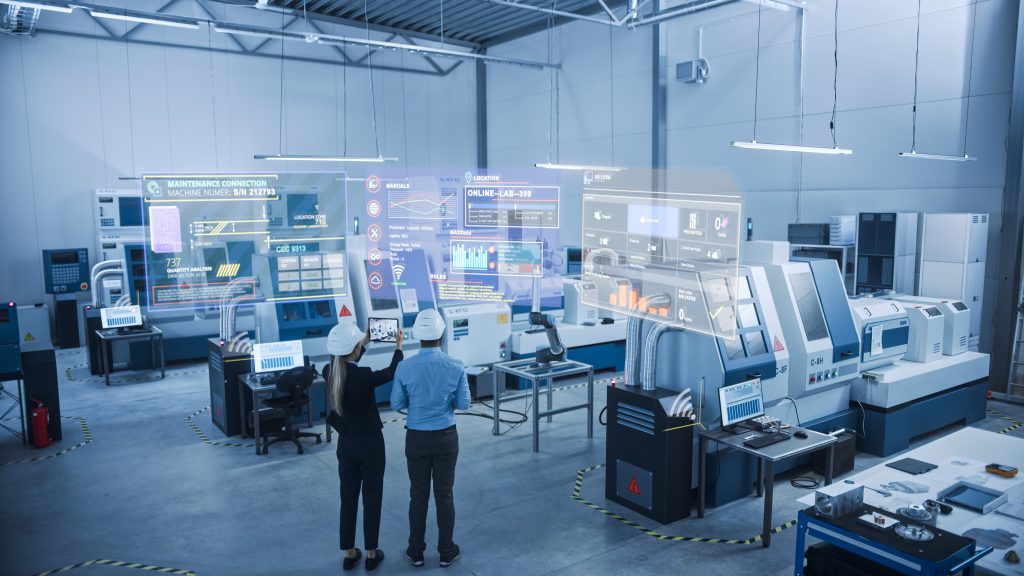
This blog is based on Dassault Systèmes’ partnership with IndustryWeek on conducting a midyear survey of industry leaders to gain a better understanding of how virtual twins in manufacturing are helping them adapt to these changes.
Today, change is the only constant, and success depends on the ability to adapt quickly and efficiently. The past year and a half saw manufacturers face unprecedented challenges resulting from global disruptions, to which they responded by repurposing or developing new product lines, reconfiguring their plants and restructuring their supply chains in order to meet changing demands and keep afloat amidst uncertainty.
The current manufacturing environment is ripe for virtual capabilities that help manufacturers visualize and test new ideas—including workflows, line changes and facility expansions—before they occur.
In an effort to understand the role virtual twins play in manufacturers’ current and future strategies, Dassault Systèmes via IndustryWeek conducted a midyear survey of industry leaders across a wide range of manufacturing sectors.
Featured below are excerpts of key findings and observations from the report:
Operational Challenges in The Face of Disruption
The lack of available workers is noted as the biggest challenge manufacturers face when it comes to retooling operations for new products or additional capacity to meet customer demands. Two-thirds of respondents reconfigured work cells or production lines in the past year for safety and social distancing reasons. Though more than 80% of respondents effectively restarted operations after the redesign, some smaller manufacturers struggled.
Survey respondents also reported a lack visibility and scenario-planning capabilities as top operational challenges in 2021. While many companies have implemented some level of IIoT connectivity, few have connected that data to their real-world operations. Here, modeling capabilities provide an avenue for manufacturers to respond to disruptions more effectively. For instance, modeling technologies can simulate how changes in labor or raw material availability impact operations.
Lean Improvement Initiatives to Overcome Production Hurdles
Manufacturers are doubling down on continuous-improvement efforts to rectify supply chain fragility. In fact, nearly half of respondents are set to place an increasing emphasis on lean manufacturing software due to pandemic-related events. Continuous improvement gives manufacturers an added layer of resiliency and the ability to respond quickly and more effectively to market fluctuations and unplanned events. Moving forward, technologies like 3D process validation are expected to be integrated into manufacturers’ continuous improvement initiatives to test and optimize new processes before they’re deployed. The wider adoption of visualization tools, such as VSM and 3D process validation, is anticipated in the coming years as one-third of respondents are looking to facility layout alternatives to increase flexibility in their operations.
The Need to Reimagine Supply Chain Strategies
Resiliency is becoming a key supply chain strategy, which will see more manufacturers rethinking location and supplier networks. This is where investment in modeling capabilities becomes even more important because the technology helps organizations visualize where they can add capacity to existing facilities before relocating operations.
Repurposing Product Lines to Accommodate Changing Demand
To repurpose a product line or make adjustments to meet new customer demands, manufacturers are considering feasibility studies, validation, plant capacity and cell layout/workflow designs. In this domain, virtual twins provide a competitive edge by helping manufacturers understand how these changes will impact their operations before they implement them. They will be able to evaluate how new inputs affect each aspect of their operations with the ability to model plant layouts and simulate workflows. This reduces the potential for bottlenecks, quality issues or late deliveries.
The Viability of Modeling and Simulation
Increasing investments in various modeling and simulation is expected over the next three years. However, the findings suggest manufacturers are missing the opportunity to leverage the full benefits of these technologies, highlighting budget constraints and limited existing infrastructure as hindrances to adoption. But challenges faced during the pandemic should promote faster adoption of technologies that help manufacturers conceptualize processes and interpret data more effectively, like virtualization and AI. In fact, 41% of large-size manufacturers have these capabilities compared with 28% of mid-sized companies and 19% of small companies.
Virtual Twins in Manufacturing
With the uptake of digital transformation and manufacturers having more real-time information than ever before, virtualization technologies, or virtual twins, will enable manufacturers to advance their Industry 4.0 goals of end-to-end visibility and flexible production.
Dassault Systèmes’ Virtual Twin Experience takes this one step further as a real-time 3D representation of your entire factory and value network, down to resources and processes. In conjunction with DELMIA solutions for modeling, simulation and optimization, manufacturers can not only reflect the physical assets but how they behave in the context of business processes for producing goods. These capabilities will help manufacturers understand the implication of strategic decisions—such as moving offshore production to an existing facility or adding a new production line.
For more findings and observations from the IndustryWeek/Dassault Systèmes survey and the role virtualization plays in manufacturers’ current and future strategies, read the full report here.