The following article is based on the plenary presentation, Accelerating Business Value Through Unified Modeling and Simulation, presented at the 2021 Global 3DEXPERIENCE Modeling & Simulation Conference. Gregor Judex, SIMULIA WW Industry Consultant Director, and Daniel Pyzak, CATIA Mechanical Industry Process Consult-Management Senior Director, showcased a unified environment to improve productivity and collaboration during product development with the Dassault Systèmes 3DEXPERIENCE platform.
Modeling and Simulation Together?
Many of us are familiar with the expression “two heads are better than one” as a way to say that bringing multiple people together simultaneously to solve a challenge can achieve a better outcome more quickly. But how is this idiomatic phrase pertinent to the field of engineering? One word: MODSIM. In the past, modeling and simulation have been seen as separate yet equal entities, working simultaneously without being entirely associated. But trends in the industry, such as electrification, disruption from startups, and intense global competition, are accelerating change and increasing complexity. To keep up with these changes, product development cost and speed matter more than ever before. Companies can bring new and innovative products to market more quickly if they can iterate design alternatives faster. And when simulation is done early in product development, it can improve insight into performance and later validate requirements. Therefore, a modern system needs to enable full collaboration among those defining product requirements, designing the product, and validating performance. Let’s examine the development process further using the MODSIM approach to see how everyone benefits when modeling and simulation work together. With this project, we have many stakeholders working together and they will need an environment for collaboration. The 3DEXPERIENCE platform has a rich web interface where teams can share results, discuss any changes, perform analytics, and track tasks and progress.
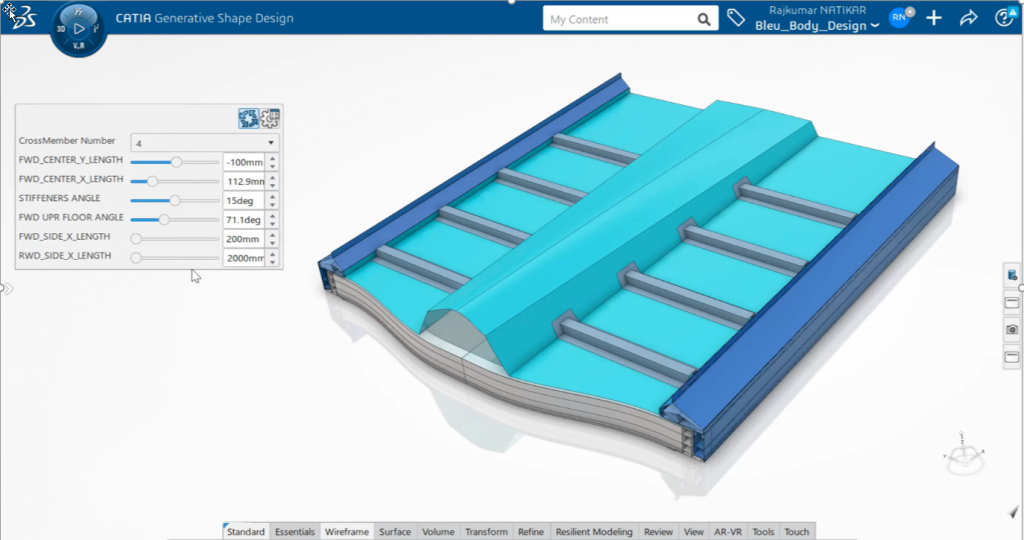
Example of MODSIM on the 3DEXPERIENCE Platform For this example, we will use modeling and simulation of a floor panel (figure 1) of an electric vehicle, showcasing a unified environment that dramatically improves productivity and collaboration by using the 3DEXPERIENCE platform. Every development process starts with requirements, so let’s start there. At the beginning of developing an electric vehicle, you need a lot of flexibility in the structure. For example, the batteries may not be fixed in size. The size of the batteries influences the panel itself, which has to be stiff enough to carry all the loads. And at the same time, it has to be soft on the boundaries to absorb enough energy in case of a crash. By tweaking the different parameters, we can then modify the floor panel of the vehicle.
Next, let’s move forward to another example to show you exactly how you can play with different parameters. In this particular case, we will optimize the stiffness of the roof panel to be about 33 hertz to avoid any vibrations in the roof. The variables we have to do this is first to move the stiffener itself, and then modify the height and the width of the beam. Now this seems to be an easy task, so to acknowledge the challenge here, while we are moving that stiffener, it has to adapt its length to fit into the width of the roof, and at the same time, we have to update the fastener as, as well.
So now, we can see the results of our initial design (figure 2) and we can start our performance study (figure 3) by simply selecting different parameters such as the height, the width, and the position of the beam. Then we move through the different positions automatically to see if everything regenerates well, and this is one step before we even start the optimization process itself.
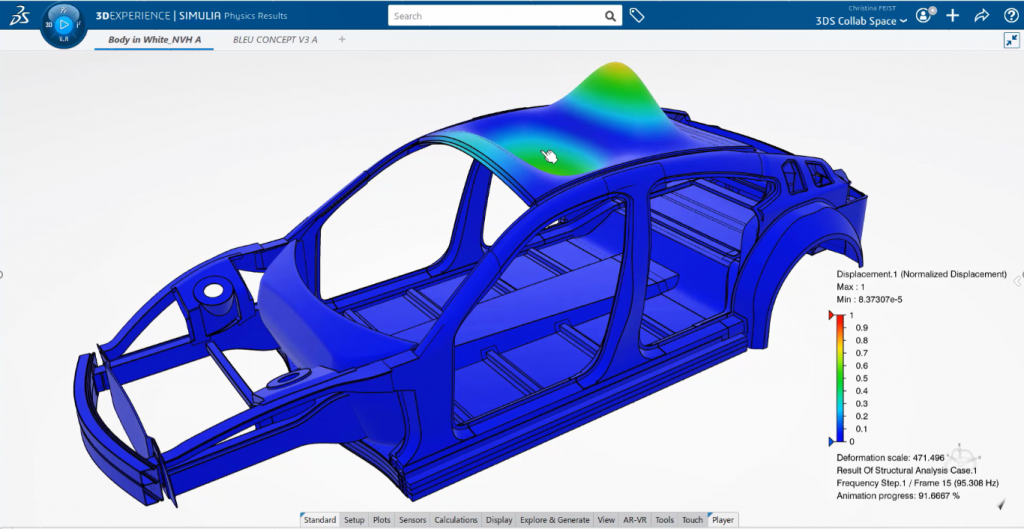
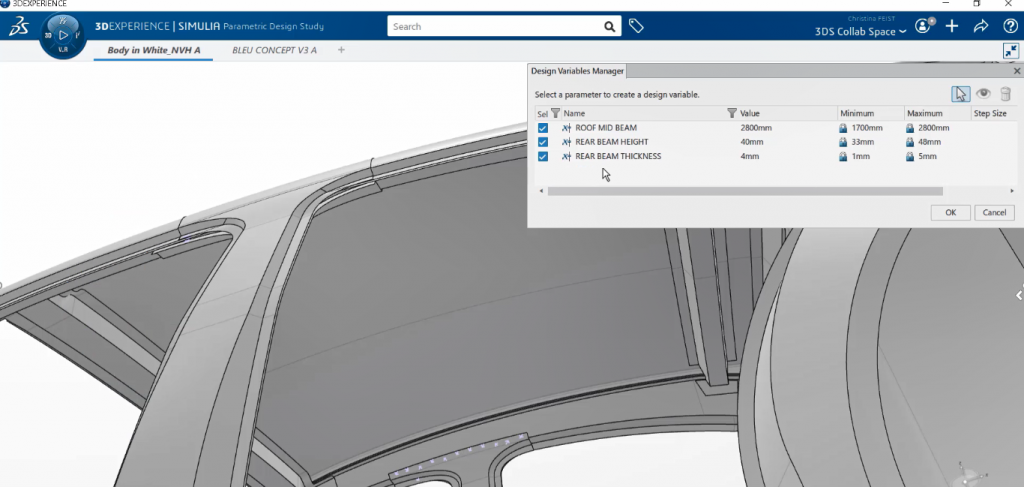
Once everything works, we can find what kind of response variables we want to use. For this example, we used the displacement of the roof, the frequency, and the total mass of the vehicle.
Now we launch the optimization process (figure 4). We will get multiple positions for where the stiffener could be. And now we can compare those best choices (figure 5) next to each other and then we can select which of those designs we want to use. Once a design is selected, we can store it as the new variant for that position, and we are feeding back that information and that process to our design experts.
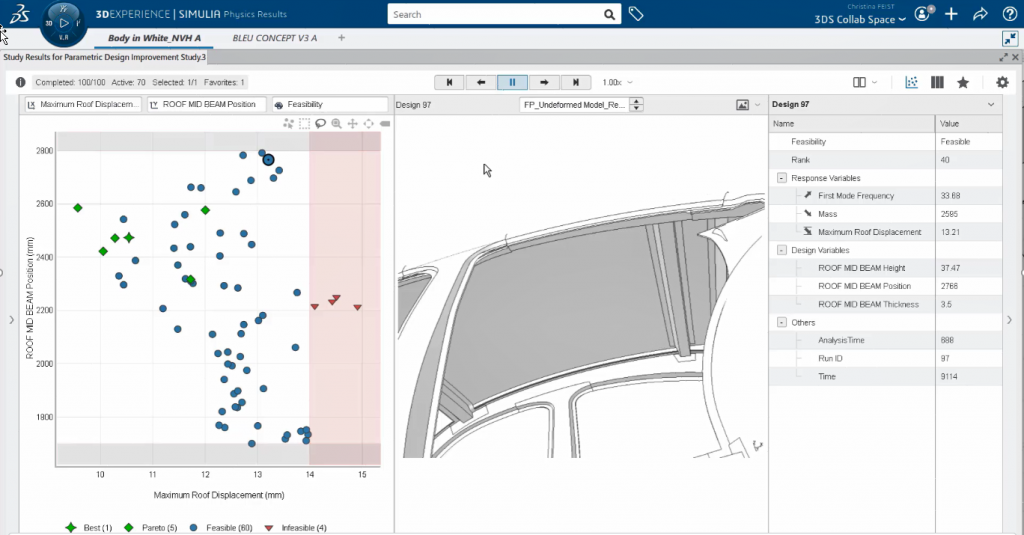
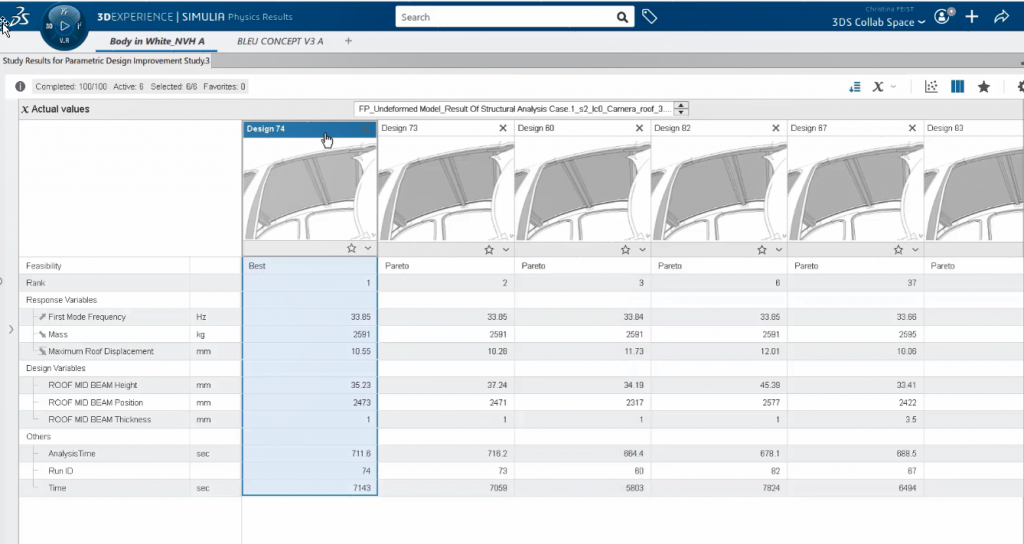
And now we can see the results of the final run (figure 6). Just a note that what we have been doing so far is within one specific domain. If we want to extend to multi-domains, we will need processes. We can create processes that can directly access all the objects within this experience and all the geometry parameters. Not only that but all the attributes of the simulation can be tweaked within the process as well. And if all those simulations are associative to that baseline geometry, you can start to do multi-disciplinary design optimization. So, we not only have the design engineer and the simulation engineer working together, there are multiple stakeholders all working collaboratively.
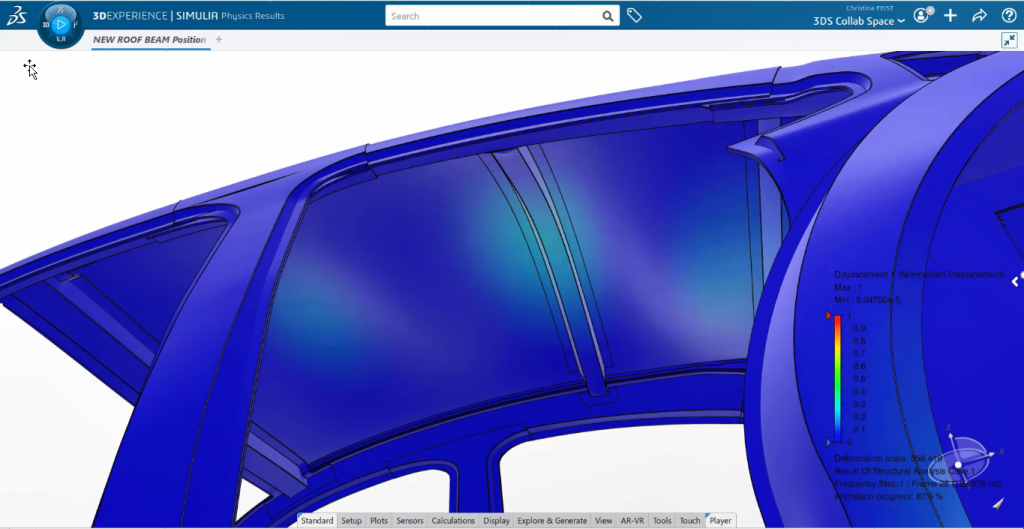
Future of MODSIM What does the future hold for MODSIM? And how will traditional roles evolve in the future? Customarily, the design came first, and then the simulation was performed. However, in the future, these roles may change. But more interestingly, there is democratization. We can use the same process we talked about earlier and put that in the hands of non-experts, maybe design engineers or other stakeholders within the company, to run sophisticated analyses. So, what simulation experts may do in the future is create simulation processes for non-experts. And a non-expert will never have to move into a different environment, using all of the features from within the 3DEXPERIENCE platform, attaining all the results needed for decision-making.
To learn more about MODSIM, the 3DEXPERIENCE platform, and to hear this presentation in its entirety, please visit the MODSIM website.
SIMULIA offers an advanced simulation product portfolio, including Abaqus, Isight, fe-safe, Tosca, Simpoe-Mold, SIMPACK, CST Studio Suite, XFlow, PowerFLOW, and more. The SIMULIA Community is the place to find the latest resources for SIMULIA software and to collaborate with other users. The key that unlocks the door of innovative thinking and knowledge building, the SIMULIA Community provides you with the tools you need to expand your knowledge, whenever and wherever.