Design for Effective Soiling and Water Management for Reliable Performance of Sensors in Vehicles.
A study from INVENSITY, a technology and innovation consultancy, says that in the current environment 90% of the innovation in the automotive industry is driven by electronics and software, as the trend is moving towards higher levels of ADAS (Advanced Driver Assistance Systems) integration and autonomy. As ADAS systems are added to conventional vehicles to support the driver, they are designed to provide assistance in most normal scenarios. However, these devices are designed only to assist the driver, who maintains the primary responsibility to operate the vehicle. On the other hand, for emerging autonomous vehicles (AV), these devices become the primary means of navigation and safety. The ADAS system then requires accurate real-time awareness and must demonstrate perfect performance under all conditions, both normal and extreme.
In the past few decades, demand for fuel-efficient vehicles has also gained more popularity. As a result, cars are designed more aerodynamically to reduce drag. This is achieved, mainly, by managing the wake of the vehicle so that more air from the underbody impinges on the back of the vehicle. Unfortunately, the air from the underbody of the vehicle is often laced with dirt and water particles that impact the rear and side of the vehicle along with the air. In earlier days when ADAS systems were not that prevalent, soiling was a safety issue in terms of driver vision, but this was limited primarily to glass and mirror surfaces. Surface soiling on the rest of the vehicle was mainly about aesthetics. Now with the increasing number of ADAS systems, especially on AV vehicles, the surface soiling on the rest of the vehicle also becomes a passenger and traffic safety issue because it can interfere with the performance of cameras and sensors. Most of the automotive industries working on ADAS and AV are trying to find soiling problems in the early design stage. These studies and experiments are currently performed in climatic wind tunnels with controlled conditions for surface soiling and water management. However, these wind tunnels are artificial environments and they don’t represent the real road and climatic conditions, as well as being very costly and time consuming to operate.
This leads to a few questions: are there any cost effective solutions to prevent soiling over the camera and sensors? Where should the sensors be placed for optimal performance? How do we make sure they all work correctly? Given that one cannot avoid a situation when a splash of mud or other dirt hits the camera, can we control where and how vehicles interact with it?
Why sensors are needed, and how can they get soiled?
In the present era, an increasing number of sensors is a significant trend, as advanced technologies, autonomous driving, more electrification, and driver assistance systems are being implemented in modern vehicles. Autonomous vehicles are faced with a wide variety of operating situations, such as when the vehicle needs to be reversed, emerge from junctions, detect collision threats, etc. The cameras and sensors fitted on these vehicles thus become their eyes and ears, without which autonomous driving would be impossible. Both cameras and sensors must remain uncontaminated by any soiling to operate flawlessly – however, the environment in which they function rarely offers this luxury.
Now, contamination of such sensors and cameras can be due to direct soiling, third-party soiling, or self-soiling, depending on its source. Rain provides direct contamination. Third-party soiling on cars occurs due to spraying of mud/rock/soil/water ricocheted by both upstream and passing traffic. The spray of dirt caused by the vehicle’s own tires leads to self-soiling. Front-tire spray creates a “deposit zone” along the body side that extends from the front wheel to the rear wheel. Rear tires generate a spray that is the dominant source for contamination on rear surfaces.
Surround-view cameras (front, rear and blind spot detection cameras) are usually directly exposed to adverse environmental conditions. This is particularly worsened when the camera lenses are exposed to rain. This leads to both reduction in the vision of drivers and the performance of cameras, and results in a critical safety issue.
How to address this issue?
Dirt, water, and other contaminants are the reality of driving on roads. While we cannot prevent this, we can design vehicles to better interact with it. Some solutions exist for keeping sensors and cameras clean, such as automatic cleaning of lens by using a jet of water followed by a puff of air, or coatings over the lens. However, coatings don’t last long and are quite expensive, and the addition of cleaning solutions can increase weight leading reduced fuel efficiency as well as increased running costs. As an alternative to this, we can try to predict where rain, dirt, bugs, rocks, or other matter are going to hit the vehicle, and subsequently can optimize the sensor positions or recommend design changes to the vehicle to minimize the soiling over cameras. Then we can predict how any design change or the alteration of a camera position can affect the aerodynamic performance of the vehicle and hence the fuel economy.
The ultimate idea is to create vehicles where sensors are placed optimally for minimal dirt deposition and the least exposure to water. However, if any external cleaning devices are still needed, the position of such systems can be optimized.
“There will always be a balance between investing in an expensive coating on a surface, or just moving a sensor by a couple of inches. We can still help.” [Article: The shape of water: how soil and fluid simulation can save OEMs millions]
Soiling & Water Management using SIMULIA Solutions
SIMULIA provides solutions to investigate a wide range of soiling and water management phenomena. Using PowerFLOW, one can perform detailed aerodynamics and particle flow simulations to assess vehicle design goals. The simulations are performed using PowerFLOW and by displaying the results in PowerVIZ, one can dynamically visualize the release of particles into the airflow and compute the particle trajectories until impingement on the surface. It allows the user to include dust, dirt, rock, and water in the simulation, which gives a clear understanding of how vehicles interact with the contaminant particles, hence giving OEMs the opportunity to better manage soiling over the vehicle surface. In addition, surface properties can be defined so particles can reflect off surfaces and create complex flow paths through the engine bay or on the vehicle surface.
For our study, we considered three scenarios, each with a different location of the camera in the car.
Scenario 1: Accumulation of dirt and mud over the rearview camera
In the first scenario, we simulate the accumulation of dirt and mud over the rearview camera, which is mainly due to the spray caused by the vehicle’s own tires, dominantly by the rear tires.
Scenario 2: Deposition of water over the BLIS (Blind Spot Information System) side mirror camera
In the second scenario, we simulate the deposition of water over the BLIS (Blind Spot Information System) side mirror camera in rainy conditions. One can simulate how the rainwater particles behave and interact with the camera lens for a specific door mirror design.
Scenario 3: Rock chips striking the front camera
In the third scenario, we have worked on understanding how the rock chips flying from passing traffic strikes at the front camera of a vehicle and affects its visibility and function.
Results
I. Rear & side body soiling
A rear view camera, also known as a reversing camera, helps the vehicle or driver to see the area behind the car and improves the rear blind spot vision. The added visibility helps prevent a crash when backing up. For the baseline design of the car, the dirt particles emitted from the rear tires are deposited over the rear surface and obscure the view of the rear camera, ensuring an unsafe travel experience for the passengers. For this study, a design change in the underbody of the vehicle is proposed, with the goal to redistribute the contaminants away from the most sensitive locations, such as camera positions and license plate. As shown in the figure below, the underbody diffuser is modified by bending its curvature upward.
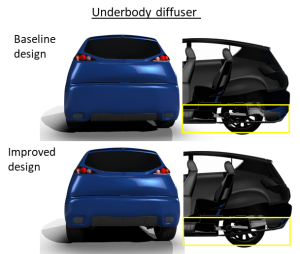
For the baseline design, the streamlines associated with the rear wheel wake interact with the lower part of the base wake vortex. This interaction signifies an advection mechanism, which can potentially transport contaminants into the rear wake. Whereas, the change to the diffuser strengthens the lower lateral arm of the rear wake ring vortex, resulting in a more balanced rear wake.
The plots of rear surface film thickness accumulation shown below provide a qualitative comparison of the baseline design and the modified design. It can be seen that the design changes made to the underbody diffuser modified the distribution of the rear face contamination as well as the level on the rear windshield. This is of interest because some regions of the back face are more important to keep clean than others. For example, the camera, license plate, and rear gate handle are important regions to keep clean, and this can be achieved with this slight design modification at the early design stage.
This work provides evidence that aerodynamic interventions in the vehicle design may be able to redistribute the surface contaminants away from the most sensitive regions. However, as we have not been able to demonstrate enough reduction in rear surface contamination in this first step of our study, we have pursued further systematic design investigations to find the modifications required to achieve the desired results.
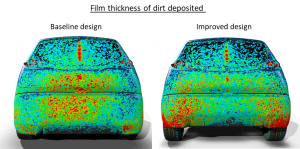
In many regions mud flaps are added as an aftermarket product, because it is thought that they reduce the soiling on the vehicle. Our investigation reveals that this is not the case, and in fact, they actually increase the general height of the soiling on the sides of the vehicle. As shown in the figure below, they allow the dirt to reach the door handles, which would make the customer’s hands or clothing dirty when they come into contact with the handle.
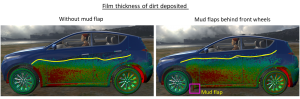
II. Soiling due to rain
A blind spot information system (BLIS) camera, which is usually mounted below the side door mirrors of the car, keeps an eye out for other vehicles and helps an autonomous vehicle to see what is around them, even at the blind spots. When rainwater droplets impact on the door mirror housing, they break up and form a fine spray layer which then gets influenced by the mirror wake direction. This results in deposition of droplets over the side mirror and camera lens, thus obscuring the side mirror and camera views. With the baseline design, a lot of water is being deposited over the mirror and camera lens, which impacts the view (see second figure below). From the time history visualization of the particles hitting the side glass, one can see that most of the particles hitting the side glass are coming from the bottom of the mirror arm. Consequently, the mirror arm is modified as shown below to change the vortex behind it and reduce the soiling over the mirror and camera lens.
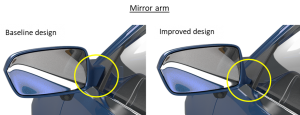
Examining the plots shown below of water film thickness accumulation over the mirror and camera, it is clear that the design change in the mirror arm drastically reduces the amount of soiling by water that is deposited over the mirror and camera lens.
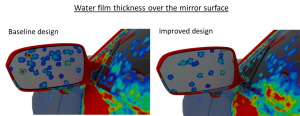
III. Rock thrown by a moving vehicle
The car front cameras are designed to avoid hitting parking blocks, curbs, and other potentially disastrous obstructions, and the most common cause of camera damage is the debris thrown from other vehicles, such as rocks, stones, gravel, and pebbles. These tiny, hard granules fly at high speed and can damage the sensitive parts of other nearby vehicles moving in traffic. It is also a significant source of corrosion of an automotive underbody along with undesired cosmetic effects.
For our study, a simulation has been done with the goal to optimize the location of the front camera. We try to minimize the risk of its damage by the rocks thrown from the tires of a vehicle moving ahead of the car. As shown in the figure below, for the baseline design the front camera is placed at the top of the lower grille, and the simulation, shows that the camera is exposed to the thrown rocks and is more prone to get damaged. The hit points plot obtained from the simulation results gives a clear picture of the locations that are less likely to get hit by the rocks thrown from the tires of a forward moving vehicle. Consequently, by comparing the hit points from the analysis results, the camera location is moved to the bottom of the upper grille, where it is clear that the new position of the camera is safer and it is less likely to get damaged. Similar studies are very useful to optimize the camera positions in the early design stage and to avoid the potentially costly consequences of changes late in the design process.
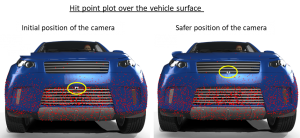
Conclusions
Simulation techniques are very promising in evaluating the performance of sensors on vehicles in adverse climate and road conditions. Car manufacturers put significant effort into finding ways to reduce the dirt deposition on the vehicle body, and also to make sure that the rain droplets do not obstruct the camera vision. Our study has presented the simulation methodologies to study soiling of vehicle rear and side surfaces due to dirt, rain, and the interaction with the debris thrown from the tires of moving vehicles. The study is done by addressing 3 cameras at different locations of the car. In addition, design changes are also suggested to reduce the soiling over the cameras and to keep them clean. The procedure implemented in this work gives the added benefit of performing virtual testing in the early stages of the vehicle development, thus eliminating the need for physical prototypes and testing, especially in Advanced Driver Assistance Systems (ADAS) and Autonomous Vehicles (AV), where a large number of sensors is required. While the influence of these design changes on the aerodynamic performance of the vehicle is beyond the scope of this study, tradeoffs may need to be made between the reduced soiling over the external surfaces and the increased drag.
See all our Transportation & Mobility solutions by visiting:
https://www.3ds.com/products-services/simulia/solutions/transportation-mobility/
SIMULIA offers an advanced simulation product portfolio, including Abaqus, Isight, fe-safe, Tosca, Simpoe-Mold, SIMPACK, CST Studio Suite, XFlow, PowerFLOW and more. The SIMULIA Community is the place to find the latest resources for SIMULIA software and to collaborate with other users. The key that unlocks the door of innovative thinking and knowledge building, the SIMULIA Community provides you with the tools you need to expand your knowledge, whenever and wherever.