This is Part 1 of our 6-part blog series based on our white paper, “The Top Five Reasons for Manufacturers to Improve Data Management.”
OVERVIEW
Today’s manufacturers face a host of challenges related to effectively managing product design and manufacturing data, not just within product development and manufacturing departments, but across the greater manufacturing enterprise. How well manufacturing organizations manage product and production data—and leverage this data to support related functions—has a direct bearing on a manufacturer’s ability to grow, as well as maintain and extend its competitive edge.
In an increasingly competitive global market, manufacturers must not only manage product and production data successfully, commonly known as product data management (PDM), they also need to effectively manage the distribution of product design and production data to related departments to improve their performance, a process known as distributed data management (DDM). This paper examines the top five reasons why manufacturing organizations should improve data management processes and the ways that Dassault Systèmes data management solutions can help them achieve their data management and business goals.
Reason #1: Boost Productivity
By improving data management, manufacturing organizations will be able to boost productivity by doing the following:
- Automating Manual, Repetitive Tasks – Throughout every manufacturing organization, a myriad of manual, repetitious tasks exert a real drag on productivity—tasks such as the manual creation of bills of materials (BOMs) or revision-checking on drawings. PDM tools can help you identify all of the manual, repetitive tasks in your workflows that can be automated, sped up, or eliminated, boosting productivity while establishing a more accurate, secure process.
- Minimizing Delays, Cost Overruns – Missing deadlines and going over budget are clear signs that your product development and manufacturing workflows are out of step and can benefit from the workflow automation that a PDM system provides. PDM tools can help manufacturers institute the automated workflows that can resolve time-intensive, costly issues and steps, and make schedule delays and cost overruns a rarity instead of the norm.
- Integrating PDM and ERP Systems – Many manufacturers rely on a product data management (PDM) system to manage product development and manufacturing data, and a separate manufacturing enterprise resource planning (ERP) software to manage all other business-related data. By integrating PDM and ERP systems so that they work in concert as a single system, manufacturers can realize additional productivity gains.
- Eliminating Wasteful, Redundant Processes – Every manufacturer has legacy processes that were once useful and critical to developing and manufacturing products, but no longer serve any practical purpose. As manufacturers increasingly rely on computer-aided digital technologies to design and produce products, a PDM system can help you scrutinize your existing processes and workflows, and then eliminate, replace, or automate outdated processes by utilizing PDM to revamp your workflows.
- Working Smarter Instead of Harder – Getting more out of existing resources to boost productivity does not necessarily require manufacturers to force staff to work longer, harder hours. An integrated PDM system will enable staff to accomplish more in the same amount of time—not by working harder, but by working more intelligently due to the automation and structure imposed by PDM.
- Accelerating Time to Market – As part of the development, production, and market introduction of all new products, manufacturers lose substantial amounts of time due to confusion, questions, and miscommunications involving data. With a PDM system supporting automated, formalized workflows, manufacturers can winnow out unnecessary instances of lost time and consistently accelerate product time to market.
- Achieving Additional Automation via API – While a PDM system can help your manufacturing organization automate many processes, choosing an integrated PDM system with an open Application Programming Interface (API) carries the potential for automating additional processes, especially those that are unique or custom to your products and manufacturing techniques.
A Case in Point: Boosting Productivity at CP Manufacturing
“We’ve been able to support rapid, sustainable growth without missing a beat, primarily because of our ability to automate sales, marketing, design, and production.” – Engineering Manager, CP Manufacturing
To read the full CP Manufacturing Case Study, download the white paper.
Part 1: Reason #1 – Boost Productivity
Part 2: Reason #2 – Improve Product Quality
Part 3: Reason #3 – Facilitate Collaboration
Part 4: Reason #4 – Increase Agility & Flexibility
Part 5: Reason #5 – Inspire Innovation
Part 6: Make Data Management a Competitive Strength with NETVIBES on the 3DEXPERIENCE platform
Download the “Top Five Reasons for Manufacturers to Improve Data Management” white paper
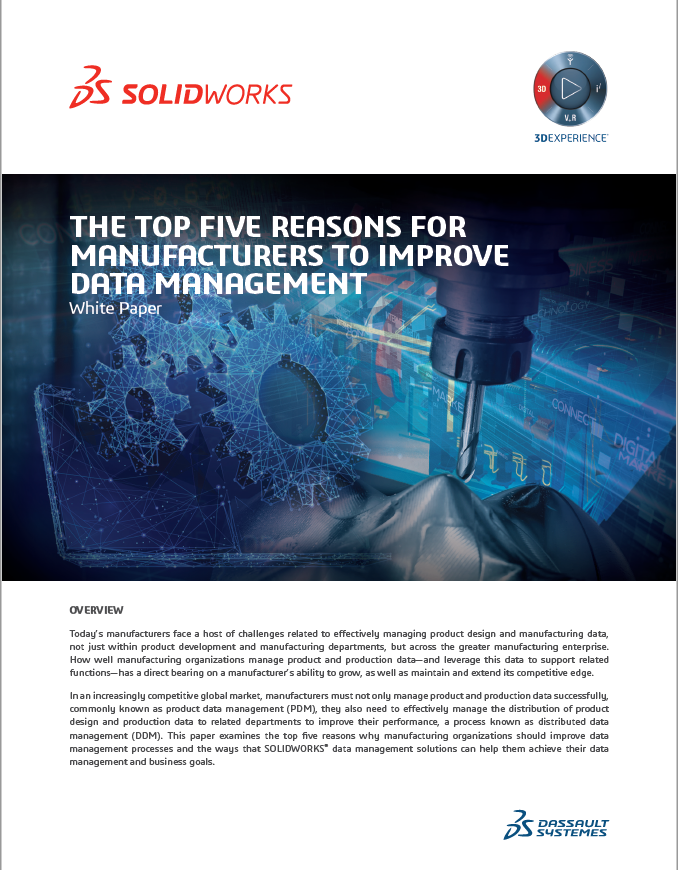
Join our User Communities to stay on top of the latest industry news, ask questions and collaborate with peers:
- EXALEAD Sourcing & Standardization Intelligence User Community
- 3DEXPERIENCE Marketplace | PartSupply User Community
- NETVIBES Public Community
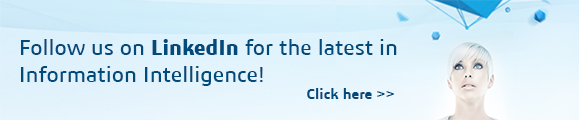