The widespread supply chain disruptions that happened when the global pandemic hit in 2020 highlighted several important lessons regarding manufacturing and supply chain visibility. Companies that lacked a manufacturing control tower software in supply chain, manufacturing and operations found themselves in a pickle. They were unable to ascertain the full impact of the disruptions they were facing. As a result, these companies could not react in a timely manner, leading to significant losses.
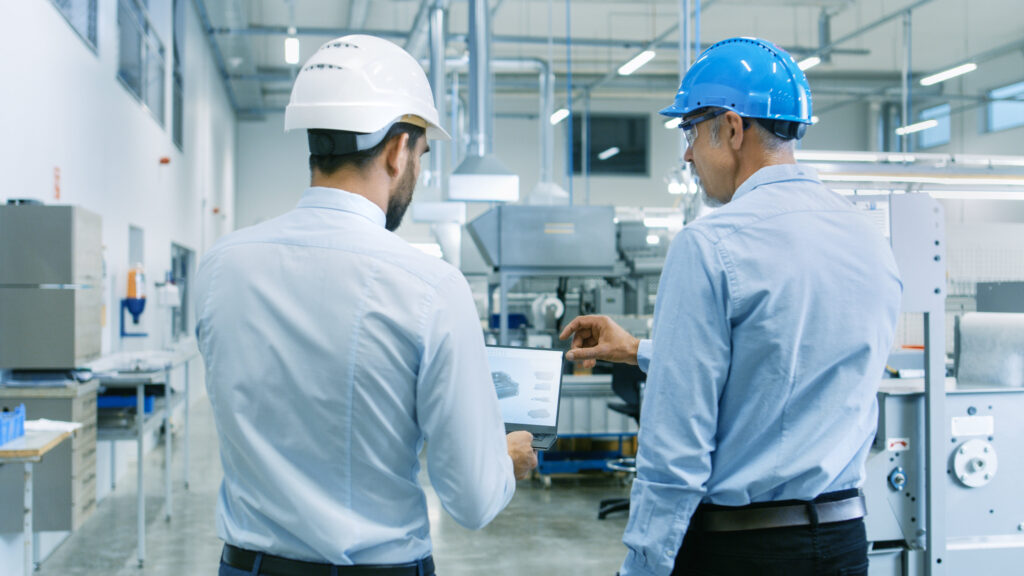
Imagine driving a car in a new city with a flawed navigation app. It can show you your destination but cannot show you the way there. The app also cannot pinpoint your present location—giving vague and significantly delayed information at best. There’s no information on your estimated time of arrival, traffic conditions or even blocked roads. In such conditions, you would be lucky to reach your destination without delays or even reach it at all. This is what it’s like for manufacturers with siloed operations that lack visibility—especially in industries with more complex products such as Industrial Equipment.
Manufacturers who find themselves with daily questions on their own operational performance have an opportunity to create significant value with a manufacturing control tower (MCT). The MCT provides centralized data management capabilities with near-real-time visibility in a unified view of the current conditions in factories and operations. This empowers stakeholders with manufacturing intelligence and the ability to collaborate effectively in a timely manner so that they can make optimal decisions in all manufacturing operations.
Why Industrial Equipment needs Manufacturing Control Tower
With MCT, Industrial Equipment manufacturers have a consolidated view of everything that happens in manufacturing and operations, from historical data to present data and future plans. Its cross-functionality enables it to serve as the central link between plants, warehouse, distribution and customers.
MCT connects all stakeholders for timely and more effective communication, and supplying real-time data and metrics enables data analysis for manufacturing and operations, empowering teams to make critical decisions faster and more accurately.
This leads to benefits such as:
- Decreased mean time to acknowledge (MTTA)
- Reduced costs from poor quality through better root cause analysis
- Operational cost savings from improved visibility and control
- Minimal disruptions from visibility into the impact of operational issues
- Improved material flow and equipment efficiency
- Cost savings from more efficient inventory management
- Improved throughput, leading to increased manufacturing capacity
Compounding value of MCT in an integrated solution
Industrial Equipment manufacturers can create even greater value from their MCT when used with DELMIA solutions. Powered by the 3DEXPERIENCE platform, DELMIA takes a model-based, data-driven approach by connecting the virtual and real worlds of manufacturing and operations.
Leveraging virtual twin technology with MCT creates a comprehensive experience that greatly improves operational visibility and control. The use of IIoT in manufacturing here is critical to enriching the 3D context of the Virtual Twin Experience for significantly improved visualization. With MCT, DELMIA enables root cause analysis by detecting and triggering corrective actions, empowering manufacturers to effectively mitigate the impact of disruptive events.
MCT within DELMIA covers three important functions in manufacturing and operations:
Supervise operations: Monitor assets and operations in near-real-time through the MCT and use alerts and events to anticipate disruptions.
Identify and investigate issues: Investigate disruptions through the 3D virtual world by replaying past events in the context of real-world data to identify issues.
Dispatch decisions: Trigger workflow activities to quickly resolve issues in areas such as maintenance, safety, quality, materials, planning and scheduling.
MCT is fully integrated with all other DELMIA solutions, including DELMIA Augmented Experience, powered by Diota. This unique solution leverages augmented reality (AR) technology to enhance complex assembly operations and augmented reality quality inspection software activities by creating digital overlays to help field operators compare products and parts in the real world with their virtual twin models. With full MCT integration, team leaders can have more detailed visibility than ever on what happens on the shop floor so that they can ensure that everything is executed according to plan.
Discover how DELMIA with manufacturing control tower can be configured according to your company’s business needs—driving more effective planning, unparalleled optimization and improved reactivity so you can create a competitive advantage with your future-ready virtual factory software. To learn more, download the whitepaper Centralizing Control of Manufacturing Operations in Industrial Equipment.
Watch the video: