Designing energy-efficient, robust, and durable Turbine Blades is a multidisciplinary challenge in Aerospace & Defense (A&D) and Industrial Equipment (IE) industries. By equipping our customers with state-of-the-art simulation technologies, we can significantly reduce the design cycle and simulation cost, giving them the edge over their competitors.
We asked Yunfei Shi, Technical Solutions Consultant with SIMULIA who developed this workflow, to provide answers to some common questions.
Q: Why does this workflow need to be analyzed?
A: Designing energy-efficient, robust, and durable In Jet Engines and Gas Turbines, to extract as much energy as possible from high-speed flows, turbine blades must work in extreme conditions of high temperature, high pressure, and high centrifugal load. To provide enough cooling to the blades without compromising its energy efficiency and structural integrity, design engineers and analysts are spending months if not years perfecting the designs of blade shapes and Cooling Channels.
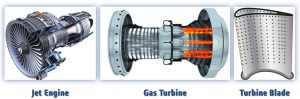
Q: Describe the workflow.
A: To help product engineers in the A&D and IE industries ease their pains in carrying out routine simulation tasks, we have developed an Industry Workflow for Structural Analysis of Turbine Blades. This workflow includes Heat Transfer, Thermal Stress, and Creep analyses using Realistic Geometry of the blade design. Instead of navigating through menus and buttons on various software platforms, product engineers can follow step-by-step tailored instructions to complete the tasks of Modeling, Meshing, Computing, and Results Analytics using Vertical Applications.
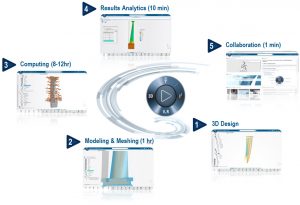
Q: What are the key simulation goals? What are you trying to learn from the simulation?
A: Detailed spatiotemporal distributions of temperature and thermal stresses are critical to evaluating and improving the Energy Efficiency and Fatigue Life of blade designs. These structural simulations help product engineers understand how different cooling techniques will affect the Thermal Performance and Structural Integrity of the blade design and come up with Alternative Designs for improvement.
Q: Which SIMULIA solutions did you use?
A: For this workflow, I used the Structural Analysis Engineer role on the 3DEXPERIENCE platform, which offers the state-of-the-art technologies of High-Performance Modeling and Meshing, High-Performance Computing, and High-Performance Visualization. This workflow also includes the Enhanced Iterative Solver Technology that SIMULIA has recently developed for Large-Scale Simulations.
Q: What were the benefits of using simulation workflow?
A: The most significant benefit of adopting this simulation workflow is to save product engineers from the trouble of simplifying cooling channels and reducing mesh quality, which usually takes about 14 days. The SIMULIA solutions on the 3DEXPERIENCE platform allow product engineers to perform unprecedented large-scale simulations and obtain results of high fidelity and high accuracy in less than 2 days. In addition, designers and product engineers can work seamlessly on the same Digital platform with Automatic Data Synchronization and Traceability, reducing design cycle and monetary cost.