By Kevin West, Senior Client Executive, Dassault Systèmes
The global mining industry is under increasing pressure to reduce its environmental impact and carbon footprint. As part of this effort, leading global mining companies are considering transitioning from traditional diesel-based vehicles to battery electric vehicles (BEVs).
BEVs offer several benefits over diesel-powered vehicles including reduced emissions and noise pollution as well as improved efficiency and lower maintenance costs. However, there are also a number of challenges and considerations that must be taken into account to fully transition to this technology.
Battery life expectations in usage
For BEVs, battery lifespan and replacement costs are key factors in the cost-benefit analysis against diesel vehicles. Battery technology is rapidly evolving, and there is no established baseline for the lifespan of batteries in mining operations. Manufacturers estimate the lifespan of batteries to be between five to seven years, although that may vary based on specific factors such as the operating environment and battery workload.
Mining companies should consider the battery’s expected lifespan, replacement costs, and potential maintenance costs when making the decision to transition to BEVs. While battery technology is evolving, companies should keep abreast of developments and factor in future improvements when making the transition decision.
Maintenance cost comparison across the asset lifecycle
While transitioning from diesel vehicles to BEVs, it’s important to consider the maintenance cost comparison across the asset lifecycle. One of the key advantages of BEVs is that they require significantly less maintenance than diesel vehicles. BEVs have fewer moving parts and do not require oil changes or other routine maintenance tasks that are necessary for diesel vehicles. This can lead to significant cost savings over the lifetime of an asset.
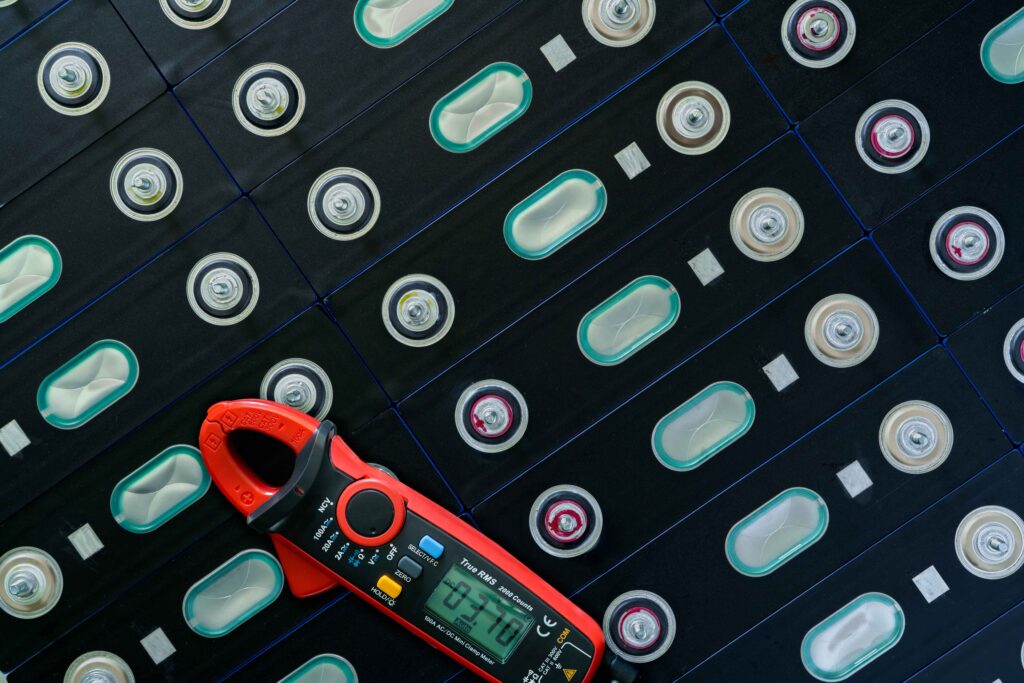
But while BEVs require less maintenance overall, the batteries do have maintenance requirements. The battery is one of the most important components of a BEV, and its maintenance and replacement costs can be significant. Additionally, the lifespan of the battery is typically uncertain and can vary greatly depending on factors such as the operating environment, usage patterns, and maintenance practices.
A comprehensive analysis of a BEV’s total cost of ownership is necessary to determine its cost-effectiveness compared to diesel vehicles. This analysis encompasses the initial vehicle cost, ongoing maintenance expenses, and potential replacement costs throughout the asset’s lifespan.
Mining operations are often conducted in high-temperature environments, where temperatures can reach up to 35-40 degrees Celsius. However, battery performance and lifespan are typically optimized for a temperature around 25 degrees Celsius. This poses a challenge for the mining industry as the increased heat in the operating environment can cause battery cells to expand and age quicker than usual.
The impact of heat on BEV performance and battery life is a crucial consideration for miners transitioning from diesel vehicles to BEVs. It’s important for battery manufacturers to develop cooling systems that can operate effectively in high-temperature environments to ensure that the batteries can meet the expected five-to-seven-year lifespan guarantee. Without proper cooling, the batteries may not perform as expected, leading to reduced efficiency and overall low lifespan.
How virtual twins help to reduce emissions
When it comes to recharging methods, it’s important to consider the level of operations to determine the optimal charge. Different charging methods are available such as trickle feed, which can be done overnight, in addition to rapid recharge, which is typically done underground. However, the best methods are yet to be determined.
Another consideration is that as the vehicles descend, they can recharge, so it’s important to ensure they don’t descend on a 100% battery. Instead, they should descend with a certain charge level to reach the optimal charge point by the time they reach their operating level. Simulation through virtual twin technology can be used to determine this optimal charge point.
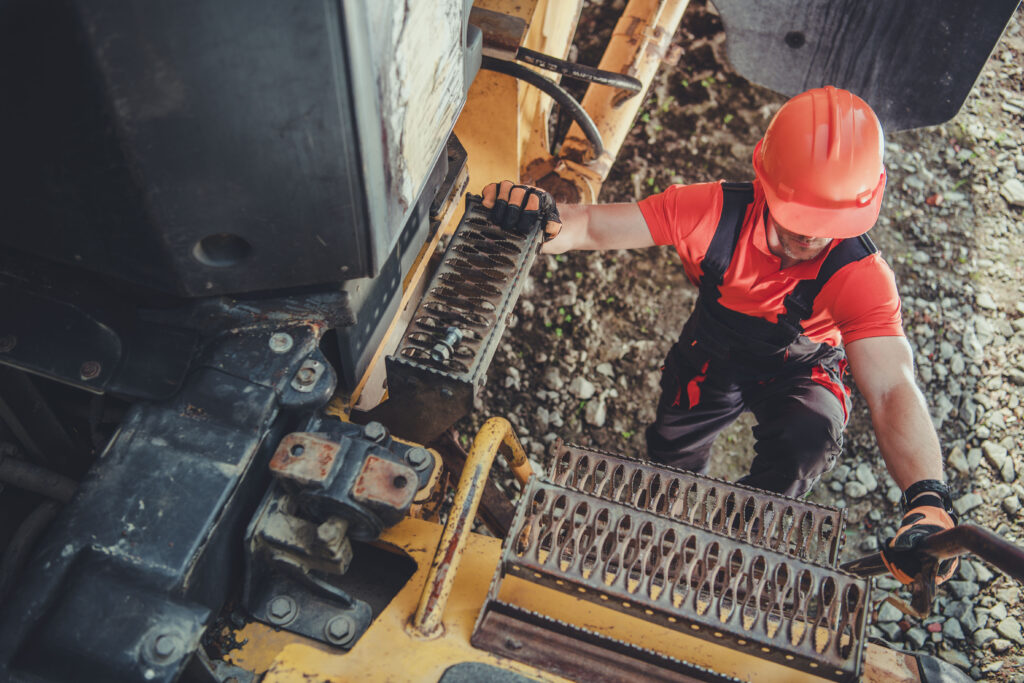
By using virtual twin technology, miners can gather data more quickly and efficiently to assist in maintaining reporting standards and meet mandatory ESG requirements. This will help attain emissions targets and improve environmental performance. Additionally, the use of BEVs instead of diesel-powered vehicles can result in significant emissions reductions and contribute to a more sustainable mining industry.
Meeting Scope 1 and 2 emission reductions
Most mining companies have set targets to reduce their Scope 1 and 2 emissions between 2030 and 2035. To achieve this, miners need to transition from traditional diesel-based mining methods to new methods, primarily BEVs. However, this is a significant challenge, as they must undo over 50 years of diesel-based mining learnings.
With a timeframe of seven to 12 years, mining companies can gradually phase out diesel vehicles and adopt BEVs. Technologies such as virtual twins can help accelerate this transition by enabling mining companies to gather data more quickly and efficiently to meet mandatory ESG reporting requirements.