The containment problem
The “containment problem” stands as a pervasive challenge that has been a thorn in many a manufacturer’s side for decades. A 2015 report from the National Highway Traffic Safety Administration (NHTSA) reveals that since the implementation of the National Traffic and Motor Safety Act in 1966, a staggering 390 million vehicles have been subject to recalls; including 46 million tires, 66 million pieces of motor vehicle equipment, and 42 million child safety seats. Astonishingly, the figures are immense when contrasted against the backdrop of North American vehicle sales in 2022, totaling about 13.75 million units. A disconcerting reality emerges as 932 safety recalls, impacting 30.8 million vehicles, unfolded in the same year. It becomes strikingly evident that, for the better part of the last three decades, the number of vehicles affected by recalls has consistently surpassed the total number of vehicles sold in North America.
The relationship between quality and containment
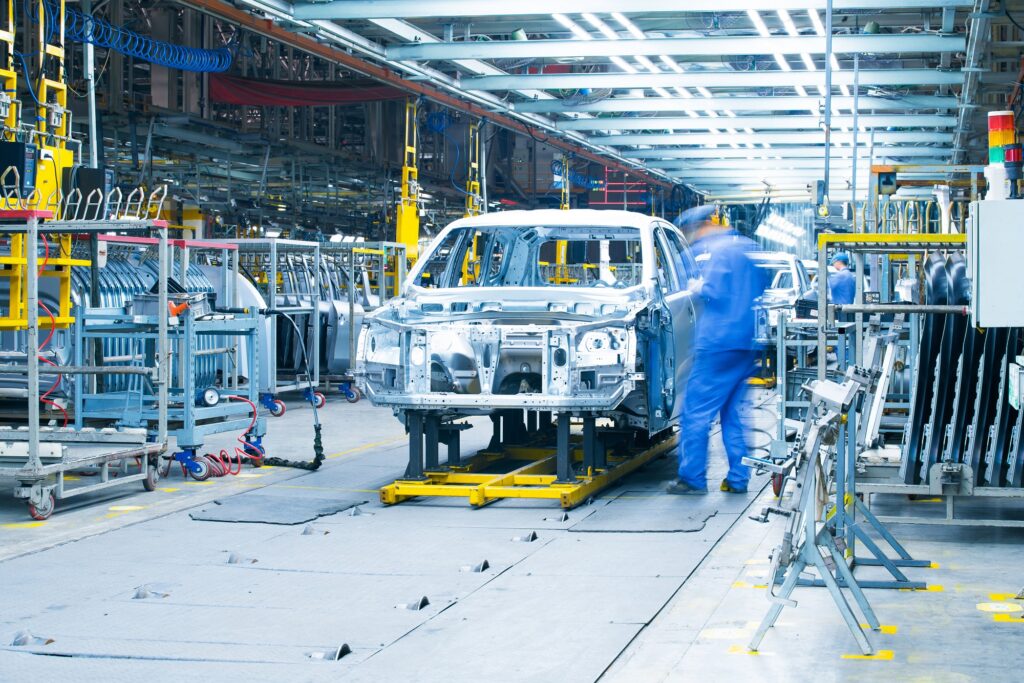
Quality and containment go together as two sides of the same coin. Quality, as a proactive process, seeks to prevent non-conformance through a repertoire of tools such as inspection, sampling, quality tests, and Statistical Process Control (SPC). Improving quality is a daily endeavor that requires the diligence of line workers alongside a comprehensive incorporation of preventive measures. The ethos of quality not only upholds standards but is the bedrock upon which improvements are built, ultimately leading to enhanced product quality and a reduction in associated costs.
On the flip side, containment emerges as quality’s responsive counterpart, stepping in when non-conformance manages to elude the preventive measures put in place by the quality protocols. Containment deals with the unpredictable or unknown root causes of issues, typically surfacing as rare events that demand the attention of quality managers and engineers. It functions as a strategic safety net, helping to identify new preventive measures while simultaneously mitigating risks associated with unforeseen deviations.
In this delicate interplay between quality and containment, a symbiotic relationship forms—one that is essential for maintaining the integrity of the production process as well as ensuring that products meet or exceed the expected standards of excellence.
Promote excellence with a containment manager
Containment management software, such as DELMIA Apriso Containment Manager, helps manufacturers navigate the intricate landscape of quality management, offering top-level benefits that bring value across the entire production and customer satisfaction spectrum. The key benefits of a containment manager include increasing customer satisfaction, greater risk mitigation, as well as maintaining brand integrity.
Operational efficiency is a key contribution of a containment manager. By consolidating data from disparate systems into a single source of truth, they significantly reduce search times, alleviating labor time and effort. Furthermore, the implementation of multiple search criteria minimizes the occurrence of outliers and reduces the labor-intensive processes required to inspect and rectify product issues. Moreover, a containment manager introduces automated processes to swiftly and effectively hold suspect items, ensuring that only products that meet the stringent quality standards upheld by the manufacturer make their way to the market.
Even beyond the production floor, the containment manager plays a pivotal role in maintaining production plans within the manufacturing network. Quick and effective containment measures are instrumental in minimizing disruptions, enhancing overall production efficiency, and meeting delivery timelines. This proactive approach not only bolsters immediate operational goals but also contributes to long-term financial health by reducing warranty costs over time. The downstream impact extends to the financial realm, where improved containment practices reduce the need for a “warranty hold-back” amount on the balance sheet.
An automotive supplier success story
Facing the complex challenge of unifying quality, traceability, and containment processes across 32 global plants, a major Tier 1 automotive supplier orchestrated a remarkable transformation by standardizing with DELMIA Apriso as their singular, global system for Quality, Traceability, and Containment. The rollout, executed with precision over 42 months, required full traceability and containment capabilities to support common processes. The payoff was significant, with one plant realizing a 19-day payback. How did they accomplish this?
Central to this success story was DELMIA Apriso’s ability to automate the search process. The implementation of Interlocking Traceability with Containment revolutionized data accessibility, enabling automated searches from a single, centralized data source instead of navigating through multiple systems and manual records. The results speak for themselves—a huge reduction in search time from over 60 hours to a mere 3-4 hours, realizing a 90% or more reduction in labor and time expenditures.
DELMIA Apriso Containment’s prowess extended beyond automation to strategically narrow down the ‘book-ends’ – the number of parts requiring inspection and validation. The sophisticated search and filtering capabilities drastically reduced the number of parts requiring attention from several thousand to a few hundred—a remarkable 90% reduction. This precision not only streamlined processes but also significantly diminished the likelihood of oversight, ensuring that attention was focused where it was needed most.
The culmination of these improvements manifested in tangible savings of over $1 million on a single quality spill.
“(DELMIA Apriso) Containment Manager easily allows us to identify and quarantine an engine or parts by multiple criteria, such as operation time, operator, work center, child, or parent parts. Out-of-spec work-in-process can now be held and not shipped to our customers, helping to improve customer satisfaction.”
Project Manager, major automotive supplier
Solve the containment problem with DELMIA
In short, a containment manager can be a pivotal component in ensuring seamless and resilient operations across the entire supply chain. By helping manufacturers navigate the intricacies of risk mitigation and containment activities, DELMIA Apriso Containment Manager preserves both operational integrity and brand reputation. The multifaceted impact extends beyond the shop floor by significantly reducing costs. By integrating prevention with risk mitigation, DELMIA Apriso Containment Manager not only safeguards against unforeseen deviations but actively contributes to increased customer satisfaction.
Containment process
Learn more about a containment manager that helps make these benefits a reality in your organization today. Download the DELMIA Apriso Containment Manager datasheet.