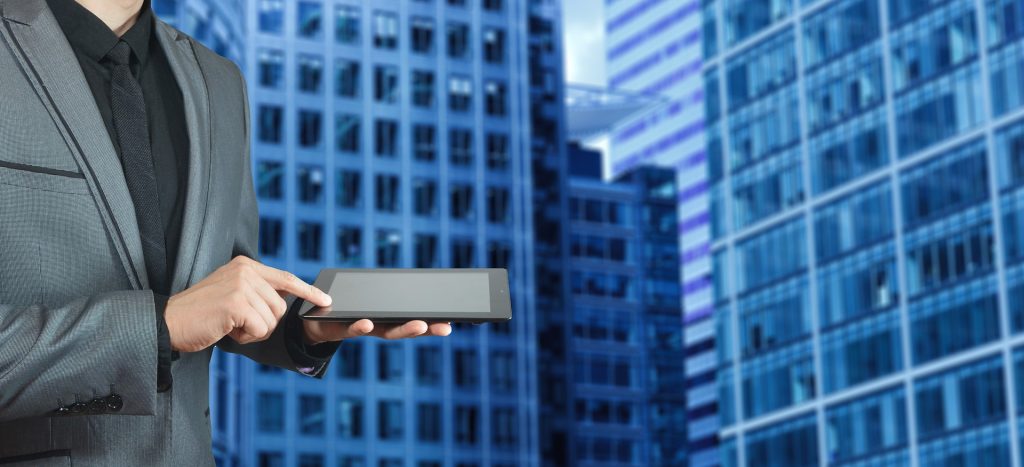
Unlike more traditional industries, High Tech represents the opposite spectrum of innovation and rate of new product introductions. This drives rapid changes to products that have desperately short lead times and life-cycles. The initial design process can be completed virtually, but at some point the product has to become a reality. Determining manufacturability is an important step. Can this still be accomplished despite teams and staff being physically separated due to COVID-19?
Digital product design is a mature process, but there is a “digital divide” between design and production. Manufacturing often relies upon physical prototypes and lots of disparate data used by assembly planners and manufacturing engineers to determine how best to create or incorporate new products. Development of new work instructions also requires a lot of manual effort and distribution of material. Given social distancing and stay-at-home requirements, this process has become even more of a challenge. Dassault Systèmes helps bridge the gap by providing the 3DEXPERIENCE Virtual Twin capability.

The impact of being able to collaborate between Design, Digital Manufacturing and Operations in a virtual environment has never been more beneficial.
The entire workflow can be supported digitally:
- Accessing design data to develop the manufacturing service BOM software
- Determining optimal process plans including resources, operators & tools
- Validating production and assembly against a virtual facility layout
- Development of online work instructions
- Digital rollout and management of process changes
Leveraging 3D visualization and powerful optimization enables High Tech companies to build products virtually and address the “what”, “where” and “how” they will be manufactured. The collaborative nature of the 3DEXPERIENCE platform means that all stakeholders can participate concurrently, and from the convenience (and safety) of their own login location.
The value of having a single data model that can support efficient management of design changes and deliver accurate and validated process plans is significant. Elimination of physical prototypes is just the start. Companies typically see 10-30% reductions in production cost and time-to-market as well as double digit improvements in production throughput. All of which are key benefits in this age of hyper competition and required to meet consumer demands. For the High Tech industry, the need to adapt during times of crisis is critical. Maintaining business continuity despite unique workforce constraints requires innovation at the process level. To understand how DELMIA can help enable this innovation, please connect with us or learn more about our Digital Manufacturing solutions.