This is Part 8 of our 12-part blog series based on the LNS Research eBook,“Forging the Digital Twin in Discrete Manufacturing: A Vision for Unity In the Virtual and Real Worlds”.
Previously in Part 7 we explored how Digital Twin technology can simulate product use. Now let’s examine how it can simulate the manufacturing process.
Simulating the Manufacturing Process
Simulation adds tremendous value to the production process in manufacturing plants. Today companies mainly use it to zero in on process improvements and new product introduction (NPI). Engineers can adjust the virtual model of a process, test it and determine suitability on a “new” production line. Of course using a Digital Twin, engineers can try tens of thousands of possibilities for a system to determine which improvements work best with the process. Trial and error isn’t a good strategy when you’re testing on a real line but it makes complete sense with a Digital Twin.
In process industries like pharmaceutical, oil and gas, or even plastics there is a strong emphasis on the Digital Twin to ensure process optimization and predictive reliability. Simulation using a Digital Twin is key driver in asset-intensive industries. Use cases around running production lines in discrete manufacturing will rapidly emerge.
Discrete manufacturers, unlike process manufacturers, usually consider production assets somewhat secondary to the design and manufacture of the product itself. Digital Twin will dramatically change the way discrete manufacturers conceive the manufacturing process. When they start to use a Digital Twin to build a detailed executable model of the production line, virtual manufacturing will allow them to determine the most efficient way to produce goods and which changes are required when the product changes.
As we bring “cobots” to the shop floor (collaborative robots that interact with people and machines), the need for manufacturing process management becomes far greater. Simulation tools will be required to ensure safe operation and interaction between human and robot, working in the same unguarded spaces. In particular assembly operations that take place in encumbered spaces can hugely benefit from detailed “what if” analysis of the environment and the resources that share it.
Cobots, effective Digital Twins, and flexible machines will support a critical change that is coming in the manufacturing world: configure or design to order. The ability to change what you make and as how you make it in near real-time opens up new business opportunities for manufacturers.
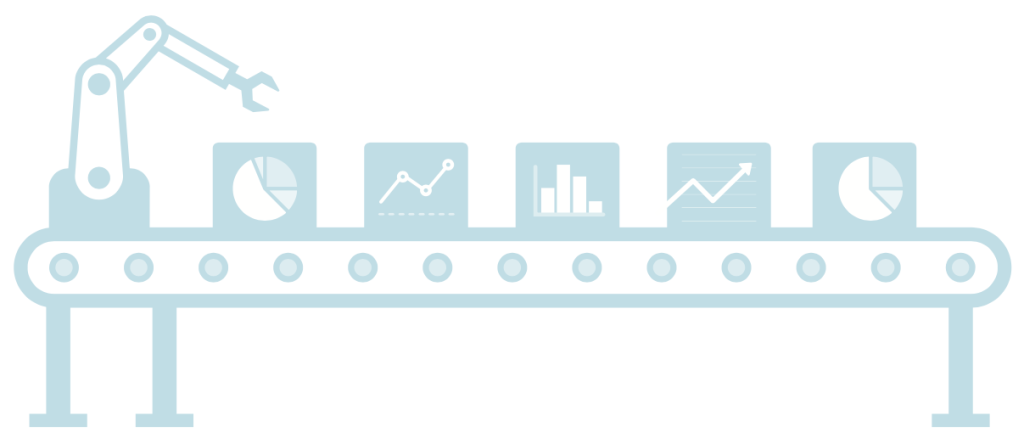
EXALEAD Commentary
Simulation is key, not only for the manufacturing process, but in general to understand and explain current or past situations and to predict future behaviors.
As a matter of fact, today every manufacturing activity is planned before it is executed. Any action’s duration and outcome is planned in advance to determine when and how to perform the next actions. The plans are shared with allstakeholders, including sub-contractors, suppliers and customers, where everyone conducts their own planning and relies on the accuracy of the others. In this tight relationship, any deviation from the plan will affect many people and create many side effects that will require modifying the plans.
The critical point that links all the activities is the reliability and the confidence level of each individual activity. Consequently, it is key for manufacturers to improve the reliability of each and every system.
That’s why simulation is so important: it helps us to understand in detail why and how phenomena are happening in space and time. Gaining a deep knowledge about the behavior of systems allows us to improve the accuracy of the mean time between failures.
Dassault Systèmes 3DEXPERIENCE twin Model Based Systems Engineering (MBSE) is providing a large set of models that allow manufacturers to improve functional (and dysfunctional) behavior, replacing empirical models or statistics which were previously used to evaluate the probability of failures.
If the reliability of products, assets, and systems could be determined with more accuracy, it would not be necessary to perform predictive maintenance in operations. This process is “only” needed today because people don’t have enough confidence in the reliability of the assets they operate.
Dassault Systèmes 3DEXPERIENCE twin MBSE is helping to answer the following questions: What are the major root causes that can lead to an equipment failure?
- Failure can be a design or an engineering problem: A 3DEXPERIENCE detailed root cause analysis helps to highlight the weak points in the system. A design failure mode and effects analysis helps managers review if and how the technical and functional requirements are covered.
- Failure can be related to manufacturing or assembly problems: A 3DEXPERIENCE product failure mode and effects analysis helps investigate the potential sources of errors, including: people, methods, material, resources, measures and context. EXALEAD analytics on the 3DEXPERIENCE platform help to monitor the quality and reliability of manufactured products by aggregating information from across operational and IT systems to deliver a 360-degree view of the assets, systems and products in space and time, as well as issues and deviations from the plan in the context of the 3D.
In the next blog installment, we will explore simulating the manufacturing process with Digital Twins.
Part 1: What is a 3DEXPERIENCE Twin?
Part 2: Digital Twins and Manufacturing: Today’s Possibilities
Part 3: Who is Using Digital Twin Technology?
Part 4: Growth Expectations for Digital Twins in Manufacturing
Part 5: Digital Twin Use Cases in Manufacturing
Part 6: Exploring Digital Twin Opportunities in Manufacturing
Part 7: Simulating Product Use with Digital Twins in Manufacturing
Part 8: Simulating the Manufacturing Process with Digital Twins
Part 9: Software in Digital Twin
Part 10: Real Data Versus Virtual Data
Part 11: Digital Twin: Pragmatic Considerations
Part 12: Recommendations for Getting Started with Digital Twin
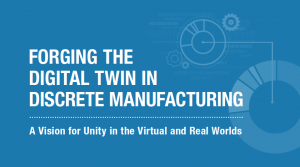
Read LNS eBook on Forging the Digital Twin in Discrete Manufacturing
Join our User Communities to stay on top of the latest industry news, ask questions and collaborate with peers:
- EXALEAD Sourcing & Standardization Intelligence User Community
- 3DEXPERIENCE Marketplace | PartSupply User Community
- NETVIBES Public Community
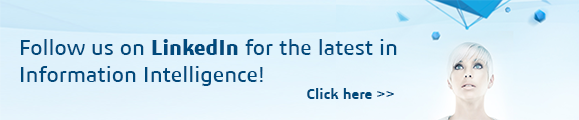