This is Part 11 of our 12-part blog series based on the LNS Research eBook,“Forging the Digital Twin in Discrete Manufacturing: A Vision for Unity In the Virtual and Real Worlds”.
Previously in Part 10 we examined real data versus virtual data in the Digital Twin for manufacturing. Now let’s look at pragmatic considerations for the Digital Twin.
Pragmatic Considerations
The LNS Research survey asked respondents about Digital Twin program ownership, and while the results are somewhat surprising, they’re also encouraging. Ownership by production and supply chain leaders implies that the focus is customers rather than internal. However, it also raises some questions about the role Digital Twin plays in technology integration across the enterprise.
A variety of initiatives drive industrial transformation in manufacturing companies. More importantly, we see an ever-growing number of top corporate executives getting involved–even if it’s the form of appointing a chief digital officer (CDO) or getting other senior executives directly involved (such as CIO or COO). Ultimately, their role is to set Strategic Objectives and set the course of industrial transformation. The enterprise objectives steer and accelerate decisions about platforms, tools, storage—indeed everything that makes up the IIoT platform.
In many ways, the Digital Twin evolved from an entirely different direction. In discrete manufacturing, PLM, Manufacturing Operations Management (MOM) software/MES, automation and even business systems such as Manufacturing ERP software matured over the years in the plant environment. Much of the early groundwork for the Digital Twin emerged from PLM platforms and connectivity beyond traditional 3D design. Decision makers should recognize this difference and must avoid a clash between IIoT and PLM platforms. So the Digital Twin can manifest the highest form of plant integration and support industrial transformation.
Gather a Team Rather Than Hand Over the Reins
This discussion brings us back to the question of who owns, and who should own Digital Twin projects. The survey revealed that among discrete manufacturers, production and supply chain leaders drive digital twin initiatives. As twin technology shifts toward production assets and development models, those heading up twin projects should also combine digital twin projects with the industrial transformation initiative.
The Digital Twin is here to stay the technology will rapidly become a critical part of modern manufacturing. Therefore, it’s inconceivable to keep them separate from the enterprise industrial transformation program. Manufacturing executives must appoint leaders with a breadth of experience and support in plant and business technology to drive transformation. The organization needs an extended cross-functional team that represents and can work with information technology, engineering, operations technology and more. Digital Twin requires proper IT/OT/engineering convergence.
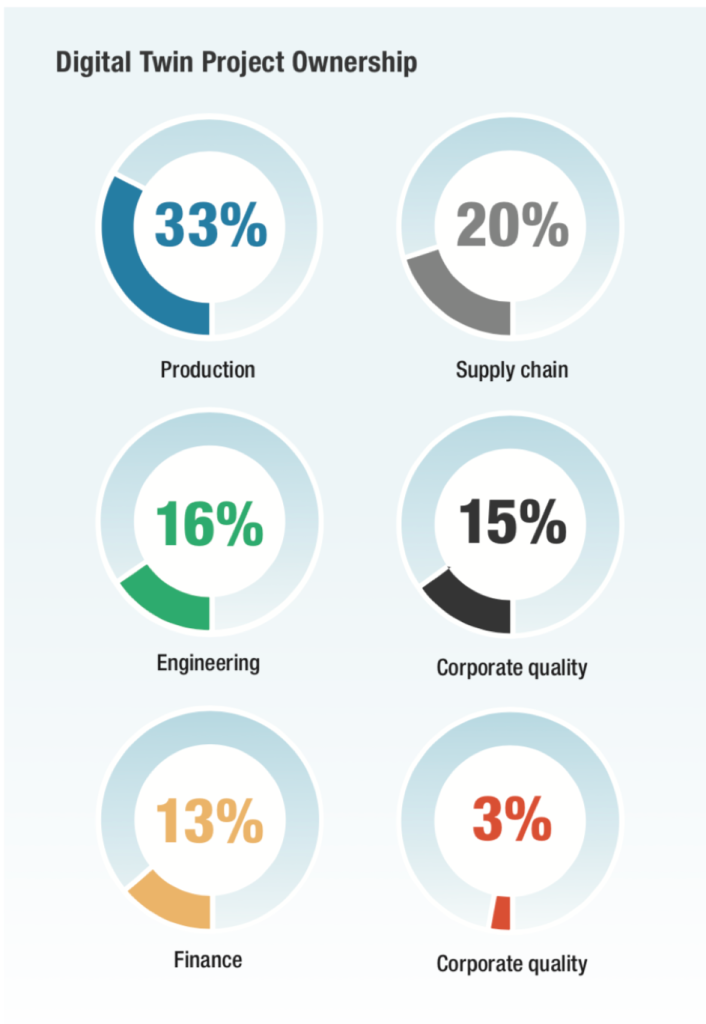
EXALEAD Commentary
If we agree that companies must improve their chain of digital continuity from product/process design down to the final user and back, is the Digital Twin the right answer?
The US/ANSI ISA95 standard (known under the ISO/CEI 62264 international standard) helped to clarify the functional scope of the main systems deployed in companies, including SCM, ERP, MES, SCADA, EAM, CRM applications. ISA95 focuses on the Site and the Area definition, whereas ISA88 focuses on the definition of Process cells. These standards widely helped to structure the interoperability between process control and automation levels-0-1-2, MES level-3, and ERP level-4.
What would be the benefit of adding a Digital Twin to the existing IT landscape? Is the Digital Twin a complete revolution or just an evolution?
If we look back in the mirror, the implementation of ERP/MES/SCADA/etc. initially helped organize the supply chain and satisfy mass production. Each system had its own decision-making application and only information related to the production progress was exchanged between the different layers working in silos. In their daily activities, stakeholders extensively used spreadsheets to complement existing systems by manually aggregating data from multiple sources. This is how the job was done.
Since then, several changes have occurred in the manufacturing industry:
- The adoption of lean manufacturing software has transformed production from push to pull mode;
- Many engineering changes have been made where necessary to sustain the transformation;
- The increasing number of product variants has “complexified” the supply chain in manufacturing;
- Real-time information updates and notifications of changes became a necessity; and
- The power of social networks moved the focus from “product centric” to “experience centric”.
For these reasons, companies started to implement data warehouses to collect the massive amount of data generated by all systems in a back-end. Analytics have developed as front-end applications to exploit and leverage the data.
With the extended enterprise, mergers and acquisitions, the number of data sources has multiplied, and it is increasingly complex to ensure consistency between the data sources and the data warehouse. Because of the need to maintain a structured information model of the data warehouse, it was difficult to capture exceptions and manage issues or unexpected situations—in other words, what is occuring on a daily basis. This type of information was instead exchanged between stakeholders through e-mails or stored in files shared on network drives or in SharePoint.
Although many Business Intelligence applications are capable of handling structured data, they do not easily support unstructured data sources, such as e-mails, documents stored in folders or SharePoint. Analytics produced by Business Intelligence applications are comprehensive for only a limited number of subject matter experts.
In the final analysis, the “silo effect” was not resolved. So, what can we learn from this experience?
Take-aways:
- Companies must rethink the way they are working today by undergoing a complete business transformation;
- For many good reasons, such as segregation of duties, several roles will have to stay hermetic, keeping tight control on the information exchanged; and
- Domain expertise cannot be explained easily to non-experts (and people don’t have time to do so).
What can solve the problem?
- Using a common communication vector to present results, visualize effects and understand complex phenomenon—that is, the Digital Twin;
- Sharing a single source of truth, including accurate, up-to-date information that is relevant in space and time; and
- Using the collaboration platform to work on ideas, notifications and issues, rather than losing track of information sent via e-mails.
EXALEAD is providing the technology that enables manufacturers to bridge a wide variety of data sources, delivering smart decision-making analytics solutions. Core applications, such as ERP, MES and EAM, can be connected to EXALEAD on the 3DEXPERIENCE platform without creating an intermediate data warehouse.
Legacy applications (e.g., homegrown spreadsheet applications) can also be indexed with EXALEAD to make the information accessible in the unified and single user portal hosted by the 3DEXPERIENCE platform.
In combination with ENOVIA Product Lifecycle Management applications on the 3DEXPERIENCE platform, EXALEAD is:
- Managing configuration changes that will ultimately happen over time to provide the agility companies need to adapt their business model to market demands;
- Handling massive (structured, as well as unstructured) data;
- Enriching information with metadata in order to deliver more powerful, efficient search capabilities;
- Processing complex computations via artificial intelligence (AI) and machine learning ; and
- Providing advanced full search capabilities (indexing engine).
Analytics become more powerful when connected to the systems they analyze.3DEXPERIENCE EXALEAD not only delivers user-friendly dashboards, but also reveals KPIs and heat maps in the context of the 3DEXPERIENCE twin. Information that may be abstract on a report or in a table can become significant when presented in the context of the system geometry represented in 3D.
EXALEAD on the 3DEXPERIENCE platform is:
- A powerful indexing engine connected to multiple data sources;
- An aggregation layer between heterogenous data;
- An analytics foundation delivering smart decision-making dashboards;
- An advanced search engine; and
- An infrastructure supporting AI processors.
SCM (Supply Chain Management), ERP (Enterprise Resource Planning), MES (Manufacturing Execution System) software, SCADA (Supervisory Control Automation & Data Acquisition), EAM (Enterprise Asset Management), CRM (Customer Relationship Management).
In the next blog installment, we will explore simulating the manufacturing process with Digital Twins.
Part 1: What is a 3DEXPERIENCE Twin?
Part 2: Digital Twins and Manufacturing: Today’s Possibilities
Part 3: Who is Using Digital Twin Technology?
Part 4: Growth Expectations for Digital Twins in Manufacturing
Part 5: Digital Twin Use Cases in Manufacturing
Part 6: Exploring Digital Twin Opportunities in Manufacturing
Part 7: Simulating Product Use with Digital Twins in Manufacturing
Part 8: Simulating the Manufacturing Process with Digital Twins
Part 9: Software in Digital Twin
Part 10: Real Data Versus Virtual Data
Part 11: Digital Twin: Pragmatic Considerations
Part 12: Recommendations for Getting Started with Digital Twin
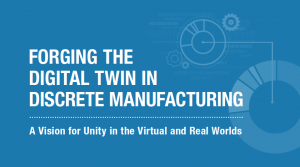
Read LNS eBook on Forging the Digital Twin in Discrete Manufacturing
Join our User Communities to stay on top of the latest industry news, ask questions and collaborate with peers: