The control and switching of power requires high reliability and safety and is subjected to strict regulation. The design of switchgear and other system components has also targeted new insulation media such as gas and oil to meet environmental standards. For many decades, research has targeted a replacement for the SF6 commonly used gas insulated switchgear. Many alternative mixtures based on CO2 mixtures have been proposed but obtaining the electrical and thermal properties of such mixtures is difficult. In this blog, an electro-thermal simulation is summarized which was applied to a load break switch under steady state conditions with CO2 gas as the insulating medium. Increased temperature has adverse effects on the aging and performance of the equipment. Such numerical simulations can be applied to other power equipment, such as transformers, and extended to include establishing dielectric breakdown risk and structural integrity.
Electricity, a natural phenomenon, has become an indispensable part of modern life and has, for over more than a century, transformed society. An electric power system is defined as a network of electrical components to generate, transmit and distribute electric power. Switchgear is responsible for the control and regulation of power in modern power transmission and distribution systems.
Thermal management is a very important issue in medium voltage switchgear design. Temperature rise plays an important role in the safe and reliable operation of equipment. Excessive temperature rise can lead to performance degradation, accelerate thermal ageing and consequently reduced equipment lifetime.
Since the 1960s, sulfur hexafluoride (SF6), with its excellent insulation, thermal and arc-quenching properties, has been hugely successful in the continued development and application of compact, metal-enclosed medium voltage switchgear. However, SF6 was one of six Greenhouse Gas (GHG) categories targeted by the Kyoto Protocol in 1997. Its Global Warming Potential (GWP) is 23,500 worse than CO2. Efforts to find alternative gases and gas-mixtures had already been the focus of research for several decades. The inferior thermal performance of alternative gases means that thermal design is more critical in the design of future medium voltage switchgear.
The optimization of existing switchgear, as well as the development of future devices, requires the knowledge to predict the temperature rise of the equipment during the different iterations of the development process. In order to shorten the product development cycle, it is important to reduce the number of prototypes or, where possible, even eliminate them entirely. Simulation also aids in anticipating and mitigating potential design issues as well as post-failure analysis. It is an indispensable tool that allows the prediction of the temperature rise due to normal and excessive load conditions, manufacturing tolerances and defects, ambient temperature, and changes in gas mixtures.
Simulation reduces the risks involved in significant design changes aimed at, for example, cost, compactness and size. The volume of the equipment is determined by conflicting design constraints, namely, insulation strength, thermal stress, current carrying capability and mechanical stress. To ensure safe operation, dimensions and minimum distances between components must be determined.
Steady State Thermal Design of a Load Break Switch
The device used in this study is a G&W Electric Rotary Puffer (RP) type, two-position switch. This is ideal for manual load break switching, sectionalizing applications rated through 25kV, 630A continuous current. The intention is to establish temperature rise for both SF6 and CO2 gas types. CO2 was chosen since many proposed alternatives use this gas in their formulation. Any arbitrary gas mixtures can be simulated provided that information about their gas physical and thermal properties is readily available. The complete study can be found in the paper at the 22nd International Symposium on High Voltage Engineering, Xi’an, China 2021.
A fully featured CAD model of the load break switch shown in Figure 1 was imported.
This model serves as a master model for a combined electro-thermal workflow based on a low frequency solution for electric current flow in the three-phase conductors at 60 Hz and a Conjugate Heat Transfer solver (CHT). The workflow is performed in single user interface and enables automatic and seamless connectivity between the simulation types.
In order to model the physics correctly, it is critical to include the contact resistances at critical joints in the current conductors. These contact resistances lead to temperature rises in the device. However, contact resistances depend on materials and construction e.g. applied torque. There will be significant variance between their values in the equipment. These values can be measured at strategic locations and their values integrated into both the low frequency and thermal models. The low frequency losses are automatically imported into the CHT model. Eddy current and thermal results are shown in Figure 2.
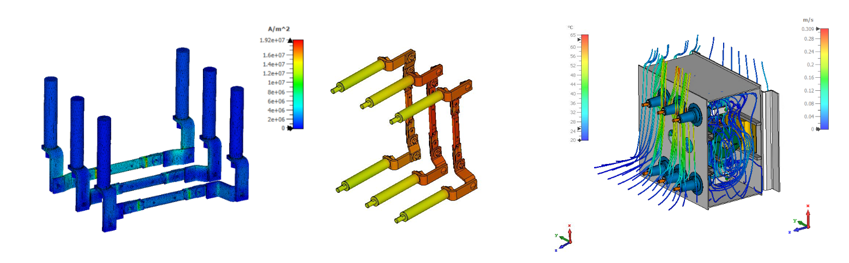
A verification of the process is shown in Figure 3. The strength of simulation is that parametric analysis allows the operating conditions to be investigated. Simulation results for both SF6 and CO2 at nominal and increased load are shown in Figure 3. Overloading, as expected, leads to dangerously high temperatures. Such studies enable margins to be determined in the design phase.
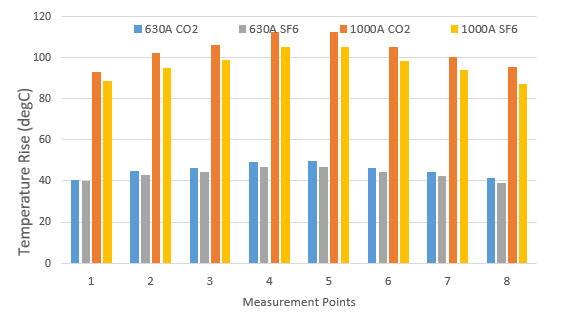
Additional Design Studies
Switchgear have several functions and require equally important workflows to simulate critical physical processes under operating and transient conditions. A fundamental performance indicator in a switchgear is its dielectric breakdown performance at nominal voltage and overvoltage due to short circuit conditions e.g. system, lightning strikes etc. Estimating the discharge or breakdown levels are subject to stringent regulation and standards. A typical switchgear consists of many subcomponents such as disconnector, earthing switch etc. all of which need to be individually designed to ensure compactness under the constraint of cost, size, safety and reliability. Changes to the design may adversely affect the thermal and structural performance.
The breakdown phenomena is an extremely complicated physical process. The streamer criterion methodology is a widely accepted approach commonly applied in the industrial design of switchgear as well as in transformers and other power system components. This method takes advantage of highly efficient electrostatic simulations which can be automated for use in design departments. Such design work is commonly carried out by R&D departments.
A simple example of a medium voltage switchgear is presented in Figure 4. The user simply enters the material data and attributes voltage levels for each of the three-phase conductors under the assumption of an arbitrary short circuit condition. The streamlines are automatically calculated within the device or at locations of interest specified by selecting relevant surfaces. A post-processing step carries out the streamer calculation to establish the inception and breakdown voltages. The streamlines emanating from these locations can be visualized. Surface fields or streamline-based results can be used to optimize the topology or distances between components as well as determine safe margins of operation.
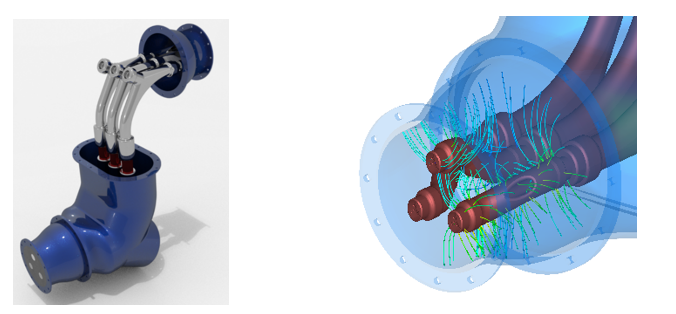
Ensuring a good design entails such a risk assessment. Designers can combine CAD modelling with simulation to rapidly and, with minimal finite element experience, modify previous or propose new designs. Shorter lead times can be the make or break in the sales process and depends on highly efficient workflows to achieve it. Topological optimisation can also play a significant role in proposing radical designs – another differentiator in the switchgear market.
It is important to establish the mechanical stresses that switchgear are subjected to under short circuit conditions. A transient low frequency solution provides the forces on bus bars at particular instances in time during a system fault. These forces are consequently used to determine the structural integrity of the system e.g. optimal location of conductor supports. Figure 5 shows the deformations in the switchgear resulting from a typical fault. This simulation can be integrated into the overall switchgear design process.
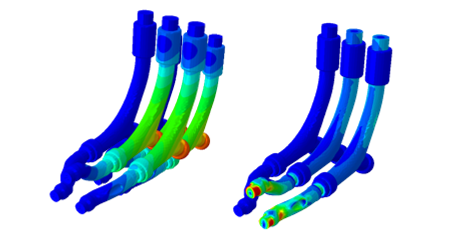
Other variations of the aforementioned workflows are available to target particular design and development aspects such as transient short circuit thermal simulation, partial discharge measurement and sensor placement, the modelling of very fast transients (VFT). Furthermore, these workflows are general and not unique to switchgear.
Conclusion
This blog has demonstrated the ability to use multi-physics based tools to help in the design of switchgear equipment. Such equipment is expensive and is subject to strict reliability and safety regulations and simulation can significantly reduce the development process. Switchgear are complex devices that require bespoke design – designs need to be adapted to challenging applications where space is at a premium. The compactness is only achievable with a highly performant gas such as SF6 but switchgear manufacturers are challenged with the development of environmentally friendly alternatives whilst retaining excellent reliability and ensuring safe operation.
Not only can obligatory tests be simulated but also additional value can be added by simulating optional tests with minimal additional effort. This enables manufacturers to demonstrate the rigorous development of their equipment. Longevity and return on investment are decisive in the acquisition of equipment that is expected to operate reliably over many decades. Maintenance is key to this and simulation can help to better understand the complex processes and improve and introduce diagnostic procedures aimed at ensuring high reliability.
Any equipment with high voltages and currents are subjected to the same rigorous test regulations and hence would equally benefit from simulation.
SIMULIA offers an advanced simulation product portfolio, including Abaqus, Isight, fe-safe, Tosca, Simpoe-Mold, SIMPACK, CST Studio Suite, XFlow, PowerFLOW and more. The SIMULIA Community is the place to find the latest resources for SIMULIA software and to collaborate with other users. The key that unlocks the door of innovative thinking and knowledge building, the SIMULIA Community provides you with the tools you need to expand your knowledge, whenever and wherever.