CHALLENGE
A leading multinational provider of innovative aerospace products, services and solutions wanted to streamline its operations by building digital continuity into design, manufacturing and services for its products. It started with two goals: to create a standardized, searchable parts catalog that would optimize the reuse of standard parts, and to break down information silos so that multiple disciplines could collaborate at every stage of the product lifecycle.
SOLUTION
The company chose the 3DEXPERIENCE platform to help achieve both goals, starting with a single environment where every user can review, discover and collaborate across the product lifecycle. In addition, it deployed NETVIBES Sourcing & Standardization Intelligence solutions to automate parts classification and drive the use of standard parts in line with its policy of best pricing.
BENEFITS
The 3DEXPERIENCE platform facilitates extended virtual twin experiences, ensuring digital continuity for continuous improvement at all levels of the organization. Sourcing & Standardization Intelligence has helped the company to rationalize its parts catalog and assure the reuse of standard parts. This has made it easier to manage the parts inventory and stripped out unnecessary costs.
Reaching for the Sky
The customer is a leading multinational producer of aerospace products, services and solutions in the commercial aircraft, helicopters, defense and space sectors. As part of its digital transformation journey, the company wants to create a unified experience for all users. Its aim is to digitize design, manufacturing and services across all of its divisions and product lines.
“We are rethinking the way aircraft are designed and operated, streamlining and speeding up our processes with customer satisfaction in mind,” said the president. “Our digitization goals are a catalyst for change and with it we are building a new model for the European aerospace industry with state-of-the-art technology. Our target is a robust production setup that offers a reduction in product development lead time.”
The company had two key challenges to overcome as it built a foundation for its vision.
First, it wanted to streamline its parts catalog. In such a large organization, engineers introduce new parts every day. But under the existing system, they had to add each part to the catalog manually using an internal reference related to its manufacturing process. This required a lot of effort and introduced significant errors – in some categories, up to 50% of the references were incorrect. As a result, parts management was inconsistent and it was difficult to ensure accurate manufacturing processes.
Because referencing was the only method available to classify parts, designers were not able to search for what they needed by name, function or category. They often found it easier to source a new part instead of spending time grappling with an unwieldy search system. That made matters worse by adding more parts to the catalog, including many duplicates – and each one added expense, from design to testing to manufacturing, to the development cycle. As a result, it was getting more difficult both to manage the parts inventory and to adhere to the part pricing policy.
Second, the company wanted to ensure digital continuity by creating a single view of each product where everyone could work together. Employees at various points in the product lifecycle were struggling with data silos that made collaboration difficult. Users were working in different systems, where they produced and referenced volumes of data about individual processes. When someone required a single view for day-to-day tasks or specific analysis, they would have to spend hours or even days gathering data about each component’s design, tolerances, simulation results or in-service findings from different systems. Bringing all that data together in a single, collaborative virtual space would eliminate those challenges.
The company chose the Dassault Systèmes 3DEXPERIENCE platform to achieve these goals, focusing initially on its commercial aircraft operations. It deployed NETVIBES Sourcing & Standardization Intelligence applications to streamline and standardize parts management. And it harnessed NETVIBES data science solutions, with virtual twin experiences on the 3DEXPERIENCE platform, to unify data and provide a collaborative environment for users in multiple disciplines.
Optimizing Parts Management
Sourcing & Standardization Intelligence is a set of artificial intelligence-driven solutions. It gathers information from multiple data sources throughout the enterprise and helps users to quickly identify the parts they need and make informed decisions about whether to reuse existing or buy or make new ones. The company chose two applications – Reuse and Reduce – to transform its parts management from chaos to order. Starting with just one of its commercial aircraft programs, the company worked with the NETVIBES team to create a unique, automated classification system with intelligent search capabilities. Tens of thousands of parts have been classified thus far, with more than 95% relevance.
Thanks to NETVIBES Sourcing & Standardization Intelligence we can drive our designers to reuse standard parts. This reduces costs significantly.
Project Leader
Sourcing & Standardization Intelligence provides the organization with an intuitive solution that allows users to search for parts by characteristics including shape, supplier, cost and manufacturing method. The search bar’s auto-completion, wild card, spellcheck and multi-suggest capabilities make searching fast and intuitive. 3D parts are linked to metadata, so users can explore related information including testing, related designs and more. Results can be compared side-by-side based on attributes and shape similarity, with color coding to highlight any differences between parts. This ease of use has helped the company to maximize the reuse of standard parts and minimize temptation for designers to create new parts without realizing they already exist.
“Thanks to NETVIBES Sourcing & Standardization Intelligence we can drive our designers to reuse standard parts,” said the project leader. “This reduces costs significantly, because standard parts currently account for around 20% of the total cost of an aircraft.”
Meanwhile, the company has used Reduce to classify and de-duplicate its parts catalog. This has resulted in a slimmed-down legacy inventory and simplified parts system, cutting unnecessary costs in the process.
“We could visualize the benefits just two months after we deployed Reduce, because we had already identified duplicate parts,” said the project leader. “This is exactly what we expect from NETVIBES, to be at the core of the processes within the 3DEXPERIENCE platform.”
Digital Continuity for the Product Lifecycle
To streamline the entire product lifecycle, the company wanted to create a single digital environment in which every user can review, discover and collaborate on a 3D representation of the product. It was essential that users could navigate and retrieve information in a way that is relevant to their role, while also working seamlessly with colleagues in different disciplines and departments.
To make that a reality, the company deployed NETVIBES data science, enriching virtual twin experiences on the 3DEXPERIENCE platform, starting with two of its commercial aircraft programs. This solution brings together data from internal and external sources and uses AI, machine learning and analytics to provide contextualized information in a single 3D mockup of the project. In doing so, it provides a unique portal that supports deep investigation and fast decision-making.
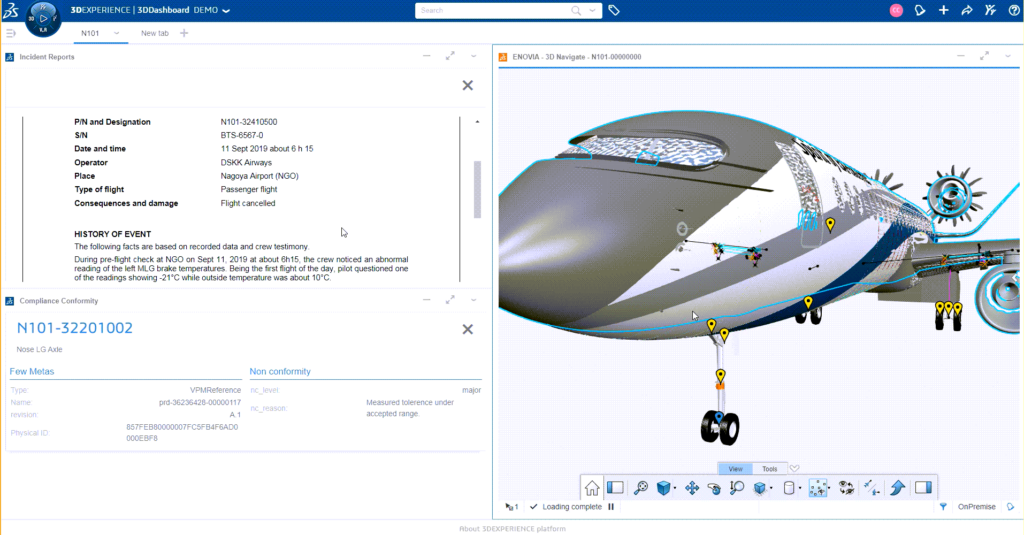
This allows users to search, visualize and explore different aspects of the aircraft, such as structural test data or in-service findings, projected onto the 3D model. In just a few clicks they can colorize the 3D mockup, select a point of interest and display all its properties in the context of business and industry knowledge. If they want to explore further, they can navigate to the corresponding data for in-depth investigation.
“The 3DEXPERIENCE platform is the backbone for digital continuity,” said Morgan Zimmermann, CEO of NETVIBES at Dassault Systèmes. “It will allow the company to gain end-to-end technology benefits, from product conceptualization through to manufacturing and service.”
Accelerating an End-to-End Vision
NETVIBES is central to the goals the company is pursuing on its journey to digital continuity.
Around 1,000 employees are already using Sourcing & Standardization Intelligence to search the company’s parts catalog, and that number is set to increase.
“In addition to our engineering community, new groups are asking to be part of the game,” the project manager explained. “Our procurement and manufacturing engineering communities expect to be able to use NETVIBES to identify opportunities such as changing the way a part is manufactured, to make it cheaper.”
Meanwhile, the company will continue to deploy its NETVIBES data science solution for new programs and use cases, with the eventual goal of making it available to its suppliers and to airlines. And it is migrating this solution to the cloud to enable faster launch of the 3D mockup.
Having started with a focus on its commercial projects, the company is also working with NETVIBES to drive digital continuity in other areas of its business. The results will include digital solutions that use big data analytics to help its military customers reduce maintenance effort, optimize fleet management and improve mission readiness.
In addition to our engineering community, new groups are asking to be part of the game. Our procurement and manufacturing engineering communities expect to be able to use NETVIBES to identify opportunities such as changing the way a part is manufactured, to make it cheaper.
Project Leader
These digital solutions are paving the way for breakthroughs in product design, performance, support and maintenance, customer satisfaction and new business models. Full digital continuity will improve its ability to co-design and develop the next generation of innovative aircraft with the manufacturing facilities that produce them, reducing costs and time to market.
“Aerospace is a unique industry where science, technology and art come together,” said Zimmermann. “Rapid transformation is a key characteristic of this sector, where continual innovation delivers complex new products and services that must work in highly regulated environments. Our customer is accelerating its digital transformation with NETVIBES on the 3DEXPERIENCE platform. With the digital continuity the platform brings, the company can capture insights and expertise from anywhere in its ecosystem and deliver exciting new aviation experiences.”
Download the eBook to discover more NETVIBES data science solutions in action!