Introduction
The electric vehicle (EV) industry is making great strides towards sustainable mobility, pushing the boundaries of what’s possible with clean energy. Although EV sales currently account for around 16% of the global market, they’re expected to rise sharply to 50% by the end of 2035 (see figure 1) as manufacturers work to overcome significant challenges like manufacturing challenges such as material availability for battery and electric components, as well as availability of charging infrastructure, to vehicle thermal challenges such as battery range and thermal comfort, cost of EVs to be on par with ICE vehicles, model proliferation, multi-physics engineering development, range anxiety etc. Among the most pressing of these are battery efficiency and occupant comfort, particularly under varying climatic conditions.
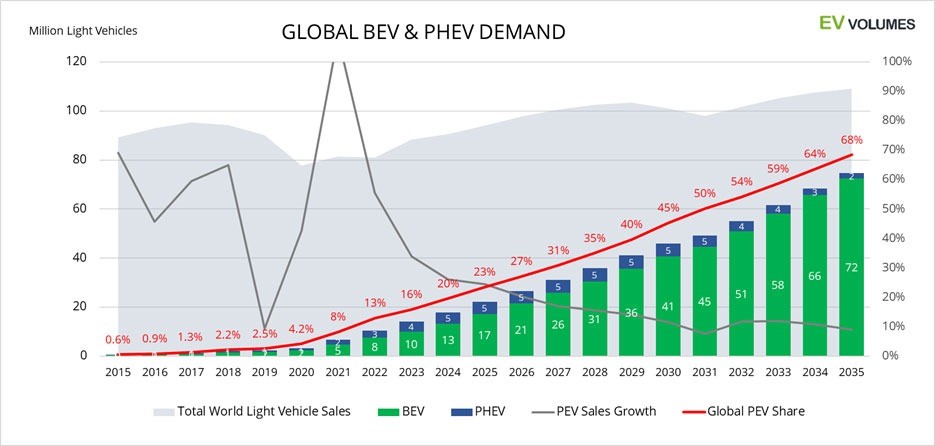
In colder climates, for example, EVs lack the waste heat from internal combustion engines that would otherwise help heat the cabin. This leads to increased power consumption by climate systems, which in turn reduces battery range. This blog explores how Dassault Systèmes employs cutting-edge simulation technologies and advanced computational tools such as Computational Fluid Dynamics (CFD) and 1D system modeling to accurately simulate and optimize these complex interactions and thereby improving both battery efficiency and cabin comfort in EVs.
Motivation: Why Thermal Management is Key for Electric Vehicles
Thermal management directly impacts an EV’s performance, as it influences both the efficiency of the battery and the comfort of passengers. In comparison to ICE vehicles, EVs must expend additional energy to heat the cabin, which can reduce range by more than 15% in hot or cold conditions and the range can drop by up to 40% in extreme weather conditions (see Figure 2).
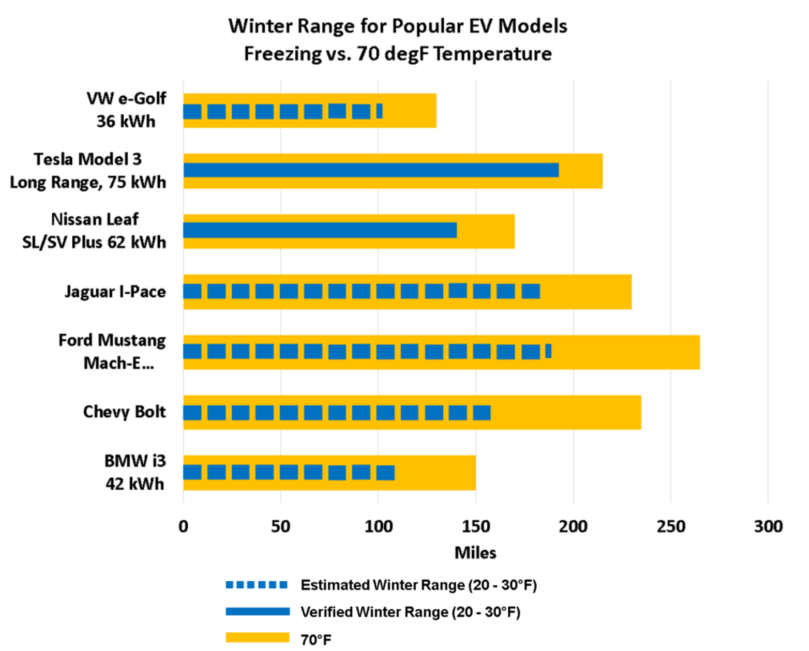
Thermal comfort is particularly relevant to drivers in extreme climates who rely on climate control features like seat warmers, cabin heaters, and defrosters. These features consume a significant portion of the EV’s battery power, creating a trade-off between energy used for passenger comfort and energy available for range.
Challenges in the EV Thermal Management Landscape
Real-world applications come with their own set of challenges. Extreme temperatures, complex thermal interactions, and fluctuating driving conditions all impact energy consumption in ways that require ongoing refinement of EV designs. For instance, urban stop-and-go traffic cycles and high-speed highway driving affect airflow and cooling needs differently, meaning that a single HVAC configuration is unlikely to suit every scenario.
Beyond comfort, EV designers also face the task of balancing battery health and efficiency. Batteries perform optimally within a specific temperature range. Excessive heating or cooling can accelerate degradation, affecting long-term performance and lifespan. Advanced simulations like those used in this study help identify the optimal trade-offs between battery protection and energy efficiency.
The Role of Advanced Simulation: To tackle this challenge, Dassault Systèmes has leveraged a co-simulation approach that integrates detailed 3D CFD models with system-level models. This approach allows engineers to simulate how heat moves through the vehicle and how energy is used by the climate system, helping to optimize both comfort and efficiency.
Methodology: A Multiscale Approach for Better Range and Comfort
A study conducted by Tesla shows that in electric vehicles, optimizing one of the components individually results in 15-25% improvement in e-drive efficiency, whereas optimizing the overall system as a whole improves the e-drive efficiency by 40%. Range is a problem, which should not be looked at through a single component in the system, but as a vehicle overall.
An advanced virtual twin can effectively assist in determining the optimal size of the HVAC system while enabling early-stage predictions for battery life, vehicle range, and passenger comfort. This study utilizes a co-simulation approach combining system-level and 3D CFD models i.e., by merging the results from 3D thermal optimization into overall system to optimize the efficiency to capture complex, multi-scale interactions and enhance overall vehicle performance. Through the integration of 3D CFD with Finite Element Analysis (FEA) thermal models, this approach provides precise predictions of passenger comfort levels and battery temperature distribution. Furthermore, by incorporating Dymola system behavior models, real-world driving scenarios for all vehicle systems can be simulated. 1D system simulation is performed with Dymola and the heat exchanger inlet temperatures are determined and provided as input to the 3D CFD simulation. As a next step, 3D CFD simulation is performed with PowerFLOW / PowerTHERM and the cabin outlet temperature is provided back to the 1D system model as input and the cycle repeats (see Figure 3). This approach benefits from the detailed response trends provided by 3D CFD analysis, facilitating quick adjustments via 1D models to optimize vehicle performance.
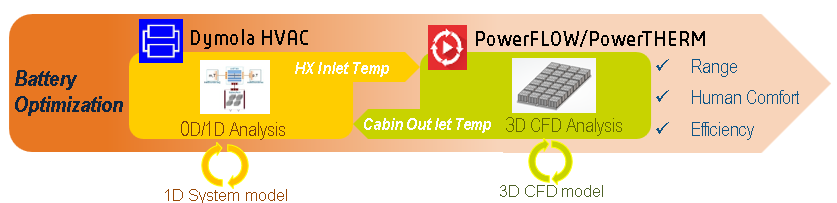
Additional 3D CFD analyses assess Underhood airflow, allowing engineers to characterize how external air affects the HVAC heat exchangers under various conditions. This airflow data is then applied to the 1D HVAC system analysis to establish realistic boundary conditions.
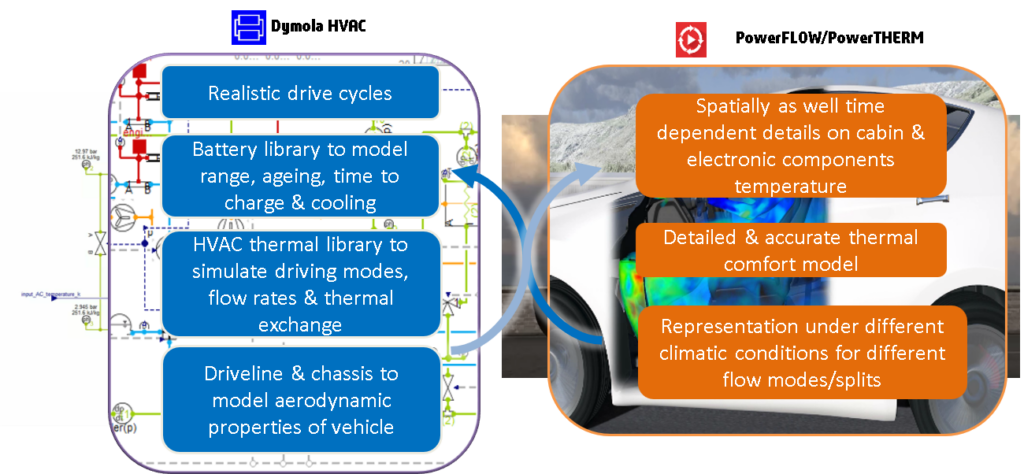
System Model
The first step is creating a 1D model of the HVAC system using Dymola, which assesses energy consumption, cabin temperatures, and vehicle range under different drive cycles, vehicle aero changes and HVAC modes. This model helps determine the size and power needs of the HVAC system to balance thermal comfort with battery efficiency. Dymola Modelica library offers a wide variety of predefined models and libraries that make our life easier in modelling the system models, like…
- Realistic drive cycles for various speeds (for e.g., high and low WLTP drive cycles)
- Battery library to model range, ageing, time to charge and cooling
- HVAC library to model driving modes, flow rates and thermal exchange
- Driveline and Chassis to model aerodynamic properties of vehicle
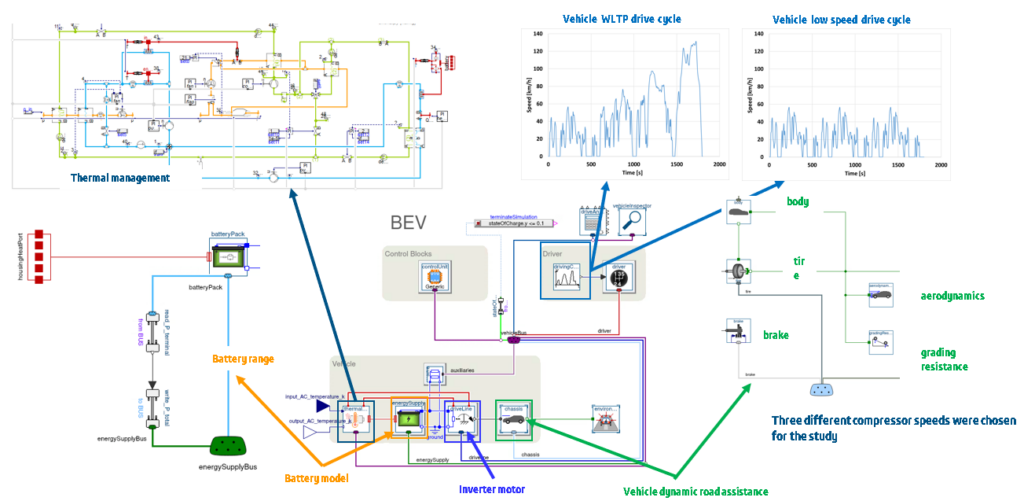
3D CFD for Localized Thermal Comfort
Using CFD simulations, one can analyze how heat moves through the cabin, affecting each passenger’s thermal sensation alongside the temperature of electronic components like display monitors, mobile rest etc. This level of detail provides a realistic view of representation of different modes for different climatic conditions and comfort across different body areas and helps inform design decisions for optimal airflow and heating distribution.
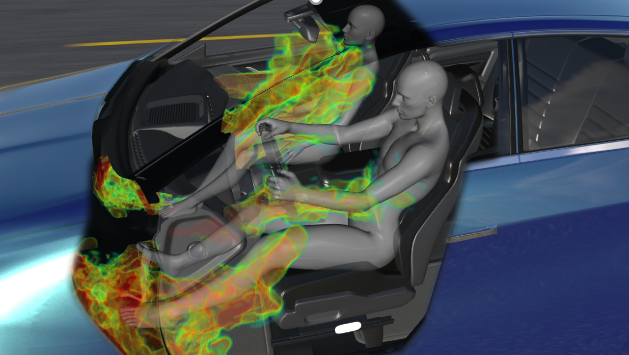
Underhood Cooling Airflow Analysis
A separate 3D CFD model simulates airflow around the vehicle’s heat exchangers, which are part of the HVAC system. This analysis captures how external air impacts cooling and heating, allowing for realistic boundary conditions and ensuring that all HVAC components operate efficiently.
The initial step involves using detailed 3D CFD analysis to characterize the external airflow that reaches the front end of the HVAC system’s heat exchangers under various vehicle operating conditions. A drive-cycle-specific Design of Experiments (DoE) approach is applied to select sample points that comprehensively represent these conditions based on their frequency of occurrence. This process, illustrated in Figure 7, defines the entire approach for characterizing airflow beneath the hood.
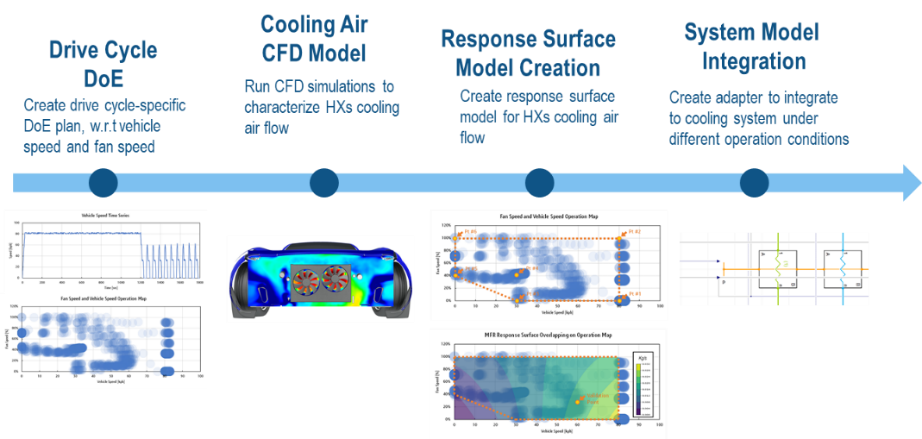
Next, CFD simulations are conducted for each sample point to determine the heat exchanger’s inlet mass flow rate and back pressure. A response surface model is then constructed using 2D linear interpolation to estimate values between these sample points. This model provides realistic boundary conditions for the 1D HVAC system analysis, allowing further simulations with accurate inputs for the heat exchangers.
Real-World Application: Analyzing Drive Cycles and Compressor speeds for Optimal Efficiency and Comfort
A transient coupled 1D-3D simulation was conducted on a compact passenger EV. This vehicle features a battery pack of 384 prismatic cells with a total capacity of 15.6 kWh. The HVAC system is designed to cool the cabin in summer and serve as a heat pump during winter. For this analysis, the focus was on a cold-weather scenario, simulating a drive in -10°C ambient temperatures for 30 minutes physical time, driver and passenger human comfort model and 60% face, 40% foot HVAC flow split mode.
The Worldwide Harmonized Light Vehicles Test Procedure (WLTP) drive cycles were used, as it reflects typical urban and highway driving patterns globally. The simulations explored two different drive cycle speeds, a regular drive cycle and an additional low-speed WLTP cycle to represent city driving, allows for realistic evaluation of the HVAC system under variable conditions. Three different compressor speeds high, medium and low were analyzed in the study, with particular attention on the HVAC system’s energy consumption, as it directly impacts passenger comfort. Additionally, the expected range for each configuration was estimated by analyzing the battery’s state of charge at both the start and end of the drive cycle.
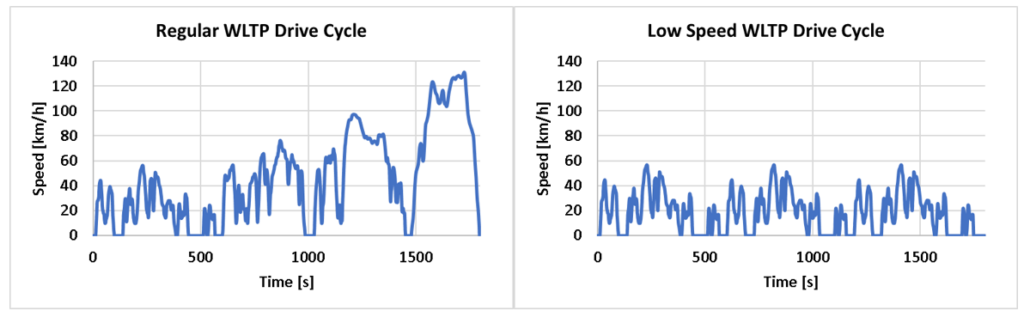
Results
The thermal comfort levels achieved are comparable across all three scenarios. After 10 minutes, occupants feel comfortable in each case. The high compressor speed scenario reaches comfort level 0 in 4.5 minutes, the medium speed in 6 minutes, and the low speed in 6.5 minutes. After 10 minutes, the low-power scenario offers the same level of comfort as the high-power scenario while consuming 50% less energy. Further analysis indicates that overall comfort is primarily influenced by the comfort level of the body’s breathing sensation. This breathing sensation is less affected by design variations among the three speeds compared to other body parts, resulting in a smaller-than-expected overall change in comfort.
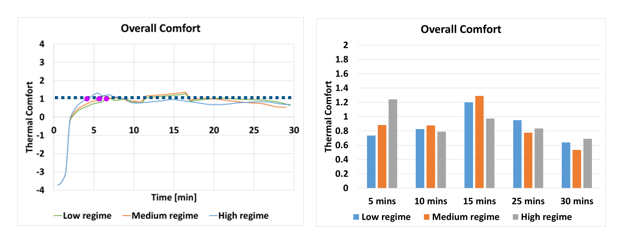
Medium and high compressor speeds consume 33.5% and 50.2% more energy compared to low speed. Moreover, at low compressor speeds, the battery drained more slowly, providing a range increase of up to 21% under some drive conditions. This test showed that reducing HVAC power can significantly enhance range without sacrificing passenger comfort.
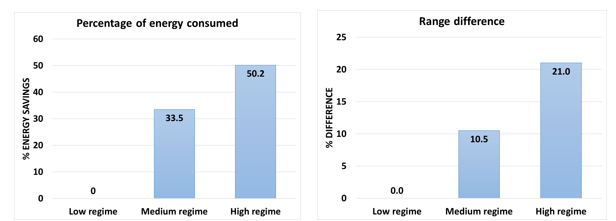
- High Speed: Achieves maximum comfort quickly but consumes more energy.
- Medium Speed: Balances comfort and energy efficiency.
- Low Speed: Consumes the least energy, with only a slight delay in achieving optimal comfort.
Conclusion: Paving the Way for Smarter EV Design
As electric vehicles become more prominent, tools like co-simulation are essential in crafting a user-friendly and competitive product. By blending 3D CFD with 1D system modeling, manufacturers can optimize a vehicle’s thermal performance and ensure it meets consumer expectations for both range and comfort. Together, these simulations allow engineers to fine-tune vehicle parameters, such as compressor speed, in response to different driving cycles. For instance, reducing the compressor speed in the HVAC system can lead to significant energy savings without greatly impacting comfort levels.
This holistic approach promises a range of benefits:
- Improved Range: Strategic HVAC adjustments can preserve battery life and extend driving range, reducing range anxiety.
- Enhanced Comfort: Precision simulations ensure that passengers enjoy a comfortable cabin experience, even in extreme climates.
- Energy Efficiency: Optimized HVAC systems lead to lower power consumption, helping to meet energy targets.
As simulation technology advances, EV designers are increasingly able to predict real-world outcomes in a virtual environment. By adopting these methods, the automotive industry is poised to make electric vehicles not only a viable alternative to traditional cars but a preferred choice for eco-conscious drivers worldwide. The workflow presented here also exemplifies Dassault Systèmes’ approach to MODSIM, integrated modeling and simulation and supports the company’s long-term strategy to bridge the gap between designers and simulation engineers, ultimately speeding up the product development process.
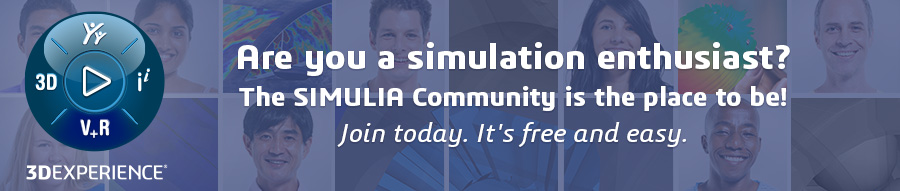
Interested in the latest in simulation? Looking for advice and best practices? Want to discuss simulation with fellow users and Dassault Systèmes experts? The SIMULIA Community is the place to find the latest resources for SIMULIA software and to collaborate with other users. The key that unlocks the door of innovative thinking and knowledge building, the SIMULIA Community provides you with the tools you need to expand your knowledge, whenever and wherever.