
Injection molding is one of the most prolific manufacturing techniques in the world — but it’s not without potential frustrations. One of these is the time and precision required to ensure your machines, molds and build materials are interacting with one another the way they’re supposed to.
To accomplish this, an injection molding company must use either their machines’ built-in quality controls or take the next step up to either a pressure-based system or a vision-based one. For several reasons, “machine vision” is becoming the new favorite when it comes to performing inspections and calibrations of your production equipment and ensuring a steady flow of high-quality parts. Here’s what you should know.
Existing Injection Molding Methods
Injection molding specialists are likely already familiar with some of the existing mold protection techniques and products — as well as their importance in manufacturing quality control software and staying solvent in a competitive industry. Until this point, manufacturers typically relied on low-pressure clamps and clamp settings, pressure sensors or non-contact sensors to detect workpieces in the mold and ensure their successful release.
You may have seen demonstrations where machine operators placed extremely delicate items between the two halves of a mold. With the correct sensors and pressure settings, the mold should reverse itself automatically as it makes contact with the object, without damaging it.
These demonstrations are always a good piece of theater, but the realities of operating this type of equipment compromise its effectiveness:
- As molding machines operate, its complex components change temperature repeatedly, which can introduce changes to these delicate settings.
- Over time, even the lowest low-pressure mold close settings might result in short-shot parts and other damage to workpieces.
- Relying on pressure-based mold protection means workers spend more time monitoring and adjusting machine parameters than performing valuable work.
These combined shortcomings mean workers tend to waste valuable time and effort optimizing their machines, and that castoff parts and wasted materials are more likely.
This lack of consistency and precision to our injection molding workflows will likely bring harm to the molding machine itself. Poorly optimized pressure settings require force for the tooling to stop its movement. Even a small amount of unnecessary force could damage the machine and the mold, especially if the mold has delicate features or details. Finally, even your cycle times are likely to feel the pinch, since pressure-based systems rely on a slower closing speed for the mold.
As far as using sensors for mold protection goes, there’s a different set of complications entirely. If you deal with simple designs and tools, you’ll usually choose molds with fewer cavities. The more cavities, the more sensors the project requires — and each one needs individual adjustments. For anything but the most straightforward runs of simple parts, this is not an effective technique either, from a time or financial perspective.
What is Machine Vision?
For any company operating with lean principles in mind — which is most — or those that are particularly sensitive to time constraints and deadlines, it makes sense to look for a better way. Machine vision — or vision mold protection — is a relatively unheralded technique for protecting injection molds, as well as the workpieces within.
Machine vision uses one or more cameras, instead of many sensors, to take images of parts and molds alike throughout the entire work cycle. The result is greater accuracy than what a typical 2D inspection system can achieve. It’s also applicable to virtually any molding operation. In a nutshell, here’s what it offers:
- It tells machine operators whether or not parts are present in the molds, in addition to whether cores, slides and ejectors are properly placed, and that double inserts have not been placed.
- The operator can tell at a glance whether parts are stuck in one side of the mold, both or neither.
- Software accompanying the camera(s), plus the selective application of light, can detect faults and errors and automatically pause the cycle until a machinist can respond.
- The application of light and photography continues until the machine and mold apparatus are aligned properly, present and accounted for.
Any injection molding specialist will tell you a short shot can be a time-consuming mistake that results in employee re-work to ensure the mold gets filled the next time around. Machine vision for molding takes care of this problem, first by preventing damage to your machine that might compromise its ability to fill molds, and second, by offering a more appropriate and consistent speed and pressure for the manufactured part.
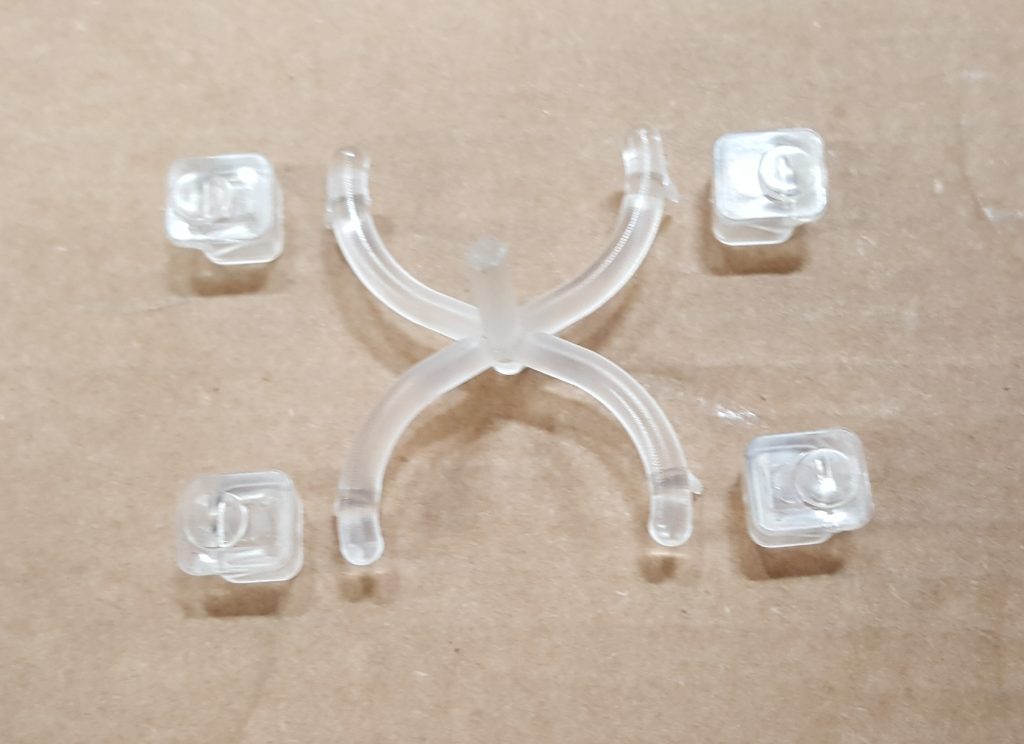
Some parts are too convoluted or complex to facilitate the smooth filling of the mold, and situations like this might call for a redesign. But for most machine shop needs, short-shot parts will likely become a far less frequent occurrence after the transition to a vision-based molding machine inspection system.
Vision mold protection has historically been cost-prohibitive for all but the most established molding companies. But that’s not the case any longer, with many manufacturers of such systems boasting they can now pay themselves, through higher productivity and less waste, in a matter of months or even weeks.
Who Can Use Machine Vision-Based Mold Protection Systems?
Molding machine operators and company decision-makers will be pleased to know there are very few applications in which vision mold protection will not work with your existing equipment. If any of the following apply to you, you can almost certainly bring machine vision to your shop:
- You work with horizontal or vertical machines, or both.
- You perform die-casting, metal injection molding or micro-molding.
- Your company engages in foam molding at low pressures or uses molds with multiple cavities.
Versatility and flexibility are the primary advantages of a machine vision system over incumbent methods of mold protection. Even so, some of the most widely touted specific applications include the manufacture of electrical connectors, parts with delicate features such as pins and any other molding process where the workpiece contains a high number of cavities.
Are There Any Downsides to Machine Vision?
There’s a good chance you’re familiar with the benefits of applying various coatings to mixing and molding equipment — to extend the longevity of your equipment and to ensure a more consistent final product. Depending on the work you do, this could complement, rather than replace, the addition of a machine vision system. Both have their place.
Many see vision-based systems as the future of the industry, however. You’ll have a choice of multiple vision-based mold protection systems, but not all of them will offer the same ease of use. There are some one-size-fits-all machine vision systems you can incorporate and set up as you would any other piece of aftermarket hardware. But these sometimes come with steep learning curves.
Whenever you can, see a demo of any system you’re looking at. Get a sense of the intuitiveness of its user interface and ask the company offering it whether they designed it for use by machinists of all skill levels, or whether professional-caliber setup and calibration is necessary. Again, you’re likely to find multiple providers looking to meet various skill sets and industrial requirements. More than anything, don’t feel pressured to adopt a system you don’t feel comfortable with, or that doesn’t quite suit the work you do or the pace at which you do it.
Continue the conversation in the DELMIA Fabrication Community on SwYm. Membership is free.