On the road to Operational Stability, one of the key considerations is the management of production mining activities, both planned and actual. To successfully achieve effective mine production management, you must ensure you fill these six requirements:
1. Intuitive and rich reporting, drill down and navigation
The Mining Industry needs clear and easy-to-use production reporting that is not just automatic, but is also interactive and adhoc/on-demand. While it’s common for Operations to have a standard Daily, Weekly, and Monthly Production Reports that can be generated with the click of a button, it is also important for Subject Matter Experts (SMEs) to browse the information with different levels of detail and from different viewpoints. Providing modern-day dedicated/pre-calculated analytics can afford these experts to fully understand and explain the information they may be seeing on a chart or display – and when there are issues with the information, drill down to the tooling required to correct and adjust discrepancies.
2. Fast deployment allowing quick benefit realization
Defining a plan for Mine manufacturing production and management software can often be perceived as daunting. Production Mining is a very dynamic process when compared with manufacturing processes, for example, which are generally much more controlled and predictable. It’s important to develop an iterative approach to Mine Production process improvement that may involve first centralizing and automating your Daily, Weekly, Monthly reports, then beginning to address the important feedback cycle between planned and actual, finally developing a reconciliation approach that allows you to manage data discrepancies across the entire mining value chain (from Mine -> Mill).
3. Complete integration capability with all systems, including manufacturing ERP software
Automation of data integration is an important enabler in any Mine Production Management solution. The connected mine (even underground nowadays) is increasingly fitted with sensors/devices for most/all of the key mining processes (fleet, conveying, processing, etc.). Typically this data is very raw in nature and may be difficult with which to work for reporting and aggregating, etc. The longer it takes SMEs to manually integrate and aggregate the information, the less value the information is likely to have before it can be used. Looking at historical data has value but why not take a look at the current situation while there is still an opportunity to influence outcomes? Not to mention, there is a high likelihood for error in manual processes. Automation of data integration is also becoming increasingly pivotal in bridging the gap between OT (the plethora of raw data systems in Operations) and IT (corporate systems, including ERP).
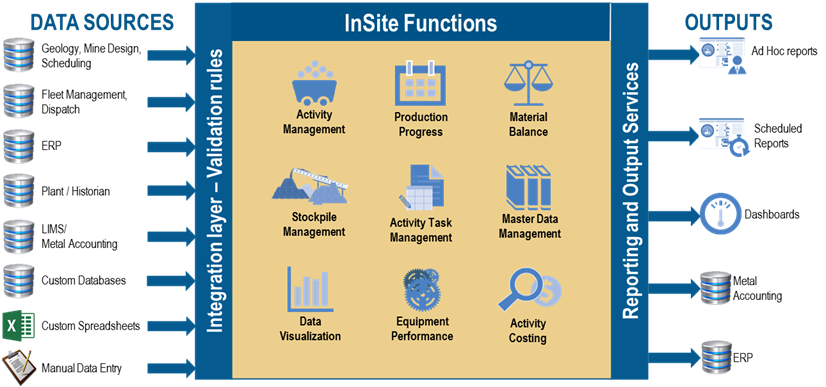
4. Single point of access to all operational data
One of the key challenges in Mining is system overload: too many software silos – typically with no single point of entry or view of operational data. Regardless of the systems and datasets involved in production processes, the user experience for reporting, data analysis, and reconciliation needs to be standard and consistent across all departments in order to achieve stability.
5. Self-reliant operation of a solution and easy configuration
Further speaking to the point that Mine Production processes are dynamic, providing solutions to execute these processes must also by dynamic and flexible. Control Room and Technical Services SMEs need to feel like they are in charge and not hindered by rigid controls or workflows. Arriving at the perfect recipe of decision-making intelligence and agile execution is important.
6. Capture of deviation from plan issues and decision support
Historically, execution of mining activities and planning of mining activities have been largely disconnected. Mine planners would produce a schedule, and pass it over to Operations. Operations would run with the provided schedule, but typically deviate from the plan with little or late reporting back to the Scheduling Department. However, Operations are increasingly acknowledging a need to better connect these processes to better understand the discrepancies between scheduled and actual much more quickly and effectively.
Typically activities planned and actual are managed separately as distinct processes/workflows. Actual Mining activities are just a series of instances or executions of planned activities. From an information perspective, they contain the same attributes: locations (possibly source and destination), equipment units, employees/operators, material code/type, volumes/tonnes, grades, hours, etc. While the types of activities that make up the end-to-end process may include variable attributes, the planned and actual activity attributes for any activity should be a very close match. Even if we are collecting more information about the actual execution of the activity than what could be planned/or predicted, there should be a close correlation between what was planned and what actually happened (in format).
Gain Control of Mine Production Operations with a system that encompasses these six requirements
Dassault Systèmes provides mining applications to increase the confidence in mining operations’ ability to meet production targets, manage costs, and improve efficiencies to meet stakeholders’ expectations. Its GEOVIA InSite™ application provides up-to-date information for improved visibility into production activities, enabling in-shift control and support of material reconciliation across the mining value chain. InSite provides operations with real-time data analytics to support decisions and enables conformance to plan. Delivering auditable transactions and master data management, InSite centralizes Operational Technologies and gives you the information to drive the business excellence and agility required to thrive in fluctuating mining and market conditions. With an interactive graphical user interface, InSite’s fully customizable dashboard helps navigate the system through visualization to both see and understand all areas of variance across mining operational processes and activities.
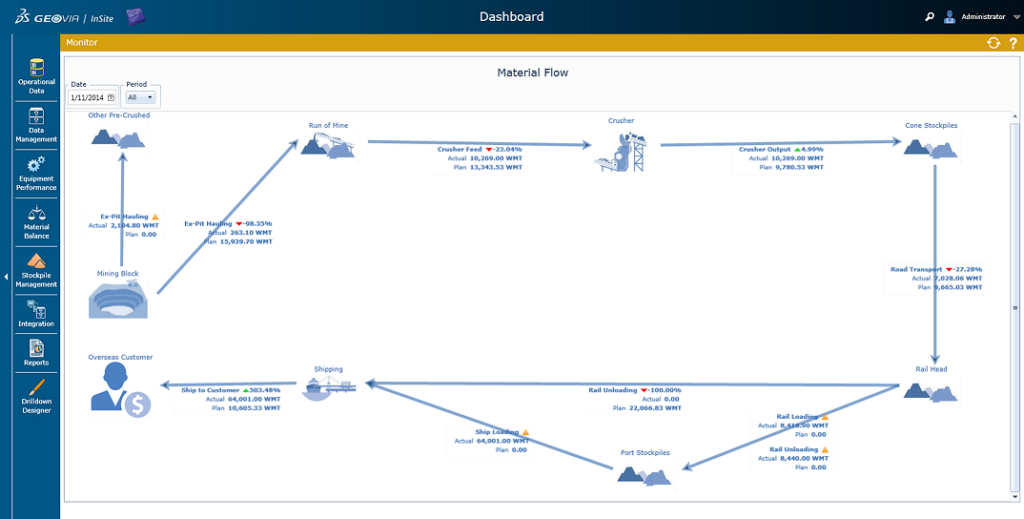