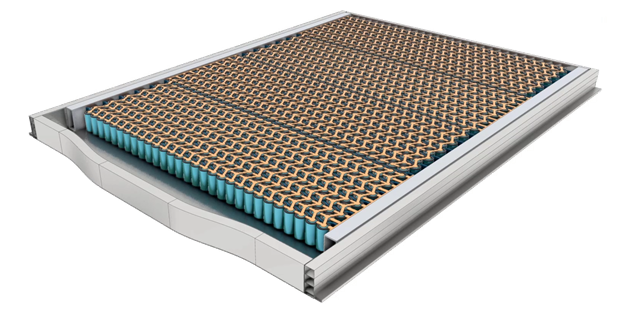
Electric vehicles require massive energy storage—the battery is often the single heaviest component of the entire vehicle. The battery pack consists of hundreds or thousands of cells arranged into multiple modules, control electronics, power distribution and cooling systems.
In previous blog posts, we’ve examined how modeling and simulation (MODSIM) is used to design individual battery cells. In this post, we show how MODSIM can also be used to analyze and optimize the numerous factors engineers need to consider for a successful battery pack design. We will discuss vibration, sealing, fatigue life, crash safety and thermal management.
Challenges of Battery Module and Pack Engineering
The battery pack is critical to the vehicle’s performance and must be able to withstand the forces of hard driving. Car batteries are subject to constant vibration and stress, leading to progressive fatigue in components over years of use.
Any damage to a battery cell can potentially lead to thermal runaway and a serious fire, and with so many battery cells carrying many kWh of energy, safety is a critical engineering consideration. Battery pack engineers must ensure the battery is as protected as possible, even in crash scenarios.
However, creating a more robust battery body design can potentially increase the battery weight and reduce the vehicle’s energy efficiency and driving range. A delicate design process and careful trade-off analysis is needed to ensure vehicle safety while maximizing range and performance.
The electrochemical reactions in the battery cells and the high currents in the busbars can generate significant heat. Electric vehicle battery packs need dedicated cooling and heating systems and reliable airflow even when travelling at speed in variable weather conditions.
Developing a battery pack is therefore a multiphysics, multidisciplinary task that requires input from many different departments. All stakeholders in the project, which will often involve many companies at various parts of the supply chain, need to collaborate. Too often, designers and analysts work in silos, resulting in delays and unnecessary compromises in the design.
A MODSIM Workflow for Battery Pack Engineering
The alternative to siloed processes is unified modeling and simulation (MODSIM). In MODSIM, modeling using computer-aided design (CAD) tools and simulation are brought together into a single unified workflow on a common platform. Geometry from CAD can be used to build simulation models with minimal rework. At any stage in development, from the initial concept to final manufacturing, the designer can analyze the design with simulation to understand its performance without constructing and testing prototypes.
The Dassault Systèmes MODSIM solution for Battery Module and Battery Pack Engineering combines the industry standard CATIA design tool with the powerful, trusted simulation tools from SIMULIA and requirements management and results analysis tools on the 3DEXPERIENCE platform. In this MODSIM solution, many battery pack analyses can be carried out on a virtual twin of the real battery.
Shaking Table
Shaking table testing replicates the vibration that a battery will experience during driving. In the virtual shaking table analysis with MODSIM, engineers can simulate years of driving in a single simulation. After constructing the module or pack model, the engineer first performs a static analysis for bolt pre-tensioning and a harmonic analysis to identify vibrational modes of the battery pack. This information helps to identify salient locations for bolts and fixtures.
The resulting vibration data is then imported into the SIMULIA tool, fe-safe. This calculates fatigue on the battery pack, highlighting possible failure locations and estimating the fatigue life of the product. Engineers can then optimize designs to find the best trade-offs for improved fatigue life.
Drop, Shock, Impact, Rollover and Crush
Battery packs, which are usually tested to destruction, have many potential damage scenarios. Crash testing can be replicated virtually without the need for battery pack prototypes. The user can import regulatory or internal test requirements, test procedures, and validation data into the Requirements Management app in the 3DEXPERIENCE platform so all stakeholders are working to the correct test specifications.
The geometry is imported from the CATIA tool and prepared for testing. For example, a crush and penetration test adds a metal piston set up to produce a specific force as specified by the test requirements. If required, the geometry of the entire vehicle can also be included. The user executes explicit dynamic analysis and explores the results to identify areas of deformation, damage, stress and strain. As all specifications are on the platform, KPIs can be immediately checked against requirements, and design changes can be made if needed.
Seal Durability
Battery packs need to be well sealed to prevent the ingress of water and dirt from the road and the leakage of electrolytes. Simulation can model the seal’s performance under pressure, not only for a newly manufactured battery pack but also after years of aging.
The user can generate a simulation model of the seal, including the hyperelastic properties of the material. The simulation considers assembly loads (bolt loads) and ballooning caused by positive internal pressure of 100-250 bar. It reveals likely failure points and leak paths, helping engineers design the optimal fixtures. The simulation can also consider the impact of aging on the sealing performance and degraded bond strength.
Battery Thermal Management
Just as internal combustion engine vehicles require radiators for the engine, electric vehicles require battery cooling systems. Increasingly, EV battery packs use both liquid cooling and air cooling – individual modules use glycol or a similar coolant to conduct excess heat to a heat exchanger, from where fan-driven air cooling removes the heat from the battery. To increase efficiency, battery packs also include heating systems for cold weather.
The first step is to simulate the heating of a single cell. For more information, see our blog post on battery cell engineering. Once this is available and validated, the engineer can construct the module or pack model. Thermal simulation considers the duty cycle of the battery module and the cooling/heating condition. Different scenarios can be modeled – for example, charging versus driving. A combined computational fluid dynamics and conjugate heat transfer (CFD-CHT) simulation is used to model coolant and air flow through the cooling system and the resulting heat distribution. Simulation over a transient duty cycle shows how much the system heats up over time.
With the simulation results, engineers can review key results such as temperature, heat rejection and flow resistances and compare them against the specifications and requirements easily.
Benefits of the Dassault Systèmes MODSIM Solution
Performing the four workflows discussed in this article requires structural, thermal, CFD and vibrational simulation. Integrating battery cell engineering into this workflow adds electrochemistry as well. All these simulation technologies are brought together in the SIMULIA product portfolio, with powerful solvers proven by decades of industrial use. Multi-physics simulation integrated in the 3DEXPERIENCE platform enables a unique level of multi-disciplinary trade-off studies for battery pack engineering.
MODSIM also breaks down the silos between designers and analysts with fully modular, flexible and parameterized workflows. Battery cell, module and pack designs from CATIA can be imported directly into SIMULIA simulation tools, making parametric design studies and optimization possible. Optimized designs can be passed straight back to the designers, providing unparalleled design and analysis capability.
MODSIM workflows on the 3DEXPERIENCE platform include substantial automation, robust meshing and connection creation. This accelerates the development process and reduces manual work to fine-tune the model and solution parameters.
Implementing MODSIM in a battery pack engineering workflow accelerates product time-to-market by assisting designers and engineers while minimizing the need for physical prototyping and testing. Replicating testing on a virtual twin of the battery pack reduces the risk of problems emerging later, potentially leading to expensive and time-consuming rework or recalls.
Conclusion
Battery modules and packs require careful design to optimize their performance. Engineers need to ensure crashworthiness and robustness while keeping battery weight at an acceptable level. They must also manage multiphysics environmental risks, including vibration, heating and leakage.
Simulation gives engineers the tools needed to analyze battery pack performance, reliability and safety early in the design process – before constructing a physical prototype. The battery module and pack engineering solution on the 3DEXPERIENCE platform combines the multiphysics simulation tools needed to tackle various battery pack design problems. The unified modeling and simulation (MODSIM) approach means that simulation can easily be connected to design tools. It combines battery module and pack analysis with battery cell design and full-vehicle system integration in a typical workflow.
Keep reading:
- Accelerate and Optimize the Design of High-Performance Batteries
- Build Better Battery Cells with Simulation-Driven Engineering
- Unleash the Secrets of Simulation for High-Performance Battery Cells
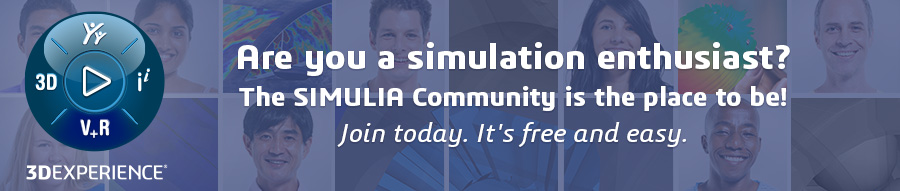
Interested in the latest in simulation? Looking for advice and best practices? Want to discuss simulation with fellow users and Dassault Systèmes experts? The SIMULIA Community is the place to find the latest resources for SIMULIA software and to collaborate with other users. The key that unlocks the door of innovative thinking and knowledge building, the SIMULIA Community provides you with the tools you need to expand your knowledge, whenever and wherever.