This post has been contributed by Kevin West – Senior Client Executive, Asia Pacific South, Dassault Systèmes.
Mining companies are facing a range of challenges that are shaping the future of the industry. From increasing demands for sustainability and environmental, social, and governance (ESG) compliance to supply chain disruptions and the need to replace aging assets with more capable and efficient technologies, companies must navigate complex issues to remain competitive.
The push towards sustainability and mine electrification is gaining momentum, and many mining companies are exploring ways to reduce their carbon footprint, and improve safety and health outcomes for workers.
Sustainability and mine electrification
Mining companies are currently dealing with increased pressure to reduce their environmental impact and adopt sustainable practices.
“Companies are focusing their efforts on mine electrification, which has the potential to reduce diesel particulate matter (DPM) and improve safety outcomes for workers.”
DPMs from diesel vehicles in underground mines can cause serious health issues, including lung cancer, and are the second biggest cause of lung cancer in Australia after smoking. The high costs associated with ventilation in underground mines make reducing DPM a critical challenge for mining companies. In fact, 80% of underground mining costs are attributed to driving ventilation fans.
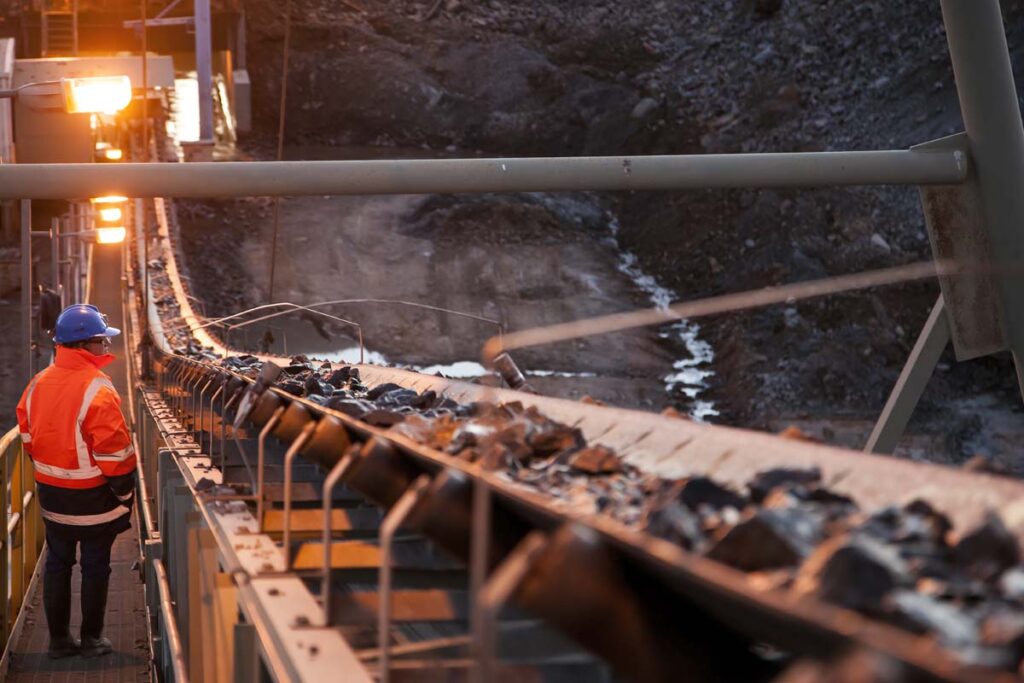
However, reducing DPM and improving safety outcomes for workers can also lead to business benefits, such as reduced healthcare costs and improved productivity due to a healthier workforce. Therefore, many mining companies are exploring ways to reduce DPM and improve safety through electrification, such as through the adoption of battery electric vehicles (BEVs).
Asset replacement
As mining equipment ages and becomes outdated, mining companies need to replace them with newer assets. The use of BEVs offers several benefits.
“For instance, BEVs have fewer moving parts than diesel engines, resulting in lower maintenance costs. In addition, BEVs emit lower carbon, heat, and noise emissions, making them an environmentally friendly option.”
However, transitioning from diesel to electric engines comes with challenges. Mining companies need to acquire specialized equipment maintenance management software skills to deal with BEVs. As a result, there will be a need for repurposing diesel fitters to become battery maintenance specialists.
The objective of this shift towards BEVs is to improve mining capability. By replacing outdated equipment with more advanced assets, mining companies can increase their efficiency and productivity while reducing maintenance costs.

The electric mine template
Electrification is a rapidly growing trend in the mining industry, with the aim of making all new mines primarily electric-powered within the next 5-10 years.
“The primary objective of electrification is to achieve cost savings, as well as reduce carbon, heat, and noise emissions. By reducing heat emissions, ventilation costs can also be lowered.”
Traditionally, ventilation fans have been used to cool down mines, but with the reduction in heat, their use can be minimized, driving down costs. Additionally, noise emissions in mines can cause hearing problems for miners working in confined spaces. The use of electric engines can reduce noise emissions, contributing to a safer work environment.
To accelerate the implementation of mine electrification, mining companies are working on a template for future electric mines. This template will help companies hit the ground running more quickly, with a clear plan for implementing electric power in all aspects of mine operations.
Interdepartmental collaboration
Collaboration is crucial in the mining industry. From sustainability and mine electrification to asset replacement and the future electric mine template, each of these initiatives involve multiple departments and stakeholders working together to achieve common goals.
“One of the tools that Dassault Systèmes offers to enable collaboration is the Vehicle Energy Management solution. This out-of-the-box solution leverages a collaborative, comprehensible, and multidisciplinary systems platform to optimize the energy management of vehicles in mining operations.“
The framework for the solution is as follows:
- Work requirement specifications through trade-off analysis and decision making.
- Systems architecture and simulation as well as vehicle performance synthesis.
- Collaborative environment to connect multiple departments to identify the best solution.
- Model within a Loop Environment for Vehicle and Control Tuning (repeatability).
- Open platform for collaboration.
The Vehicle Energy Management solution is designed to bring together different departments, each with their own objectives, to identify the best solution for everyone. In gathering all the information required, we interviewed the following departments:
- Maintenance
- Finance
- Health and safety
- The miners themselves
- The sustainability team
The collaboration between these departments is crucial, as each one has a unique perspective that can contribute to the decision-making process.
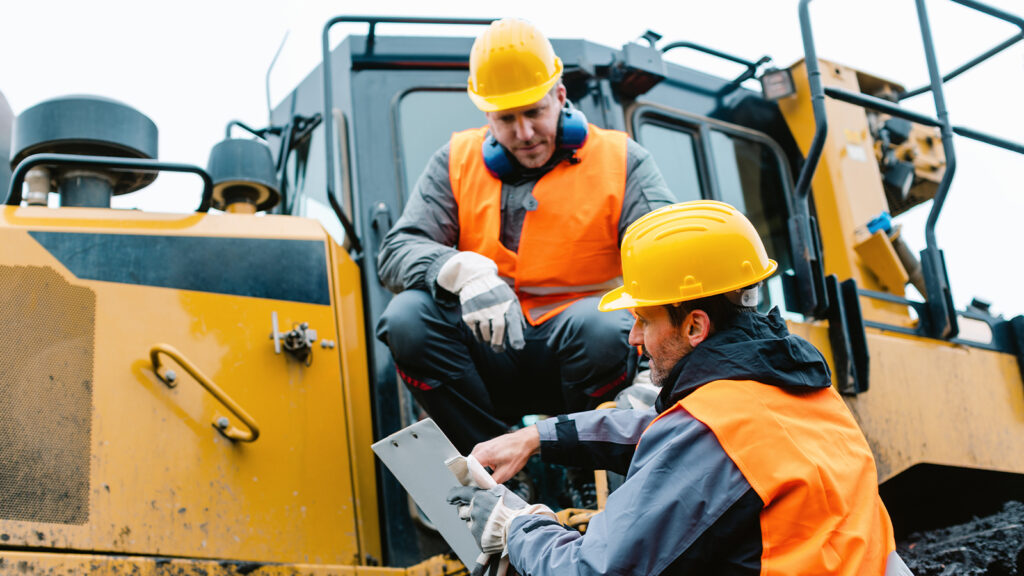
This is the whole backbone of why we have the 3DEXPERIENCE platform: to allow for these interactions. We have common problems, but we do not want to see them in isolation. The impact of a decision on one end has an impact on another end. This way, everyone in that loop is connected. Ultimately, the decision on acquiring assets needs to take all five departments into consideration to ensure that everyone’s needs are being met.