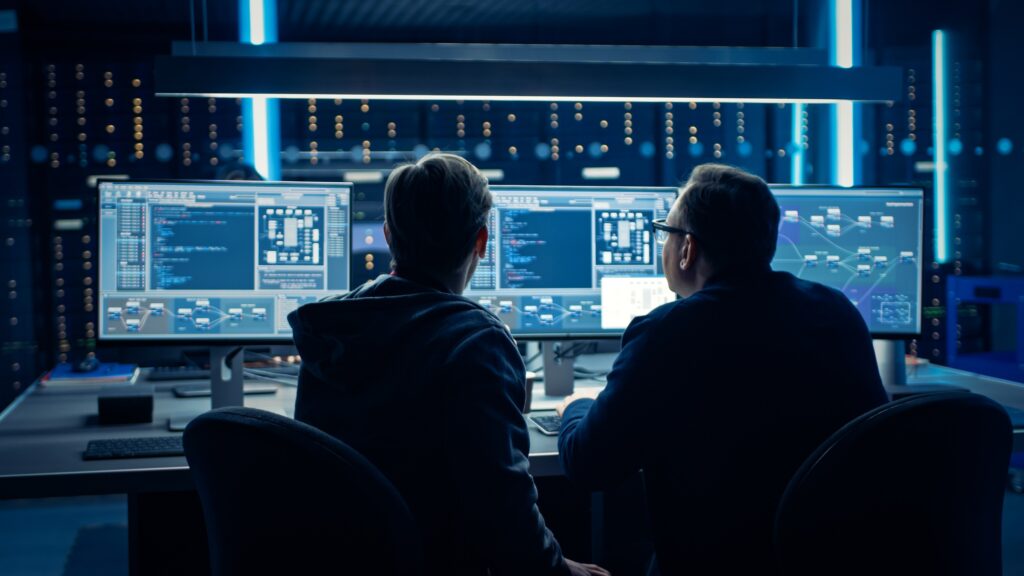
While the worst of Covid-19 seems to be over, manufacturers are still reeling from the after-effects of the disruptions caused by the pandemic. Enterprises are left to ask what’s next, and how do they prepare for potential road bumps in the journey ahead? According to McKinsey & Company, agility and flexibility will be critical to navigate the following challenges ahead.
Industry Trends for the Next Normal
Based on Dassault Systèmes’ data from 270,000 customers across 11 industries in 140 countries, plus the research conducted from several leading consulting groups, there are 4 key trends that we can expect to see in a post-pandemic “next normal” world.
1. Digital Transformation / Industry 4.0
Many organizations are moving towards digital technology adoption with functions for Big Data, advanced analytics in supply chain, human-machine Interfaces, and digital-to-physical transfers. Informed organizations are looking for technology that is flexible, scalable and secure. The main goals for these adoptions are to improve company operating performance and the performance delivered to the customer.
2. Sustainability
Most modern enterprises are aware of and looking to reduce the environmental footprint of their products and company in general. This could mean reducing fuel consumption, machine CO2 emissions, or transitioning their energy to hybrid, electric or hydrogen sources.
3. Supply Chain Instability
While the height of the pandemic may be over, Covid-related issues will continue past 2022. What organizations are currently experiencing is a supply chain “Bullwhip” effect that is affecting industries across the board. The next solution enterprises are looking for is to reinvent their supply chains to gain advantage beyond the next disruption.
4. Manufacturing Workforce Challenges
Aside from supply chain issues, we continue to see an ongoing talent shortage as well. Companies are facing the challenge of building employee retention as the demand for higher wages and the competition from other companies increase.
3 Critical Questions about the Virtual Twin Answered
With all of these challenges pressuring the current market, enterprises are looking for solutions through digital transformation and innovative technology in order to optimize operations and improve performance and delivery. DELMIA’s Virtual Twin Experience is one such solution, and in this blog we will address 3 key questions about this technology:
- What is “Virtual Twin” Technology? Digital Twin technology is a transformational technology that many companies are trying to implement today, however there have been significant challenges to this new technology. We define the Virtual Twin Experience as a scientifically accurate virtual model of objects that can be tested to analyze and optimize how they will behave under different scenarios using real-time or experimental data. Virtual Twin technology extends the Digital Twin – it is more connected, dynamic and reusable and is based on Model Based Systems Engineering.
- Where is it Useful? There are many areas or functions where the Virtual Twin Experience can provide value to your organization. Three of the most common are:
- Product – By creating digital models of products and the processes that create them organizations can efficiently define and validate process plans and virtual builds with the digital twin. This provides benefits of early determination of part assembly feasibility, development of digital work instructions, simulation of industrial ergonomics software to reduce or avoid worker injuries and reduced prototyping requirements which greatly reduces new product introduction costs.
- Resources – The Virtual Twin Experience supports a digital model of resources – from individual machines and equipment to full facilities. This can enable you to simulate and optimize physical space and line layouts, workshop operations, and robot operations. Using these virtual models for simulation provides significant benefits including early detection of layout problems, validation of the use of robots & tools in context, optimization of resource utilization, faster scale & ramp up, reduced time and cost for new product introduction, and many others.
- Supply Chain – By implementing digital twins, manufacturers can create end-to-end simulations of all aspects of the supply chain. This aspect of the Virtual Twin Experience provides optimized planning with mitigation of disruptions, modelling of the key operations that impact business goals, and improved agility to meet demand variations.
- Product – By creating digital models of products and the processes that create them organizations can efficiently define and validate process plans and virtual builds with the digital twin. This provides benefits of early determination of part assembly feasibility, development of digital work instructions, simulation of industrial ergonomics software to reduce or avoid worker injuries and reduced prototyping requirements which greatly reduces new product introduction costs.
3. How do I Use it? Here is the scope of solutions that DELMIA makes available to organizations with the Virtual Twin Experience, taking you from strategic to tactical operations:
- Resource Planning
- Manage a full plant layout in 3D
- Design for fluctuating production, changing capacity and worker safety
- Supply Chain Planning and Optimization software
- Analyze historic data and automatically adjust while searching
- Artificial intelligence to choose optimal solutions at all times
- Short-term Production Planning software
- Plan/validate manufacturing processes and workflows
- Simulate the process and flow of products
- Manufacturing & Operations
- Extend the digital thread to the shop floor
- Reduce waste, inventory & cycle times to improve productivity and quality
The Practical Requirements of Implementing Digital twin

In order to avoid the pitfalls that have impacted many companies trying to implement Digital Twins, we have identified 5 critical success factors in implementing the Virtual Twin Experience:
- Reasonable Scoping & Estimating
The first step is to determine the cost, benefit, and scope of the digital twin. DELMIA’s value engagement service offers expert help to analyze your current business and base needs, providing a cost-benefit analysis and full financial study.
- Clear Business Objectives
Have a list of goals you wish to accomplish and gain from the rollout of the virtual twin. This will provide realistic expectations for its capabilities and act as a guide for next steps.
- Understanding Of Required Data & Supporting Systems
It is critical to know what data you need to support your digital twin and where that data is going to come from.
- Platform vs. Point Solutions
New start-ups and plants usually choose a single representative or leader for a particular system, which ends up in a lot of point solutions. The initial rollout may be quicker, but it is not a sustainable model. Each point has to communicate and work with each other beyond initial integration. When upgrades happen, the systems may also be incompatible. The difference with a platform solution is that it allows for collaboration, and it is both sustainable and scalable.
- Internal Collaboration & Executive Support
Since MRP2, the precursor to manufacturing ERP software, DELMIA Strategic Business Development Director Mike Bradford has seen that two of the key success factors for rolling out a new system are having a broad collaborative team and executive support.
Customer Case Study
Kobelco is a global industrial equipment company with multiple facilities manufacturing heavy mobile equipment. The company includes approximately 7,000 employees with manufacturing bases in Japan, China, Thailand, India and the United States, and they are currently developing business worldwide with hydraulic excavators and crawler cranes as their main products.
In Kobelco’s business environment, it is important to respond quickly to rapid changes. They consider smart factory on the 3DEXPERIENCE platform as part of this effort. Kobelco started process planning and 3D simulation in 2010, promoting the use of DELMIA to reduce the rework in product development.
With DELMIA, Kobelco has been able to achieve the following:
- Collect necessary performance information from manufacturing sites with a system that is automatic and perpetual.
- Reduce 50% of back-office staff operations by setting up an optimal operation process.
- Carry out simulations with 3DEXPERIENCE to evaluate the production lines’ adequacy and productivity in parallel with design work.
- Reduce rework with virtual assembly verification and achieve a 60% reduction of design changes during mass production.
- Cut product development lead time in half.
By accumulating these accomplishments, Kobelco hopes to serve as a source of best practices to others in the manufacturing industry with similar challenges and aspirations.
How to Start Your Virtual Twin Experience Journey
The answer is to start at any stage. It is your digital acceleration journey, so you determine where to begin. For example, some of DELMIA’s customers already have an effective manufacturing operations management solution, but they want to move forward with model-based enterprising and begin virtualizing their process planning. Other customers utilize DELMIA for planning and optimization and then choose to implement the digital twin in manufacturing operations. Still others start with model-based enterprising and managing all their engineering digitally, then choose to move the process down to the shop floor.
So you can start using the virtual twin for any aspect of your business – the key is to start! Do an evaluation, find the area you can gain the most value, and start there.
For more details about the Virtual Twin Experience and how it can transform your business operations and processes, please view our webinar “Driving Manufacturing Innovation with the Virtual Twin Experience”.