The battery cell manufacturing landscape is at the cornerstone of electrification transformation. The demand of battery cell is growing up with more than 30% year-on-year, exceeding 4,000 gigawatt hours (GWh) in the next decade.
To remain competitive and cope with unprecedented demand, manufacturers must drive innovation to maximize battery cell capacity and production.
Best-in-class manufacturers have already started investing in integrated solutions such as DELMIA Manufacturing Operations Management (MOM) software to transform their operations and overcome legacy disparate and siloed system challenges. It has helped them address the following critical considerations:
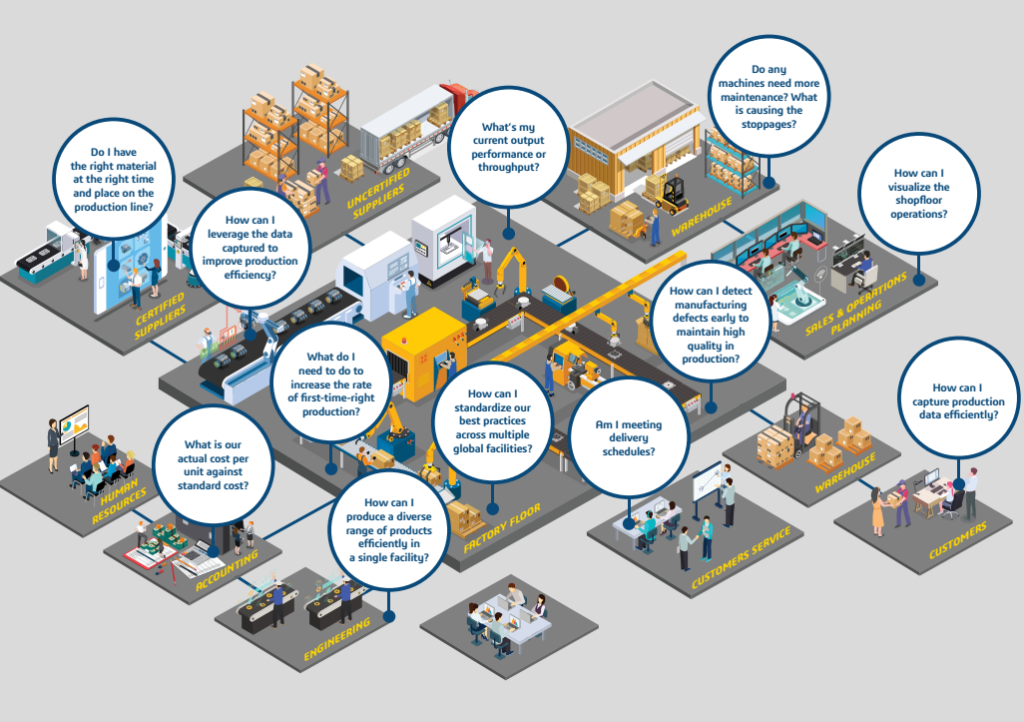
Why Manufacturing Operations Management (MOM) Matters
The urgency for digital transformation is at an all-time high for Battery Cell manufacturers. Starting with a MOM implementation can prove to be a low-risk, high-value entry point to digitalizing the shop floor.
MOM involves automating, executing and managing the performance of all business processes pertaining to manufacturing execution. It paves the way for a unified, flexible, scalable and secure digital transformation by providing manufacturers critical real-time data to improve decision-making.
Why Quality Management is Critical for Battery Cell Manufacturers?
While quality assurances are important across industries, defects in battery cells can pose a major safety hazard. Coupling this with the continuously evolving regulations related to safety and quality of products and production, manufacturers allocate a significant share from their budgets to manufacturing quality control software.
Failure to comply to these standards can result in even more expensive fines and product recalls down the line.
How MOM Can Help Manufacturers Drives Quality Costs Down?
With real-time data available at their fingertips, manufacturers using MOM solutions have full visibility and control across all phases of manufacturing operations. They are able to manage quality processes and measure product characteristics against specifications.
In addition, MOM tools enhance genealogy, traceability and containment. This means in the case of defects, they are identified quickly and are contained as early as possible, before a massive product recall.
These capabilities greatly reduce the risk of potential non-conformances and help Battery Cell manufacturers save up to 30% in production costs from scrap, yield and inventory improvements.
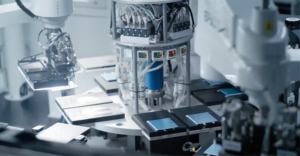
The Last Mile: Establishing a Center of Excellence (CoE) Team
Now that you have unlocked better quality management with MOM, establishing a Center of Excellence (CoE) team is a must to help you expand this excellence on a global scale.
The CoE team can help you achieve this by:
- Standardizing your business processes and how they are addressed by your IT tools
- Capitalizing and sharing best practices coming from various parts of your organization
- Providing improvement and evolution of solutions to the entire ecosystem of your plants
The time has come for manufacturers to move away from legacy systems and traditional plants that have been set up to produce high volumes in a linear way. Manufacturers today need to leverage digital transformation to build agile, flexible and sustainable operations.
To learn how to transform your shop floor to ensure resiliency and business continuity, download our eBook on Unlocking Innovation on Battery Cell Manufacturing.