Introduction
Centrifugal pumps are widely used for pumping low-viscosity fluids such as water, oil and many industrial chemicals. A centrifugal pump consists of a central inlet and a rotating impeller that accelerates the fluid and forces it through the outlet along the outer rim of the pump. Centrifugal pumps also typically include diffusers: fixed vanes inside the pump that slow the fluid and increase pressure while also increasing the uniformity of the flow. The precise geometry of these diffusers affects the performance and efficiency of the pump.
Challenges in Centrifugal Pump Design
Centrifugal pumps are widely used in industrial applications such as oil pumping, water & sewage processing, and industrial chemical facilities. They are mechanically simple and capable of moving low-viscosity fluids efficiently. However, the flow must be kept uniform to keep loads constant. Non-uniform flows can force the pump out of its optimal operating range and increase noise and fatigue on the shaft.
For this reason, diffusers are often used inside the pump. These take the form of a stator with curved vanes arranged around the impeller in the opposite direction. The diffuser must be able to regularize and slow the fluid flow while minimizing turbulent flow effects such as flow separation caused by the interaction of the flow with the diffuser vanes. The performance of the pump depends significantly on the design of the diffuser, impeller & volute, and the interaction between the impeller and diffusor.
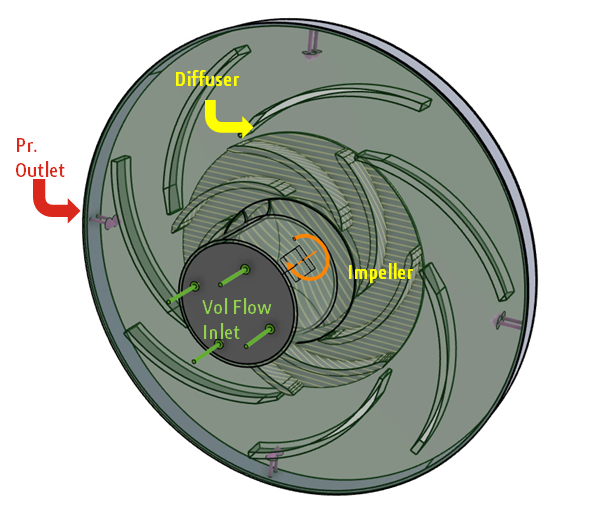
The European Research Community on Flow, Turbulence and Combustion (ERCOFTAC) has developed an open-source pump model for the modeling & simulation community to create best-practices and make methodology improvements. As this has been validated by both experiment and simulation, this is a good test case to demonstrate the benefits of machine learning on.
Centrifugal Pump Diffuser Optimization
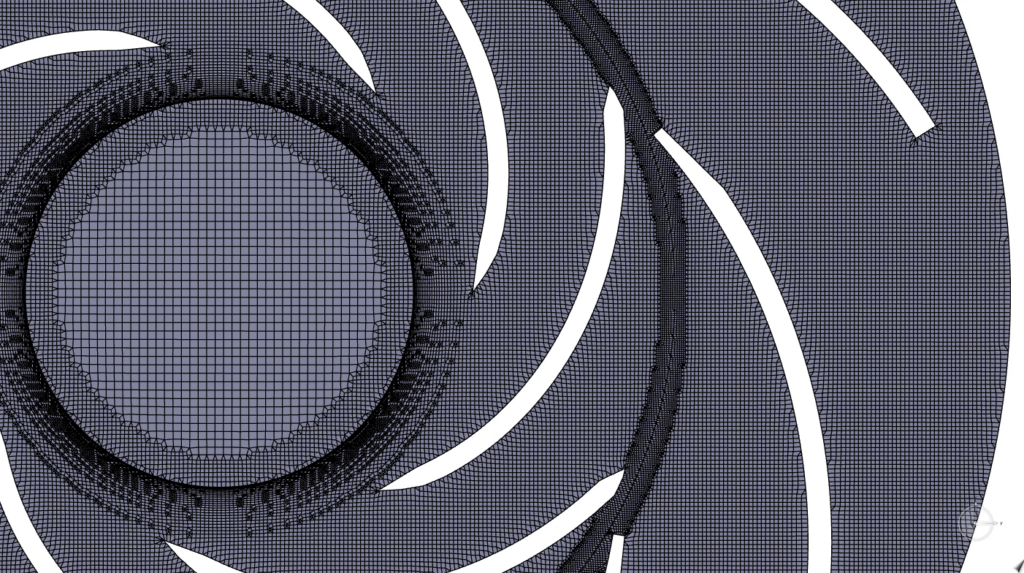
This optimization study focused on the diffuser geometry. There are four parameters to vary here: vane thickness, chord length, inlet angle and outlet angle. The complex interdependencies between these mean that all need to be considered at the same time in the optimization. The simulation was performed using CFD tools on the 3DEXPERIENCE platform.
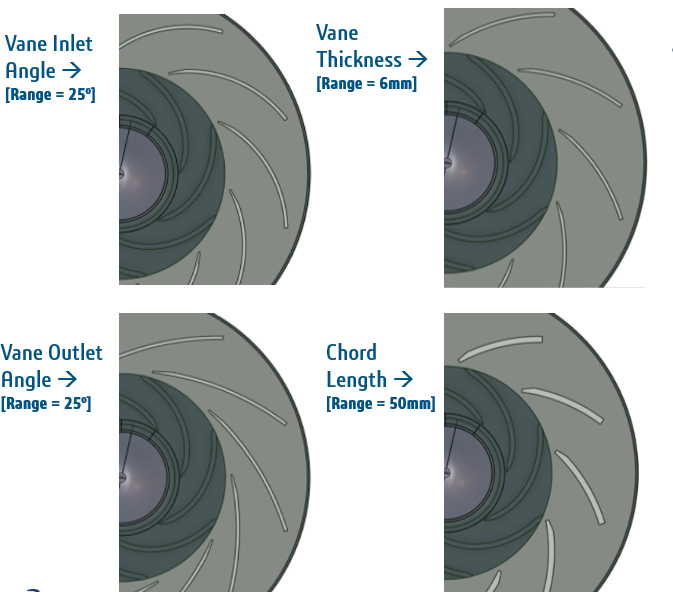
Top left: Leading edge angle can define the sharpness in the change of flow direction
Bottom left: Trailing edge angle can define the extent of change in flow direction
Top right: Thickness of a vane can define the pinching or expansion of the flow
Bottom right: Chord or the curved length of the vane can play an important role in flow separation
Simulating every possible combination of these parameters with full computational fluid dynamics (CFD) would be prohibitively time consuming. One-dimensional simulations are sometimes used instead to reduce the computational requirements, but these give poor results. Instead, we turned to machine learning (ML). A surrogate AI model can be trained on a sample of full CFD simulation results to replicate the behavior of flows within the pump with different parameters. The resulting model was then validated against further simulations and physical tests and showed excellent agreement with both the full simulation data and the measured data.
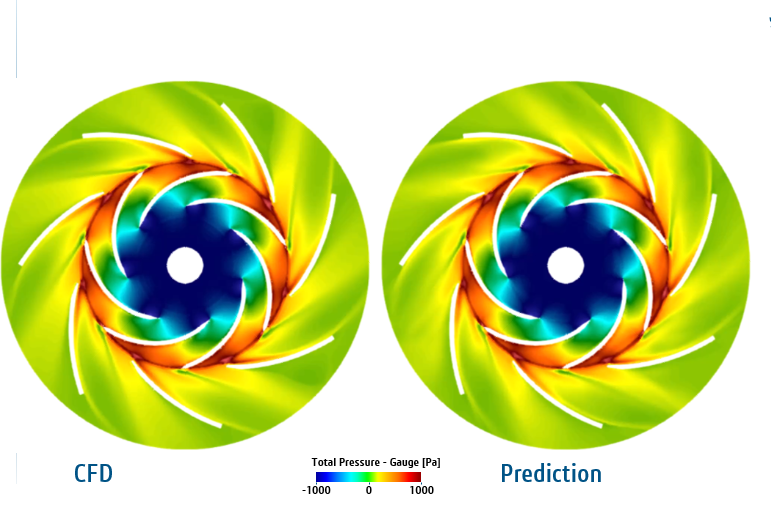
The trained AI model was able to provide results, within 2% of the CFD data, for any combination of parameters within the specified range in a matter of minutes. This gives engineers rapid feedback about the impact of a design change, allowing them to consider large numbers of scenarios to accelerate design decisions. With design exploration powered by this machine learning model, engineers could quickly find a trade-off that best meets their design requirements.
Conclusion
Improving the performance of centrifugal pumps can increase efficiency while reducing noise and extending fatigue life. CFD simulation reveals the effect of design variations on the performance of the pump, and machine learning can be used to train a generative AI experience model from these results. This model can quickly predict performance for different parameter combinations and guide engineers to quickly find the optimal pump design for their requirements. With the combination of CFD simulation and machine learning, engineers can develop products faster and get fast, reliable feedback about the effect of design changes on performance.
For more information about this application, see the paper “Improving Performance of a Centrifugal Pump Through a CFD DOE Study of Radial Diffuser Design”.
To discuss the application of machine learning and AI to simulation, join us on the Machine Learning wiki in the SIMULIA Community.
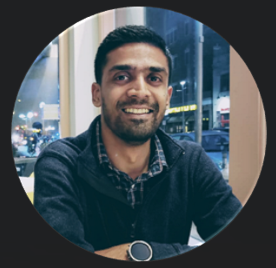
Ani Rajagopal has been serving as an Industry Process Consultant at SIMULIA since 2019, joining the Worldwide Fluids team following the integration of Exa Corporation. With nearly 8 years of expertise in fluids and thermal sciences, he serves as an expert voice in supporting customers across all industries including Industrial Equipment and Transportation & Mobility. In his role within the Worldwide SIMULIA Fluids team, he focuses on enhancing fluid solutions through physics-testing, and deploying these solutions to optimize customer processes, particularly through automation. Recently, he has been a key member of the core validation group for SIMULIA’s AI/ML initiatives, specifically for fluids-related applications.
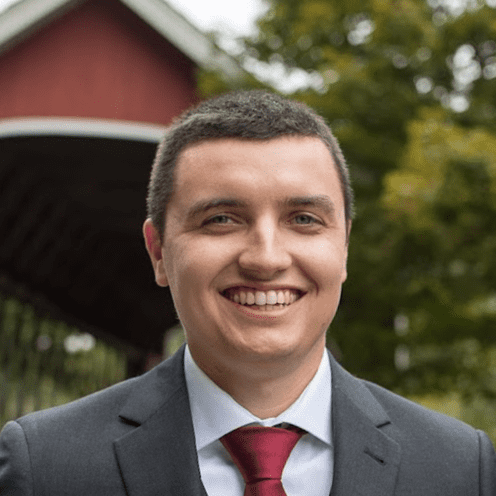
John Higgins is an Industry Process Consultant at SIMULIA. He joined Dassault Systèmes in 2019, following the integration of Exa Corporation. John has over 10 years of experience in fluids and thermal sciences, during which he has worked in pre-sales, post-sales support, and services capacities. He has experience supporting customers across all industries, including Transportation & Mobility, Industrial Equipment, and Aerospace & Defense. In his current role, he focuses on enhancing fluid solutions through development of first-of-a-kind processes, physics validation testing, and deploying fluid solutions to optimize customer processes. Recently, he has been a key member of the core validation group for SIMULIA’s AI/ML initiatives, specifically for fluids-related applications.
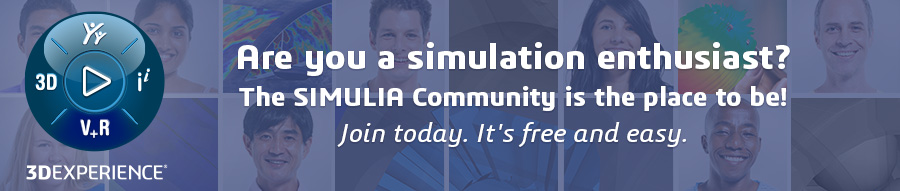
Interested in the latest in simulation? Looking for advice and best practices? Want to discuss simulation with fellow users and Dassault Systèmes experts? The SIMULIA Community is the place to find the latest resources for SIMULIA software and to collaborate with other users. The key that unlocks the door of innovative thinking and knowledge building, the SIMULIA Community provides you with the tools you need to expand your knowledge, whenever and wherever.