This blog was originally published as a whitepaper, which you can download here.
Advanced driver assistance systems (ADAS) offer an extra layer of safety and convenience while driving. Besides that, they are also an important step towards fully autonomous vehicles. Radar, vehicle-to-vehicle communication, 5G connectivity, smart road infrastructure and satellite navigation all help ADAS systems be aware of their surroundings, and all these systems heavily rely on antennas and sensors to function.
Placing antennas on vehicles poses several challenges. The body of a car can strongly influence the antenna performance, reducing efficiency and changing the field pattern. Different systems can interfere with each other and other sensitive on-board electronics. Water and dirt can also soil antennas and sensors, reducing their effectiveness. Simulation supports antenna and sensor system design and integration by allowing engineers to analyze their performance in real-world scenarios before committing to building a physical prototype.
EXECUTIVE SUMMARY
In order to safely control a vehicle, ADAS systems require full awareness of their surroundings—lane markings, signs, road conditions, other vehicles and road users, as well as unexpected obstacles. Vehicles equipped accordingly detect their environment through a number of techniques such as cameras, ranging systems like radar and lidar, geolocation, and other sensors located around the vehicle. Robust 5G and other high speed mobile data connectivity is also critical to ensuring ADAS systems can interface with internet services, smart road infrastructure, other vehicles as well as the passengers’ own devices. The components that comprise these systems are sensitive to placement effects, dirt and snow soiling and interference from other antennas and electronics. These factors need to be addressed at the whole system level in order to design safe, reliable ADAS and autonomous drive systems.
CHALLENGES OF ADAS AND AUTONOMOUS DRIVING
Antennas and sensors are necessarily very sensitive to their surroundings. In order to allow them to operate safely and reliably, unwanted influences need to be minimized. This is particularly difficult when designing a vehicle with limited space for mounting components, which also has to drive in unpredictable and highly variable conditions. The metal body of the vehicle can block and reflect electromagnetic waves. The performance of an antenna on a curved car body can also be very different to the idealized datasheet characteristics, which generally assume a flat ground plane. This can lead to blind spots in coverage for safety critical systems such as radar or cause spurious readings by affecting beam direction and side lobes. Therefore, component placement is critical to building an effective ADAS system.
Electromagnetic interference (EMI) from other components can also cause issues. Radio and radar antennas, power electronics and high-voltage systems (such as electric drive systems) for example, can all radiate fields or generate currents that affect sensor performance. Electromagnetic compatibility (EMC) is likewise an issue—the sensors must not interfere with other systems in the vicinity and surrounding vehicles. Similarly, the fields radiated by antennas and sensors must remain within radiation hazard (RADHAZ) exposure limits. Occupants as well as passersby need to be safe when radar sensors are operating. The specific absorption rate (SAR) for human tissue needs to be analyzed for different use cases and under varying load cases to ensure compliance with regulation. Finally, factors outside the vehicle can affect antenna performance. Other vehicles, the road environment, and the weather can all reflect or absorb electromagnetic waves. Labs and test tracks offer an opportunity to measure how ADAS systems perform in different environments, but testing all the different scenarios that can occur would be prohibitively expensive and time consuming.
BENEFITS OF SIMULATION
Introducing simulation in the ADAS design cycle can significantly reduce development times, costs and above all, risks, by addressing the challenges listed above. Electromagnetic simulation calculates the electric and magnetic fields and antenna farfield pattern, as well as other relevant key performance indicators (KPIs) such as directivity and gain. These can be determined through simulation long before building a physical prototype. A wider variety of configurations—such as different antenna types and placements—can be analyzed in parallel in order to optimize performance. For these analyses, CAD models are directly transferred into the simulation environment, allowing engineers to rapidly see how design changes affect ADAS performance.
Multiple antennas and sensors can be simulated together in situ on the same vehicle platform. This means that parasitic effects and interference are taken into account during the simulation. Other components that might cause interference, such as on-board electronics and electric drive systems, can also be included. Furthermore, fluid simulation can be used to calculate the effect of rain and mud spray on sensors. The spray patterns, calculated at different speeds and in different conditions, help to identify potential issues before commencing wide scale test drives. Using the same model data for the electromagnetic and fluid simulation speeds up the process even further.
Vehicles can quickly travel tens or hundreds of virtual miles in simulation, covering a much wider variety of road scenarios than test driving alone could ever hope to match.
Collaboration and a combination of workflows to ensure vehicle safety and reliable connectivity
The increased complexity of ADAS and Autonomous Vehicles requires close collaboration between designers and engineering teams to solve the challenges and benefit from faster development cycles and reduced risk. Combining simulation workflows, and integrating simulation with other products, including CAD and PLM, can help to meet the common requirements and engineering challenges of ADAS designers. Components developed by different groups can be quickly assembled into a full vehicle model and prepared for simulation, thus ensuring that simulation engineers are working with the latest versions of the geometry and keeping up with changes made to the underlying models.
Antenna design—quickly providing the right antenna for the given application
One of the first steps of developing any ADAS system is to find the correct component for the application. Antenna Magus offers a searchable catalogue of antenna designs, and will automatically select and suggest antennas that meet specifications such as size, technology, frequency and gain. These can then be used as a good starting point and give confidence for the final antenna optimization.
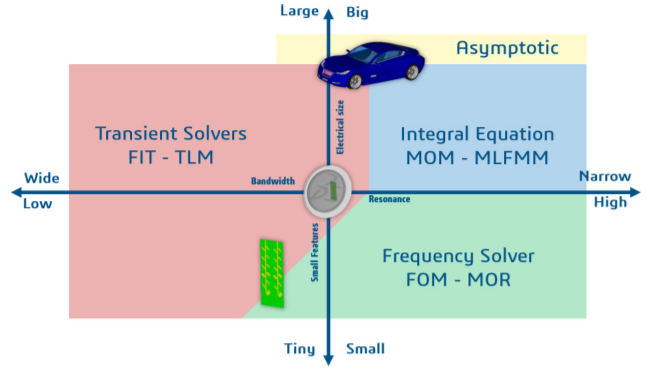
Antenna and sensor placement—calculate the KPIs for 5G, mobile data, radar, GPS and other antenna systems to find the optimal placement
Once an appropriate antenna has been designed, it then has to be placed on the vehicle and integrated into the system at large. The electromagnetic simulation package CST Studio Suite allows engineers to calculate the KPIs of antennas and sensors when attached to the vehicle. Full wave 3D electromagnetic simulation can include the vehicle body, other electronics, and the surrounding environment, to ensure the component will behave as expected when mounted on the vehicle.
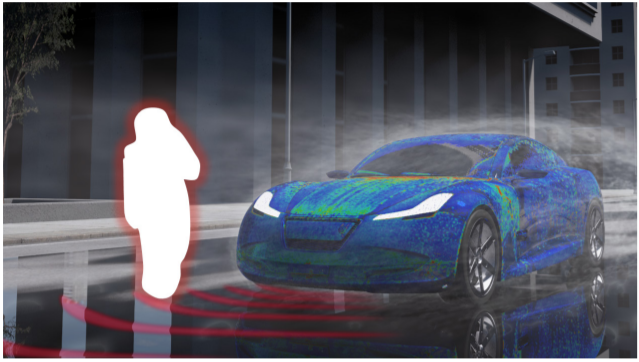
Co-site interference mitigation (RF desense)—identifying potential interference issues between systems
With so many components in close proximity, electromagnetic interference (EMI) and electromagnetic compatibility (EMC) are key concerns. The Interference Task in CST Studio Suite automatically identifies potential interference issues and produces an interference matrix showing which systems have the potential to interfere with each other. Engineers can quickly identify mitigation solutions, such as introducing additional filters or moving antennas to different locations to reduce interference to acceptable levels.
Human exposure compliance—ensuring that the exposure to electromagnetic fields remains within legal limits

Many classes of devices are subject to regulations on how much radio frequency (RF) power people near them may be safely exposed to. Realistic human body models can be added into the simulation environment and posed in and around the vehicle to allow exposure to be calculated without having to construct a costly prototype test set-up. KPIs, such as specific absorption rate (SAR), are automatically calculated by the simulation, allowing engineers to keep emitted radiation below regulatory limits.
Model-based-systems-engineering—defining and integrating system architecture up to full vehicle level
Before any components are nominated it is important to understand how the system as a whole is supposed to be designed. A methodology that has been used for decades in the aerospace industry, and is finding more and more favor in the automotive industry, is mode-lbased systems engineering. No Magic is the industry tool of choice to model systems and their interdependencies, and perform system level behavioral simulations. This is crucial in order to correctly size components and predict their performance.
Soiling optimization—modelling how rain, snow and mud spray can cover antennas and cameras
Fluid simulation, with PowerFLOW, models the behavior of rain, snow and mud spray and calculates whether their splatter can cover antennas and cameras. Using the results of the simulation, engineers can change the placement of sensors or adjust the design of the car body to reduce the risk of them being obscured.
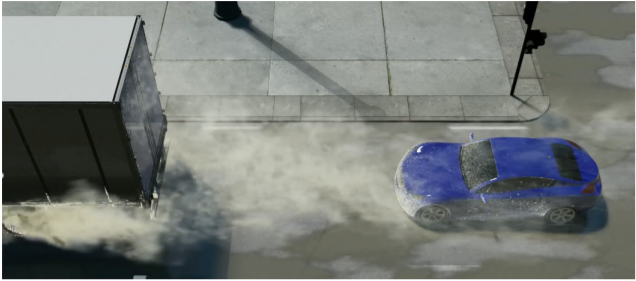
Vehicle Drive-Scenario Simulation—Building virtual environments for virtual test driving
With higher levels of autonomy the number of miles driven has become the main metric by which the maturity of a system is measured. In order to prove the reliability of an autonomous system under countless driving and environmental scenarios it is vital to train the systems with a wide range of data. Driving millions or even billions of miles with prototype vehicles in real life is not feasible. Simulation in high fidelity virtual environments is key in order to reach those “miles driven” milestones. AVSimulation makes it easy to generate realistic virtual environments and then define a variety of driving scenarios to be analyzed therein. Tight coupling with the 3DEXPERIENCE platform ensures traceability and consistency across all steps of the engineering process.
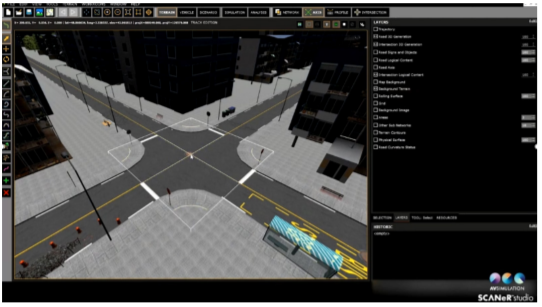
Wire harness electrical engineering—optimizing the cabling between sensors and on board computers ADAS sensors and other components are connected by bus cables combined into complex wire harnesses. Interference between different cables and wires can degrade the performance of ADAS and the other on board systems. CST Studio Suite can import cable harness designs and simulate these complex interactions efficiently, quickly identifying possible crosstalk and signal integrity (SI) issues.
CONCLUSION
Creating safe and reliable ADAS and Autonomous Driving Systems requires close collaboration and integration of high fidelity multi-physics simulation. Designing components and systems without taking these complex interactions into account is not possible while ensuring peak performance and adequate time to market. A combined modeling and simulation approach gives designers and systems integrators the tools they need to build a “virtual twin” of both individual ADAS components and full systems as an integral part of the vehicle, for testing without the need for a physical prototype. Thus ‘vehicles’ can be driven millions or even billions of virtual miles in realistic high fidelity environments to validate ADAS systems in a huge variety of realistic scenarios.
Dassault Systèmes offers a complete end-to-end solution for ADAS design on the 3DEXPERIENCE® platform, powering collaboration and communication between different stakeholders, bringing together all the different components and other data into a single source of truth while also protecting confidential information, ensuring full traceability throughout the entire development process. Enterprises employing this approach can not only cut development time and cost, but unlock untapped innovation and reduce risk on their way to the next level of autonomous driving.
SIMULIA offers an advanced simulation product portfolio, including Abaqus, Isight, fe-safe, Tosca, Simpoe-Mold, SIMPACK, CST Studio Suite, XFlow, PowerFLOW and more. The SIMULIA Community is the place to find the latest resources for SIMULIA software and to collaborate with other users. The key that unlocks the door of innovative thinking and knowledge building, the SIMULIA Community provides you with the tools you need to expand your knowledge, whenever and wherever.