Authored by Daniel Villa, GEOVIA Industry Process Consultant Expert.
In Article 1 of this series, an international copper mining company wanted to find out if it would be possible to increase productivity and reduce operating costs at a new block-caving project by changing their original design to accommodate new, larger load-haul-dump (LHD) machines.
Using a parametric design tool from Dassault Systèmes, they tested the effect of the larger loaders on their original mine design in four defined parameters:
- tunnel spacing (production crosscut, draw bells, etc.)
- undercut and extraction level elevation
- offset from geology contact, east/west access tunnels, and
- connection between levels through ore passes, ventilation raises, etc.
Owing to the efficiency of parametric design, these explorations took a matter of hours rather than days or weeks to accomplish, and the company was quickly ready to move to the next stage: figuring out whether these potential new designs would actually work the way they wanted them to.
Process Composer and PCBC mine planning tools
Using Dassault Systèmes’ PCBC mine planning tools combined with Process Composer, the copper company was able to easily:
- integrate their parametric designs with mine planning, and
- use automation and simulation of multiple scenarios to confirm whether or not changing extraction level design would in fact result in increased productivity.
To make integration simple, Process Composer eliminates the need for a designer to manually transfer the parameters and results from the parametric design into a mine planning package. Instead, it works with PCBC to handle the output variables of the design as input variables for the mine plan, allowing for an automated workflow throughout the entire mine planning process and between multiple applications/software.
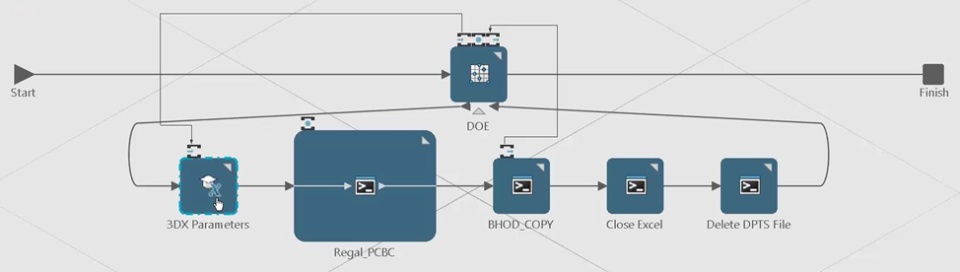
In the copper company’s case, PCBC automatically analysed the various parametric designs (signified by the 3DX Parameters box above) and then handed off to other tools to:
- generate new draw point distribution for each design
- create draw columns, based on block model and grade distribution data, to suit each tunnel spacing
- run best of height draw (BHOD) simulations to estimate economic mineable reserve, and
- calculate the tonnage, dilution, and grade of copper that could be extracted with the tunnels spaced at different intervals.
Draw columns
In this image, the draw columns generated by PCBC match extraction level tunnels set at 30m:
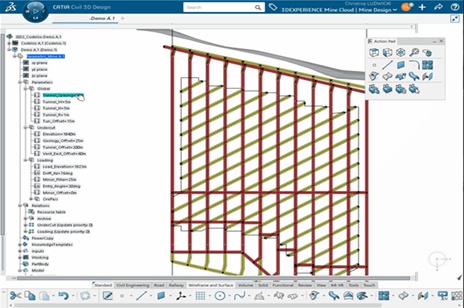
Here, the draw columns generated by PCBC match extraction level tunnels set at 36m:
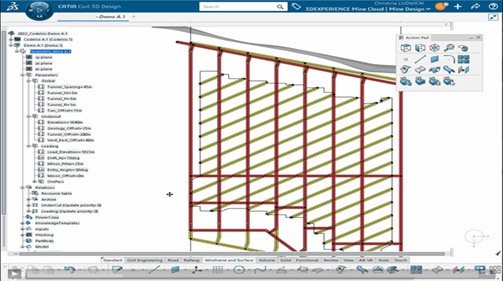
As you can see, however, the draw columns for tunnels set at 36m created much higher pillars between each draw point than tunnels set at 30m, which will affect the tonnes and grades the company will be able to extract.
Results
The copper mining company’s designer continued to use Dassault Systèmes’ PCBC mine planning tools to:
- vary other physical parameters, such as draw-bell spacing, entry angles, elevation level, and size of pillars
- run multiple scenarios to compare results, and
- for every design generated, calculate the economic reserve and create a summary of average copper value, average economic value, and total tonnes extracted — with all physical and economic parameters mapped to, and captured in, the Design of Experiment (DOE) process.
From there, the designer employed the Process Composer results analytics program to first review all the scenarios:
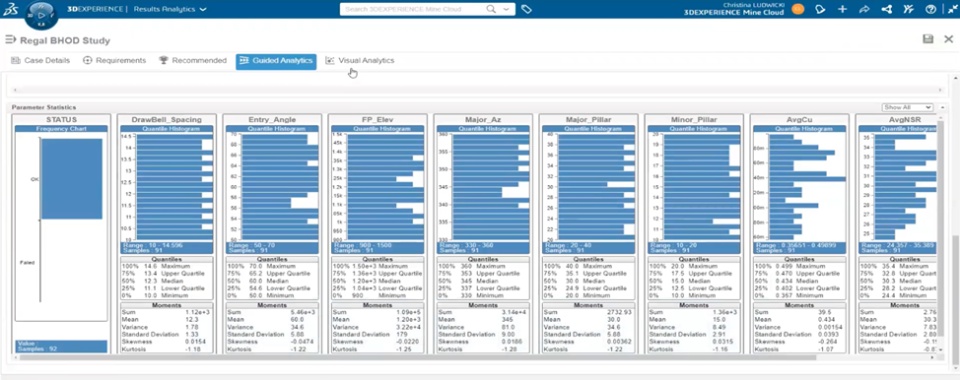
And then provide 2D or 3D visualisations of each design, where each dot represents one run of the simulation, making the results very simple to analyse and compare:
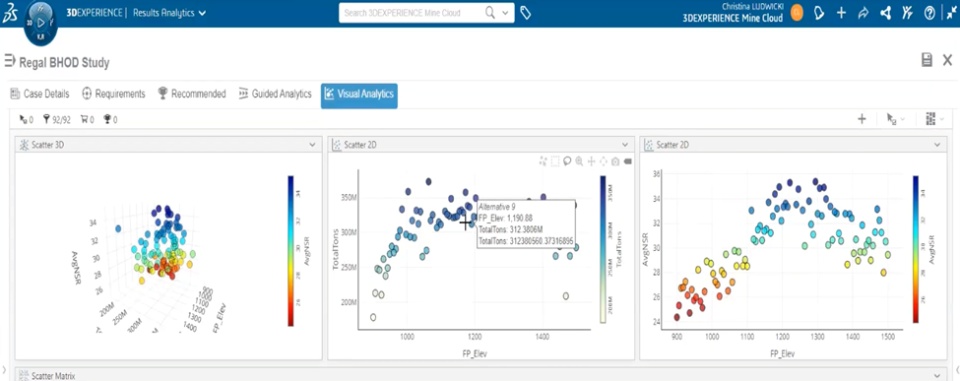
After that, the designer added the favourites, based on average NSR, to a basket for more in-depth review.
What comes next
The next article in this series will look at how the copper miner employed simulation to complete advanced geotechnical analyses. The final piece will discuss how the company evaluated thousands of production scenarios before arriving at a design that would create a smaller but significantly more productive underground mine than its original mine design.
Community is a place for GEOVIA users – from beginners to experts and everyone in between – to get answers to your questions, learn from each other, and network. Join our community to know more:
GEOVIA User Community – Read about industry topics from GEOVIA experts, be the first to know about new product releases and product tips and tricks, and share information and questions with your peers. All industry professionals are welcome to learn, engage, discover and share knowledge to shape a sustainable future of mining.
New member? Create an account, it’s free! Learn more about this community HERE.