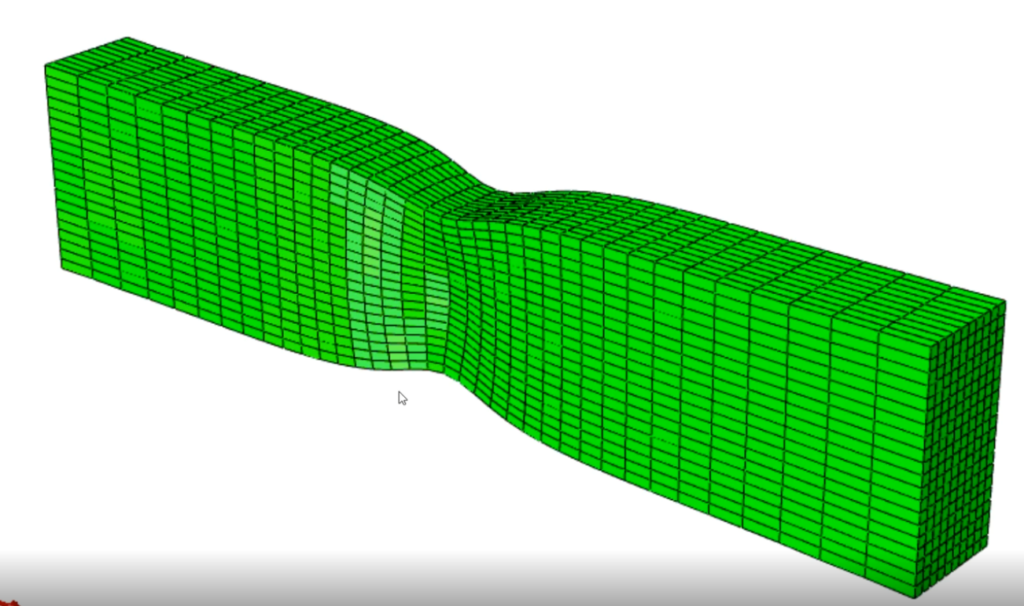
There is an older version of the Necking of a Titanium Dogbone example, and the older version does the normal thing and models the titanium with a classic Mises plasticity, linear elastic-plastic material model. That earlier example can be found here: Necking of a titanium dogbone specimen (elastic-plastic, 1500 elements, 6150 DOF, runtime ~13 secs, video from Nov, 2020).
I wanted to redo that example so that:
- We could show the general set up of the problem in a newer version of the Calibration App.
- We could show the use of a hyperelastic-plastic (FeFp) material model and a quirk of using the Marlow or Valanis-Landel hyperelasticity models in FE mode.
What does FeFp mean again? Classic (older) plasticity formulations used an additive decomposition of total strain into an elastic strain and plastic strain. In a paper by Simo for finite strain J2 plasticity, he proposed that the flow rule rule and kinematic hardening law should be derived assuming a multiplicative split of the deformation gradient as F = FeFp. That is, a multiplicative decomposition of the deformation gradient.
J.C. Simo, A framework for finite strain elastoplasticity based on maximum plastic dissipation and the multiplicative decomposition: part I. continuum formulation, Computer Methods in Applied Mechanics and Engineering 66 (1988), 199–219
What is unique about the Marlow and Valanis-Landel (VL) models ? Most hyperelasticity models in Abaqus use an equational form, defining those forms by material parameters. The Marlow and VL forms of hyperelasticity use test data to define the model. The Marlow uses one piece of test data and the VL model uses two pieces of test data. These test data must have a Deformation Mode attribute like Uniaxial, or Biaxial, etc.
Note : The “quirk” I mentioned above “a quirk of using the Marlow or Valanis-Landel hyperelasticity models in FE mode”. When one imports test data while in Analytical or Numerical mode, they are asked to define a Deformation Mode.
In FE mode, we think of the test data used for calibration (experimental data matching to the FE result) to be very general. Data like forces and displacements from a three-point bend test, or indentation tests, for example. Because of this, while importing test data in FE mode, one is not able to declare a Deformation Mode. The Deformation Mode is defined by the FE model(s) itself.
If one wants to use a Marlow or VL model in FE mode, one must first import the data that will define the Marlow or VL model while in Analytical or Numerical mode. We will demonstrate that in the video below.
The video below was created on on August 12, 2024 using the 3DExperience public cloud, R2024x, HotFix 4.20
All the files needed to recreate this example are included in the zip file at the bottom of this post.
This first video, named Marlow_FeFp_1c.mp4 shows a successful calibration set-up and Evaluation. The 3dxml file for this calibration object is contained in the attached zip file.
Note: It turns out that in R2024x HotFix 4.20 there is a bug associated with this workflow. It is related to how the software numbers each piece of test data.
The video below was created on on August 14, 2024 using the 3DExperience public cloud, R2024x, HotFix 4.20
I point out the action that leads to failure due to this bug at the 1:30 mark of the video.
To access the example files, visit the SIMULIA Community post where you can download the zip file.
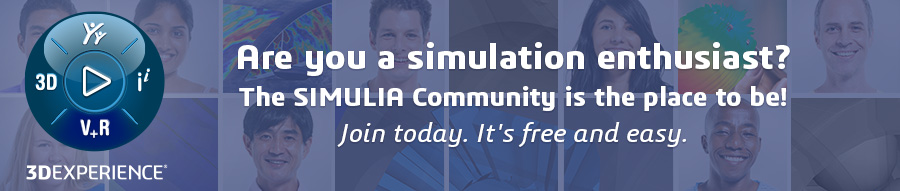
Interested in the latest in simulation? Looking for advice and best practices? Want to discuss simulation with fellow users and Dassault Systèmes experts? The SIMULIA Community is the place to find the latest resources for SIMULIA software and to collaborate with other users. The key that unlocks the door of innovative thinking and knowledge building, the SIMULIA Community provides you with the tools you need to expand your knowledge, whenever and wherever.