GEOVIA’s Glenn Barlow talks about improving the accuracy of mine planning by enabling faster, more flexible scenario analysis compared to traditional methods. Historically, mine planning focused primarily on optimizing net present value (NPV), but today’s planners must consider a range of variables, such as production capacity, slope configurations, and environmental impact. Using advanced algorithms like GEOVIA Mine Maximizer (GMX), the system allows planners to explore thousands of potential scenarios by adjusting various inputs. This flexibility helps generate multiple optimized plans that can adapt to real-world disruptions and changes. By analysing a broad solution space, planners can make more informed decisions, ensuring stable, resilient mine designs with higher returns while accounting for future uncertainties.
Creating the optimal mine plan has been the cornerstone of reserve evaluation and development for years. But because planning takes a considerable amount of time and planners are working with estimations and forecasts, mine plans have always contained inherent inaccuracies and associated risk. This is a case study of the GEOVIA Strategic Mine Planner, which could reduce inaccuracy and create a mine plan that is better than optimal.
In decades past, it could take mine planners days or even weeks to optimise a mine plan. We can now complete this kind of analysis far more quickly, but at the same time the number of parameters and constraints we must take into account has increased exponentially. In the past, we were just trying to maximise net present value (NPV) – that really was the only output we were looking for.
Today, however, we must ask additional question, such as: What is the best mining production capacity for this operation? The most desirable slope configuration for this deposit? The best processing method and rate? Should we use multiple pieces of small equipment or fewer pieces of large equipment? The list goes on; plus we must also deal with new constraints in the form of important performance indicators such as land and water use and carbon footprint.
With this increase in questions and variables, the risk of not meeting plan expectations has also increased. Dassault Systèmes GEOVIA has developed a new suite of mine planning solutions which allow us to perform advanced scenario analysis.
This advanced analysis allows us to look at various KPIs, inputs, and parameters through what we call Designs of Experiments and Loops. Using it, we can generate a scenario based on costs, prices, constraints, capacities, etc., then vary those parameters over a range of different values, and finally look at the combination of all of the various parameters together. In other words, instead of generating one fixed output for one set of inputs, we can change the inputs thousands of times and generate tens of thousands of different scenarios, which we can then analyse.
The result is not only the creation of a Plan A – an executable plan that we want to achieve – but also a Plan B, C, D, E, and F that we can pull off the shelf as needed to respond immediately to disruptions, such as changes in site productivity, water consumption, carbon emissions, commodity quality, prices, costs, etc.
The evolution of mine planning
In the 1980s, Jeff Whittle was one of the first pioneers of mine plan optimisation. His Whittle set of optimisation products, since absorbed into GEOVIA, were based on the Lerchs-Grossman (LG) algorithm, which sought to solve the problem of what size the mine should be and how much material can profitably be taken out of it.
LG works well, but can be slow with the sizes that modern block models have gotten to; in 2008 a newer network flow algorithm called Pseudoflow was developed. Like LG, Pseudoflow gave mines the ability to generate their final pit shell and the phases that they wanted to achieve within it, but in a much shorter time. It could not, however, help mines determine where they should start to apply the additional constraints, cutoff values, costs, emissions, etc., that would help ensure they extract the deposit in the best possible way – i.e., it solved the problem of where but not when or how.
One way to deal with ‘when and how’ is to use a scheduling algorithm that works in a stepped approach: you create your final shell and your phases or pushbacks within that shell, then use the algorithm to generate a schedule based on your capacities for each selected optimisation period. This works, but the decisions you take in the first step are locked in: you can’t change them in subsequent steps, which means errors or issues persist across the entire schedule.
To help solve that issue, we implemented simultaneous optimisation (SIMO) in GEOVIA Whittle which, instead of optimising for a single period, seeks to optimise for all constraints and variables across all periods. Decisions are not locked in, so you can optimise later on to make sure that each block is mined at the best time for that period and at the best time for the entire schedule. This was an improvement, but it was slower than we liked and limited in the number of variables it could handle.
The search continued
Looking for an even better option, we started to explore the use of the Bienstock-Zuckerberg (BZ) algorithm, which can very quickly break down a large problem into multiple smaller problems which are easier to solve for. We discovered that, with BZ, we could replace our traditional linear programming techniques, which could take days to run, with techniques that could run much more quickly. Again, this was a solid advancement, but we thought there was still room for improvement.
In 2023, we launched our new GMX algorithm as the foundation of GEOVIA Strategic Mine Planning. GMX combines the power of SIMO with the speed of the BZ algorithm, enabling us to achieve better results than we could achieve with SIMO or the BZ algorithm alone.
Testing GMX against the best and biggest data sets we could find, we discovered that it dramatically reduced the number of iterations needed to solve specific mine problems – from 79 iterations using BZ alone to 16 iterations using GMX – while still maintaining an optimal NPV that is measurable on the sixth decimal place. It also dramatically reduced optimisation run times, with an average 69x reduction in run times compared to SIMO. This speed is vital when you want to run tens of thousands of optimisations on the full range of inputs, such as grades, commodities, processes, and stockpiles, as well as constraints, such as water consumption, trucking hours, and equipment type.
How it works: Mine A
Mine A wanted to determine the best direction to mine an open pit. A typical optimisation engine would analyse the proposed pit and come up with a single onion skin shape (no direction indicated), with incremental pits working their way out from the centre of the pit. However, while this generates an optimal NPV, is not a practical way to extract the material because it requires excessive machinery movement across all sides of the pit.
To investigate whether there was an optimal direction that would get Mine A close to the same optimal NPV as no direction, but using a practical series of shapes, we used GMX’s automated workflow to:
- generate 23 different pit options
- analyse each option from eight different directions and more than 200 potential starting points in each direction
- produce coloured shapes for each pushback and then, from those pushbacks, run the schedules and generate relative NPVs, and
- provide a total of 1,600 different scenarios in less than 15 hours.
The results indicated that there were starting points within three directions (Southwest, Southeast, and North) that would improve the NPV by more than 5 per cent.
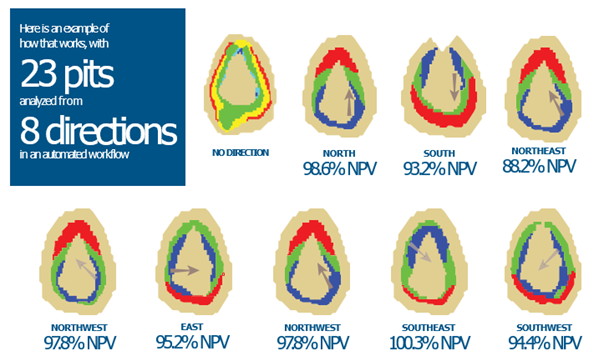
How it works: Mine B
Mine B had determined which option offered the best pushback dimensions for extracting maximum ore and had developed a mine design, but wanted to assess the quality and stability of their design over the life of the mine. To help them assess that, they needed to be able consider a broad range of factors against their impact on NPV. But standard optimisation engines usually only compare variables or constraints, like costs or prices, against each other but not against a value.
This graphic below is a 3D Surface generated by our Process Composer solution.
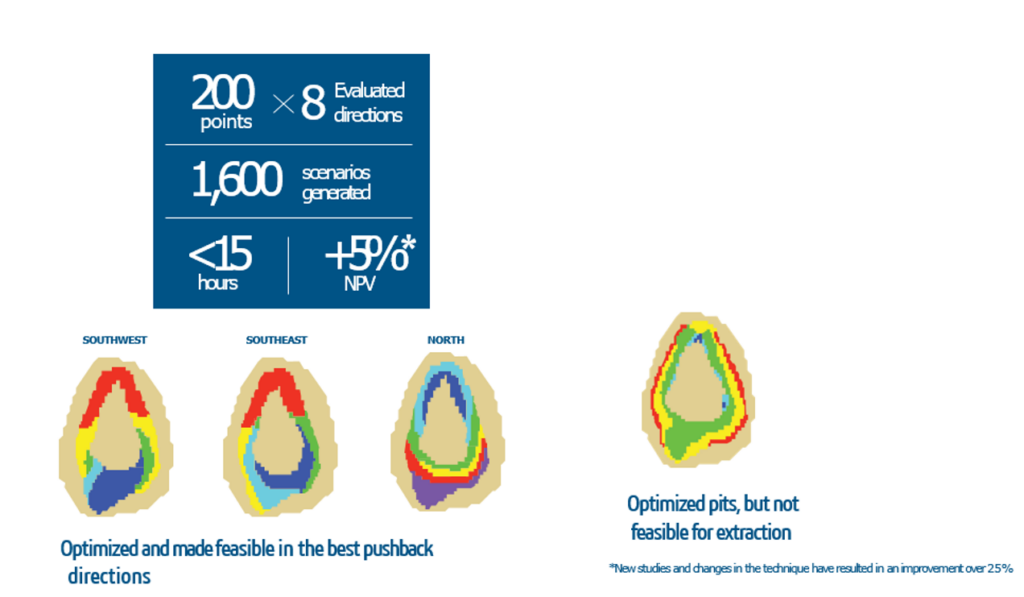
It shows Mine B where its maximum value is, and how sensitive that maximum value is to changes in production or cut-off rates. But what about other changes, like a drop in commodity prices, an increase in costs, or discovering the grade in the ground or the availability of the fleet is less than expected?
To help Mine B create a truly robust and stable design, we used Strategic Mine Planner to generate nearly 10,000 different possible production plans, each with its own NPV and 3D Surface visual, using varying cut-off grades, prices, CAPEX, waste facility locations, etc. – all within 24 hours.
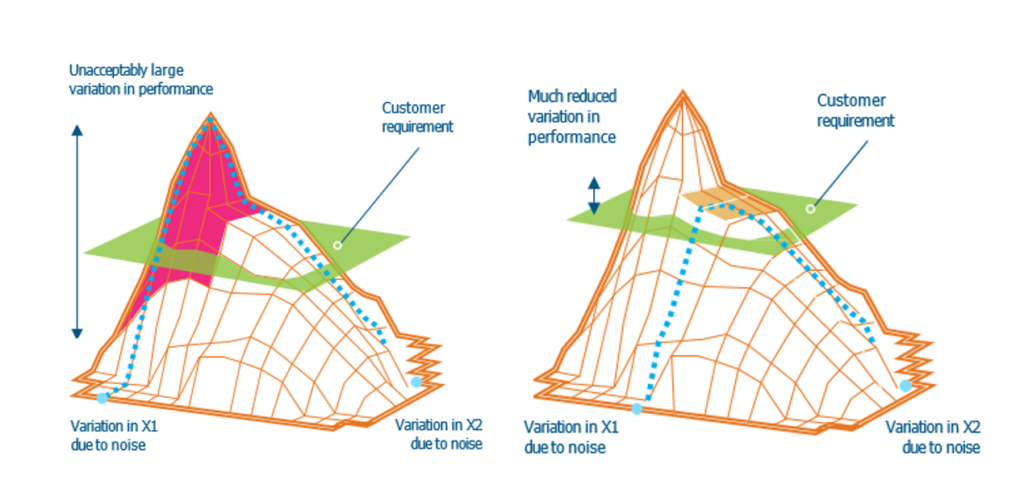
Through these 10,000 possible plans, Mine B was able to:
- examine critical questions, like whether they could get the payback they want, what the best fleet size or cut-off might be, and what effect price changes would have
- identify areas of stability that were close to optimal in terms of rate of return, payback period, or other KPI, but also remain resistant to small changes in variables, and
- both finalise a primary Plan A and fully understand the trade-offs made to arrive at that plan.
If the company changes its strategy to favour a different KPI in future (to minimise costs, or carbon dioxide, or resource utilisation, etc.), we can then simply change the weighting for that KPI and select the appropriate plan.
The big advantage of testing a wide solution space
By testing a wide solution space, we gain a far better understanding of the factors that make a successful plan for any given deposit.
To use a climbing analogy, we are able to see not just the peak of one mountain but the entire mountain range, and from this we can understand if our original mountain was really the summit we thought it was and how it differs from other peaks in the area. To bring it back to mining, we are able choose not just one single optimal mine plan, but also to understand that plan in the context of all the other choices and plans we could take – which means, we can, in essence, see beyond optimal and make better decisions because of it.
At the same time, Strategic Mine Planner is very simple to use. You do not need a mathematician or a supercomputer to run it. All you need is a mining engineer with a standard laptop who understands their deposit and cost models, and is able to define the KPIs that matter to their project.
Community is a place for GEOVIA users – from beginners to experts and everyone in between – to get answers to your questions, learn from each other, and network. Join our community to know more:
GEOVIA User Community – Read about industry topics from GEOVIA experts, be the first to know about new product releases and product tips and tricks, and share information and questions with your peers. All industry professionals are welcome to learn, engage, discover and share knowledge to shape a sustainable future of mining.
New member? Create an account, it’s free! Learn more about this community HERE.