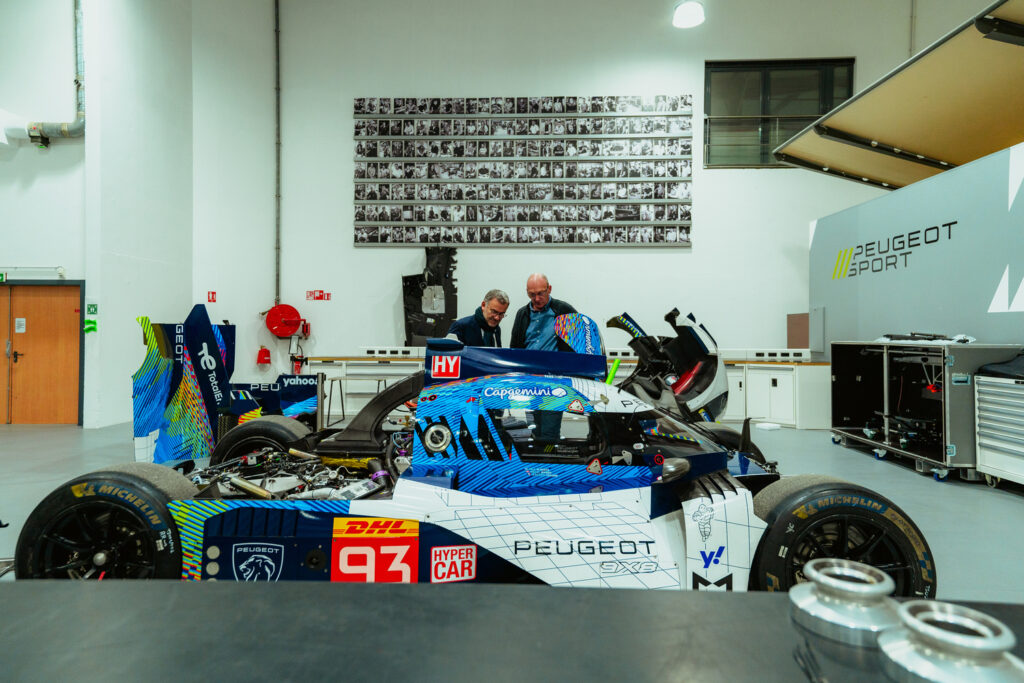
Tell us the difference between a hypercar and a standard F1 racing car.
The hypercar is designed for endurance racing, unlike a Formula 1 car. It’s meant for long-distance races, typically between six and 24 hours. So it could be up to 24 hours, like the 24-hour race in Le Mans, which is legendary for endurance racing. The hypercar is a new class regulation. It’s a class of cars, more precisely, that has been involved with endurance racing since 2021. It is a new regulation of the top class in endurance racing from 2021 to 2027. So, the hypercar also looks quite different from a Formula 1 car. All of them have closed cockpits now and are much bigger cars. They are about five meters long and two meters wide. So, it’s a much bigger car running for a longer distance and heavier than an F1 car.
How did the new hypercar regulations influence the design of the hypercar? And what changes were made to the design of the 2024 race car?
So, first, PEUGEOT 9×8 is built on the the LMH regulation, which is very open regarding what it allows for. The car’s design and shape are not as constrained as in other categories and other formulas, which gives a lot of freedom to the car’s design.
In our Peugeot perspective, we use that advantage to try to embed many of the aesthetic codes from the Peugeot brand, so that everyone can look at our race car and think about the Peugeot road cars, which was very important for us.
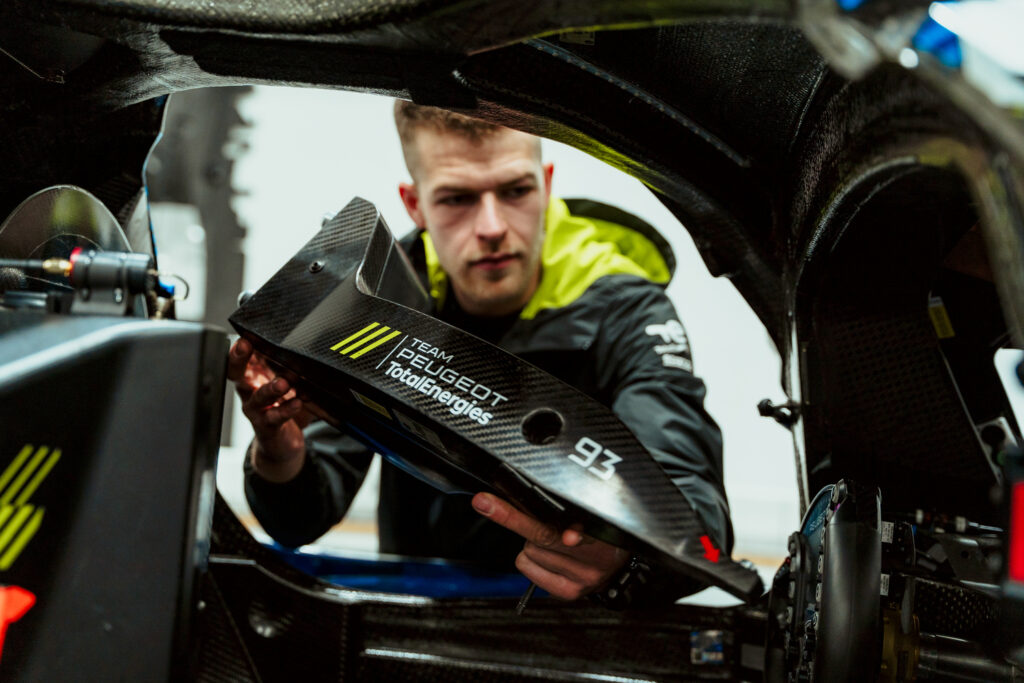
And that’s thanks to the regulation that is very open on the car design, for the car look. As for the 2024 car, the most significant visual change is that we added the rear wing to the car. So, we changed the aerodynamic concept of the car to try to match the new tire dimensions on the car. So, from a non-expert eye, I would say the most significant difference in the 2024 car is that we now have a rear wing with a different aerodynamic package.
Is that what has made the most aerodynamic impact on the car?
Yes. Correct.
How did virtual design and testing differ from wind tunnel and physical testing?
Well, virtual design has, overall, a much quicker turnover, and it’s also cheaper. In wind tunnel and physical testing, you need to develop the shapes. You need to design the parts properly for mockup parts or full-scale parts.
You need to have a design phase and then a production phase, which usually involves some tooling, which generally takes up to six to ten weeks, depending on the part itself. Then you go to testing, which is another week. Overall, the turnover is more than two months, two to three months from the idea to the physical test, whereas, with the virtual design and CFD testing, you can turn around ideas from your concepts and ideas to results within a week, so much quicker and also much cheaper.
How does moving simulation to earlier in the design process affect the overall outcome, and what are the benefits?
Simulation at the very early stage of the design process is critical because it helps with sorting out concepts. You can be very open at the beginning on concepts that look very different.
You would not be able to physically test all of those concepts because they are too different. They involve too many other models, whereas, with the simulation process, you can be much more open on the options you have at the beginning of the project, which helps you with making sure you’ve actually looked at every single opportunity of design and not just some minor improvements of existing known designs.
How does moving simulation earlier help design engineers gain access to aerodynamics expertise they otherwise wouldn’t have?
Well, as explained, they can look at very different things. So technically, from a design perspective, shapes are very different. That’s one thing. So it’s a much broader view of the potential, and then second, with the simulation, they can access the insights of the generated results.
So it’s not only the overall results they will tell, or that a shape is working overall; it creates that effect, or that one is better than the other. But here, they have access to a much more detailed understanding of what it does and why it does it.
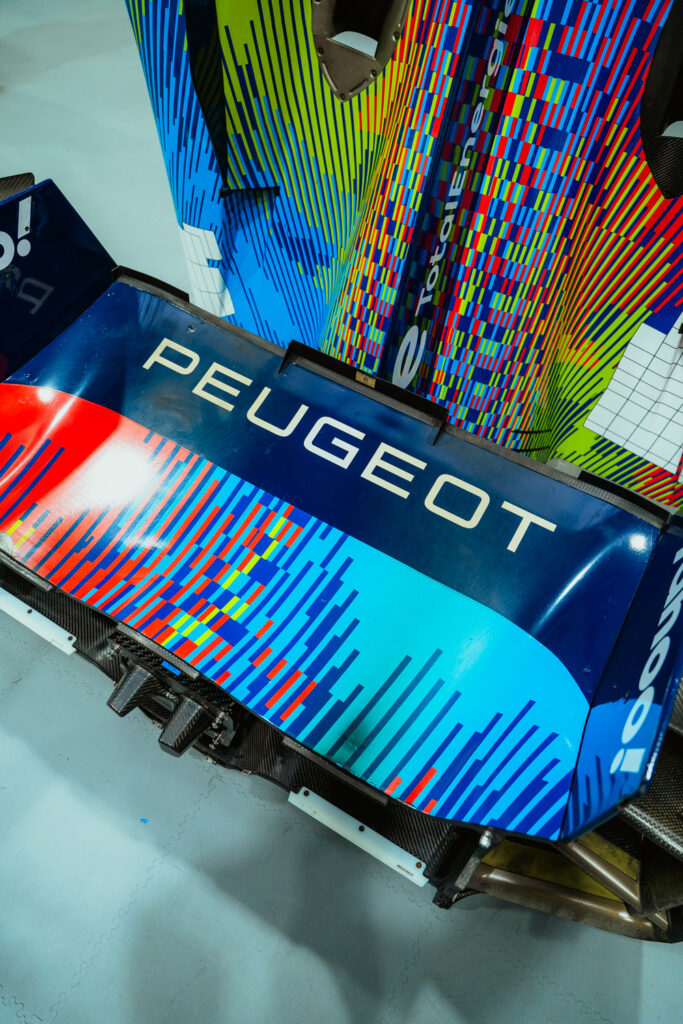
They can look physically at the flow structure around the parts, which would help them understand the physical phenomenon behind the results and, therefore, will be very important and helpful to give them the following ideas to move on to the next concept.
So, it helps understand the details of the physical problems and physical solutions and helps generate ideas for the next concept.
What was the most valuable aspect of using the 3DEXPERIENCE platform and helping to design and test the vehicle?
First, I would say there were two fundamental aspects for us. One was the fact that we are treating design in one single design environment, that is, having obviously CAD design, surface generation, surface meshing, and then simulation all within one environment, which is very helpful in terms of making sure you have a transfer process from one step to another that is as smooth as possible.
So, we are saving time and money by making the environment much more flexible for the designers. It’s also a straightforward way to share results and models between people working from different places.
Our project started during the COVID pandemic when everyone was isolated at home. It helped to have some sort of common platform where everyone could look at the results, comment on them, and generate the following ideas for others to work on.
What would the vehicle’s performance be without using simulation for the design and testing?
Well, it would be much lower. It’s clear that we would probably have missed some of the concepts that we, in the end, opted for simply because it would have been too far away from an existing consent. We would have never taken the risk of building parts and doing physical testing.
So overall, I think we’re getting more performance from the simulation. Without the simulation, the vehicles would have had less performance. Also, very clearly, the project schedule would have been impacted, and we probably would have been delayed in delivering something because, without the simulation, there’s no way we could have kept this very tight schedule we had for the development process.
How do you see simulation and virtual testing, 3DEXPERIENCE twin testing, helping with the future development of the hypercar and other racing vehicles? And what other possibilities are there for racing, in general, in the future?
Well, generally, I think the same answer applies to development. Hypercar and racing in general, I think overall, the computational power is increasing every single day due to the hardware and improvements.
Generally, we, on our side, are improving the model and the refinement of our models, whereas, on the other end, the physical testing is not improving. The investment for physical testing nowadays is enormous.
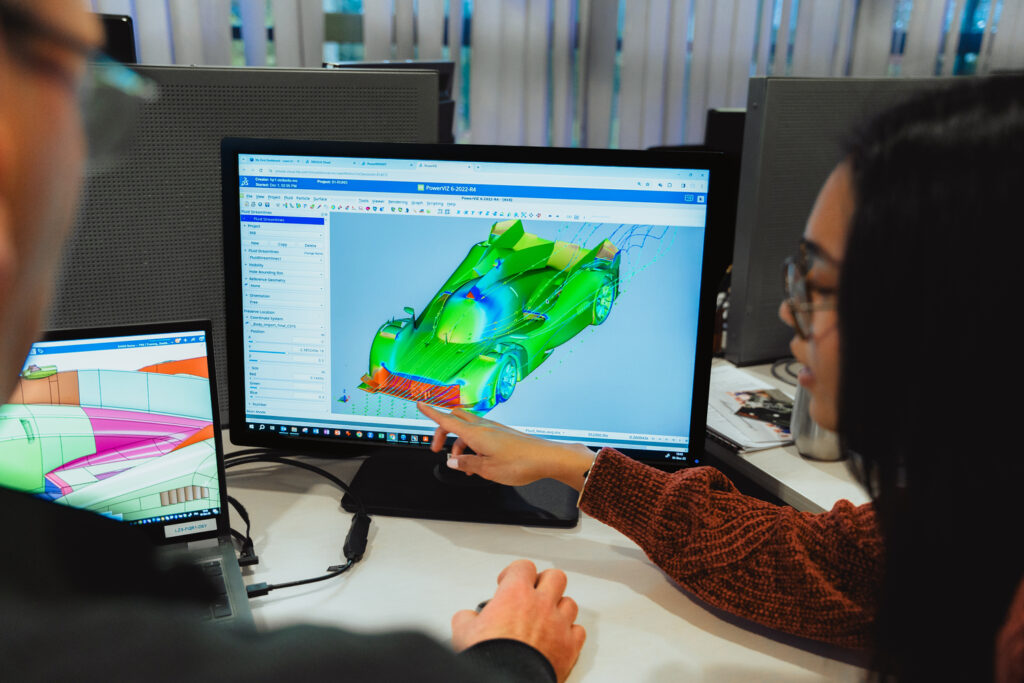
If you need a new wind tunnel, it will cost hundreds of millions of euros before you have something representative of the track. With simulation you do not have to cope with the constraints of the physical world; you’re in some sort of virtual world, where investments are on a much lower scale.
It’s essential that from time to time, you do some measurements in the physical world, in physical testing, to try to make sure the correlation is good. But once the correlation is good, the development possibilities are much higher. The refinement of what we can do with simulation is growing day by day at a much faster pace than the physical testing.
So overall, I think it’s a clear tendency that more and more of the aerodynamic development will be carried through simulation. We have seen this for more than ten years.
It’s an evident trend, and I think it won’t stop. The simulation is faster, more efficient, and cheaper as well.
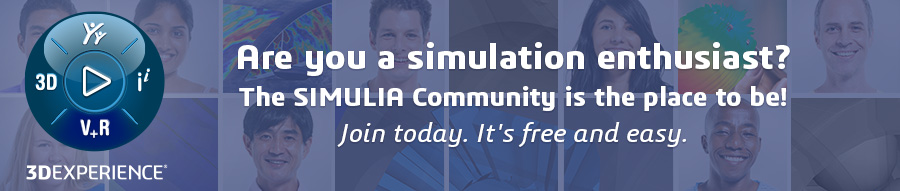
Interested in the latest in simulation? Looking for advice and best practices? Want to discuss simulation with fellow users and Dassault Systèmes experts? The SIMULIA Community is the place to find the latest resources for SIMULIA software and to collaborate with other users. The key that unlocks the door of innovative thinking and knowledge building, the SIMULIA Community provides you with the tools you need to expand your knowledge, whenever and wherever.