry will benefit from the unification of these two powerful capabilities into one ideology: Modeling and Simulation (MODSIM).
The next two blogs in this series will explore how this is happening today and where this Modeling and Simulation transformation will take us tomorrow. Stay tuned!
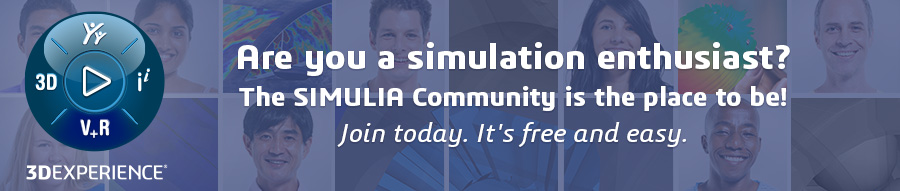
Interested in the latest in simulation? Looking for advice and best practices? Want to discuss simulation with fellow users and Dassault Systèmes experts? The SIMULIA Community is the place to find the latest resources for SIMULIA software and to collaborate with other users. The key that unlocks the door of innovative thinking and knowledge building, the SIMULIA Community provides you with the tools you need to expand your knowledge, whenever and wherever.