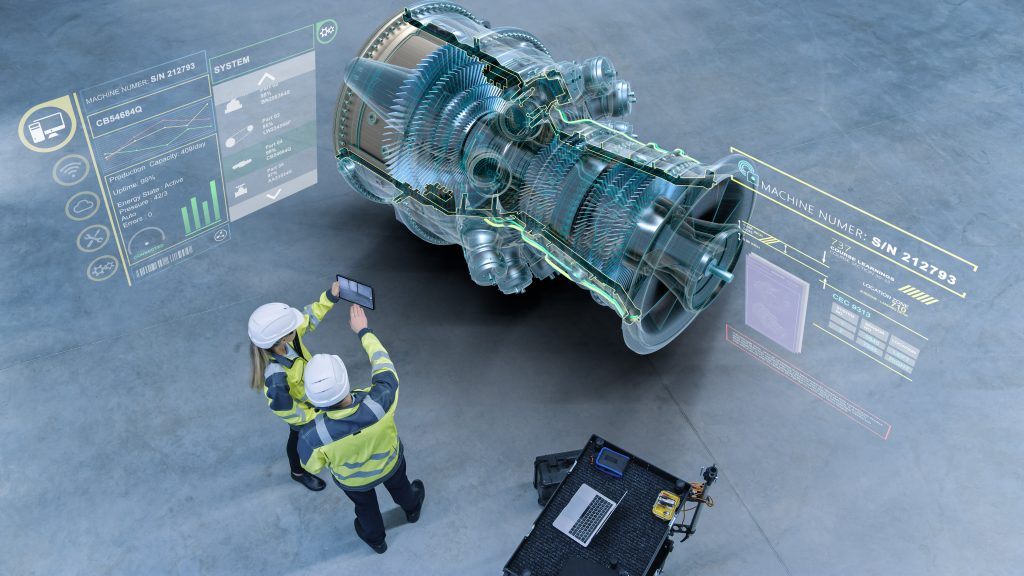
The aerospace and defense (A&D) industry is facing numerous challenges following the recent pandemic, dealing with constrained demand and vulnerable supply chains. The scale of the disruptions’ impact have forced companies to reexamine their existing operations and decision-making processes, especially in operations and manufacturing.
There are early signs of a return of commercial demand in the next 12 months and companies around the world now have an opportunity to engage in digital transformation that helps them prepare for the new normal. For aerospace and defense manufacturers it is now a chance to restructure and implement new capabilities that will help them be more efficient once production ramps up. Digital twin technology is one of the key capabilities that will provide a foundation for future success.
The adoption of digital renderings of component parts, assemblies and resources has typically been ad hoc. Design, manufacturing production and management software, short-term production planning scheduling software and MRO (Maintenance, Repair and Overhaul) software frequently operate as independent “silos” within the organization. But what if this data could be connected and leveraged to allow model-based engineering and create process simulation of actual production operations? The potential for new insight into sustainable business is obvious.
DELMIA enables companies to realize these goals through the Virtual Twin Experience . The Virtual Twin Experience, an executable virtual model of a physical system, brings in learning and experiences taken from REAL world processes to update the digital model. As an accurate representation of working conditions. Manufacturers can also set KPIs to measure performance in real time and adjust operations accordingly in a continuous closed loop process. That uses real-time data, it allows manufacturers to assess changes virtually, before implementing them in the real world.
Advantages in Time of Disruptions
The “next normal” that A&D manufacturers face due to modern disruptions has amplified certain challenges that threaten the longevity of businesses. To address the urgent need for greater resilience, manufacturers can leverage the Virtual Twin Experience to improve workforce automation , which helps employees multitask and cover skill gaps.
Furthermore, optimization can make operations and supply chains resilient to disruption from resource and material constraints. Supply chain resiliency gives companies options to optimize in economically difficult situations. The Virtual Twin also helps aerospace and defense manufacturers be more agile and flexible by simulating changeovers ahead of time and identifying the quickest and most cost-efficient way to do so, minimizing downtime.
Let’s now look at some of the capabilities that A&D manufacturers can leverage using the Virtual Twin Experience:
Plant Line Layout
By creating a digital twin of the plant or assembly line, manufacturers can manipulate and evaluate the placement of infrastructure and resources within a 3D workspace. This allows them to define and validate the layout of their facilities without needing to step inside.
Assembly Process Engineering software and Virtual Build
Simulation creates the flexibility and agility needed to work towards continuous improvement in manufacturing. Manufacturers can improve their efficiency in long-term manufacturing planning software through product build-up visualization and assembly plan validation before having to build physical prototypes.
Digital Execution
Connecting the virtual and real worlds allows manufacturer to unify engineering and manufacturing change management and deploy standard work-processes across all sites, to achieve disciplined production execution.
Benefits of Digital Twins in Aerospace Industry
Leveraging the Virtual Twin Experience can bring A&D manufacturers significant benefits:
- Reduce waste and error to deliver first time quality
- Support rate on demand with lean operations
- Minimize risks and save money by avoiding unexpected failures
- Reach and monitor tactical business & financial objectives
Learn more about how the Virtual Twin Experience provides a competitive advantage to aerospace and defense manufacturing by watching our on-demand webinar here.