By Fedja Sehic, Director of NETVIBES, Asia, Dassault Systèmes
The world we live in is full of new industrial constraints. Regulations around sustainability, carbon emissions, energy transition, and quality are all rapidly evolving with the new industrial age. We all are aware of supply chain disruptions, fast and dramatic changes in customer expectations, demands for mass personalization and the evolution of radically new business models.
The challenge faced by the modern industries like the automotive industry is that on one hand there are vast fluctuations in raw material costs. On the other hand, the industry which so far used to work with traditional tools, and restrictive methods and processes, is forced to change its ways of working to attract a new and upcoming workforce – generation Z and millennials – from whom the future generation of business leaders will emerge.
Humanity is at an inflection point of knowledge, data, and knowhow equal only to the renaissance in Europe. Today, the surfeit of information and data that people, organizations and enterprises can access and use to model knowledge and transform knowhow into new experiences has unleashed an ‘industrial renaissance’. It is critical during this industry renaissance that companies have a robust data science strategy that can create new experiences to carry the organization into the future.
The key question for organizational leaders is how do they transform data into information by building, deepening and enriching the context around it, modeling knowledge and then driving new experiences through know-how. Ultimately leaders need to understand how they are revealing ‘information intelligence.’
How Dassault Systèmes is at the center of the ‘industrial renaissance’
The technology vectors that are driving the industrial renaissance — elastic cloud computing, big data, artificial intelligence, machine learning, and internet of things – are precisely what Dassault Systèmes virtual twin experiences powered by data science are using to model knowledge and transform know-how for far better ways of running industrial processes and operations than was possible before.
Key to the new experiences is the virtual twin technology, which is far more dynamic and ‘realistic’ than digital twin technology. Virtual twin experiences are about combining three levers.
The first lever is the most advanced representation of the product, factory, or company. That can be 3D representations, systems, models, or ontologies. The second lever is all of the real-world data that organizations are capturing from any system and then projecting on to the virtual twin. The third lever is the people and the process for collaboration.
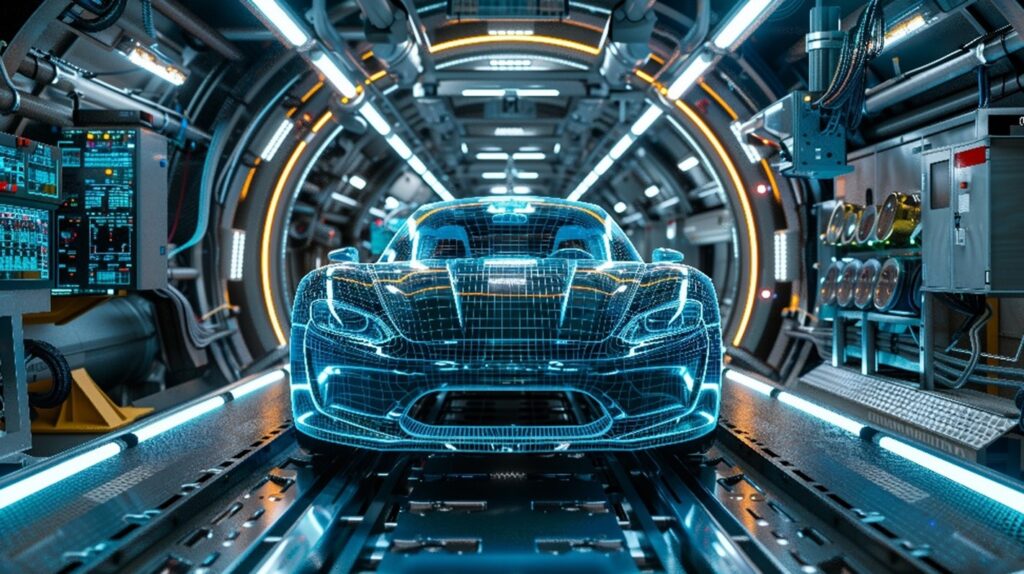
How does this actually apply in the industrial world? Consider the context of an advanced product like an aircraft. There is a lot of data around the system – stress data, simulation data, weight and balance data, raw-materials data, and suppliers data, coming from different sources. As soon as this data is projected onto the virtual twin it becomes contextualized by nature. This is the power of the knowledge model and deeply contextualized data.
Dassault Systèmes makes this model the foundation of knowledge. This means as an industrial virtual twin solution – Dassault Systèmes NETVIBES – can take any data from any data source and project it onto the model of the virtual twin to create realistic 3D experiences. How does this transform the manufacturing of cost sensitive and complex products like automobiles and aircraft?
3DEXPERIENCE platform dramatically transforms collaboration
First of all the Dassault Systèmes solution based on the 3DEXPERIENCE platform dramatically enhances collaboration. When people in manufacturing organizations think of collaboration they think of emails or messaging tools. These are in fact barriers to seamless collaboration. If for finding new ideas, risks, opportunities and threats the first thing executives are doing is sending an email then traceability and efficiency are ruled out.
The virtual twin brings people, processes, data, and the most advanced representation of the data in one place to make collaboration seamless and increase the possibility of innovation.
In the case of automotive companies, the 3DEXPERIENCE platform provides real life applicable solutions for key challenges such as price volatility of raw materials that can immensely affect profitability. The platform ingests and integrates the entire set of physical data of product lines — the configurations, variants, effectiveness, and the simulations as well as metadata associated with product lifecycle management (PLM) – which is all the physics that define the product.
On top of it is the collaboration engine which includes the change management, issue management, risk management, workflows, and visualization.
In the middle is where data science and AI combine to create the 3D experience. This is where external data from any source and data indexed at a part level is integrated on to the 3DEXPERIENCE platform’s ‘semantic lake’ that provides ontologies, intelligence and context on the data.
The decision-making process with the 3DEXPERIENCE platform brings stakeholders from costing, engineering, vehicle integration, simulation, and program management among others working on a unified workflow with real world data from the manufacturing ERP software and virtual data from PLM which is context rich. The data perspectives that they now have and the ‘inferred new data created’ helps the AI in the middle to provide instant real-world insights that then become actionable without sending a single email, or sharing a spreadsheet, or presentation file between the stakeholders.
How the 3DEXPERIENCE platform helps manage price volatility
By consolidating the data from the disparate and disconnected data sources the 3DEXPERIENCE platform can compute for any car configuration the composition of raw materials and accurately forecast how each car program would be impacted by varying price levels or fluctuations in the coming years.
At any time stakeholders can simulate and visualize all of the data and the impact of the various sensitivities in the virtual twin of the car using simple drag and drop features.
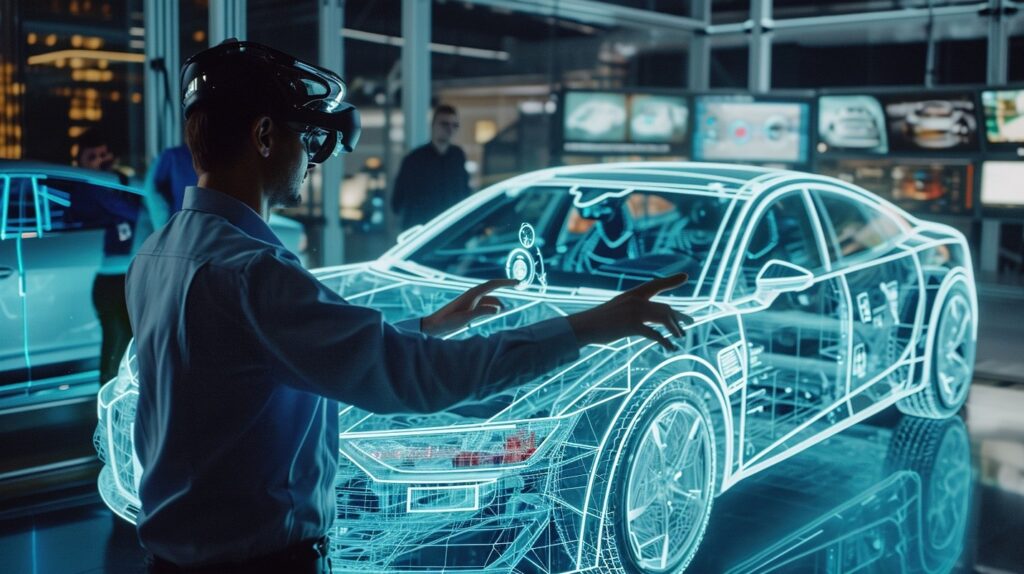
The procurement team has access to a dashboard that helps them visualize everything that has been purchased. They can understand the distribution of suppliers along with the sustainability index for all factory locations as well as supplier ratings. The procurement team can narrow down their options to the suppliers that provide the parts at the best cost and quality. With another drag and drop the procurement team can see all the similar parts that can be used as an alternative. Thereafter, an engineer can simulate and validate the new part on the 3DEXPERIENCE platform. As the challenge is tied to procurement savings, the simulation engineer can simulate, analyze and review it and share the simulation with all stakeholders.
Meanwhile in the middle layer, data science and AI improve data quality. A dashboard helps a data engineer manage the lifecycle of the data – assess the source and quality of this data.
As far as incomplete data such as parts not having the gross weight is concerned – data scientists can identify parts with similar gross weight and construct a model which helps infer a gross weight for those parts that do not have all the information around them. This is an example of how material cost intelligence improves data quality thanks to the embedded AI.
A bigger challenge is harmonizing all the data from all the data sources with a common business language. This data can be coming from procurement database, compliance database, PLM or ERP, other databases or even spreadsheets. The ontologies editor – which enables the creation of specific industry ontologies of a specific business model – resolves this challenge. For example, the raw material ontology builds the necessary consistency and relationships between the data sources for all of the stakeholders in this scenario.
NETVIBES delivers transformational outcomes across five domains
NETVIBES with the data science model and the 3DEXPERIENCE platform delivers transformational outcomes across five domains: planning, virtual product development, value network, customer experience, collaboration and intelligence.
In planning, business stakeholders can deliver programs and projects faster, on schedule, with enhanced quality and reduced risks to increase profitability.
As far as virtual product development is concerned, the platform helps engineering and manufacturing teams to optimize crucial factors such as cost and weight.
With regard to the value network, it provides AI for sourcing and standardization which in turn enables automotive teams to find the best components at the best price with the best suppliers.
When it comes to customer experience, the augmented AI provides unique data perspectives and value propositions on the product in the real world to drive enhanced availability and customer retention.
Finally with regard to collaboration and intelligence, the flexible AI foundation deeply contextualizes the output of data professionals, democratizes and universalizes the output through experiences that all stakeholders can contribute to and benefit from, using a single workflow. This ultimately sets the stage for faster innovation, assured cost savings and efficiency to drive profitability and sustainability amid price volatility.