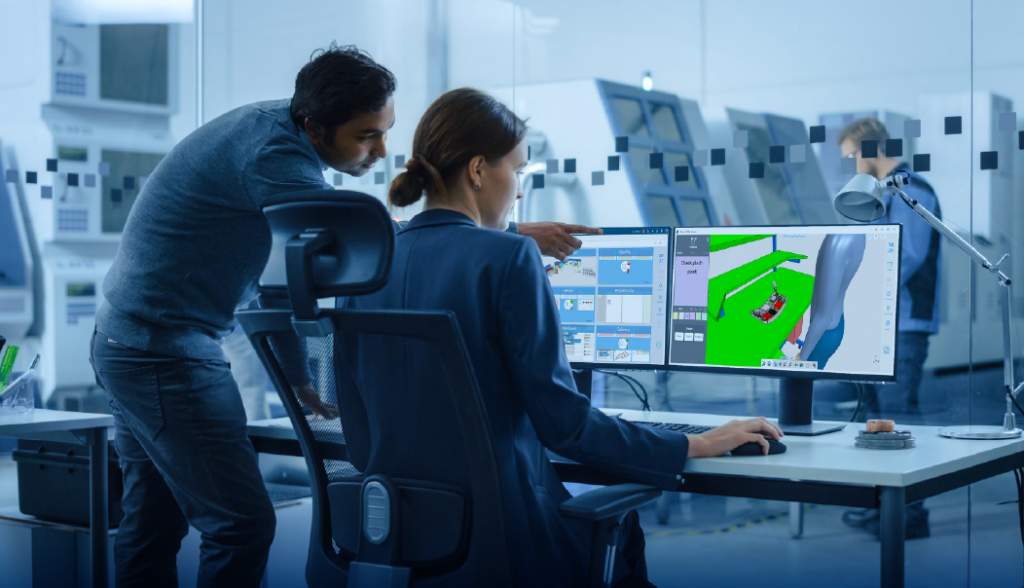
In an effort to enhance production capabilities to keep pace with the High-Tech manufacturing market demands for rapid product innovation and customized, short-run production, manufacturers are quick to adopt transformational changes and new digital solutions. However, manufacturers should not forget that their transformational changes should not only focus on new technology, but also their most important resource—their operational teams.
It is often the case in many companies that poor overall productivity can be the result of miscommunication, lack of focus on key objectives and poor engagement from team members, leading to time wasted on getting their teams back on track. Traditional team interactions are not always truly collaborative, which can harm collaboration, problem solving and follow-ups, leading to many missed opportunities.
In order for High-Tech companies to transform their teams to be truly efficient and drive operational excellence in manufacturing, there are some key challenges that must be addressed first.
Challenges of High-Tech Manufacturing Teams
One problem that many companies face, both in and out of the High-Tech industry, is that different teams often operate in silos. High-Tech companies need to break down these organizational silos as multiple departments are involved in making any new product a success. While product designers focus on designs that align with modern trends, field operations can provide valuable customer feedback on product features that are highly sought after, while engineering and operational teams can provide input on product designs that can be produced efficiently.
With so much going on in any manufacturing process, manufacturing and operational teams often need the latest updates to get up to speed on what’s going on in production. This isn’t feasible with paper-based tracking, where updates can be difficult to maintain and are often outdated. This is where teams can benefit from easy access to a digital platform that allows them to share updates on even more complex information such as 3D product information.
Lastly, because High-Tech companies are often structured as highly outsourced and distributed supply chains, the physical distance can make it challenging for stakeholders in different parts of the supply chain to collaborate effectively. Now that the shift in global trends has displaced even internal teams, it has become more urgent than ever for companies to adopt digital solutions that can enable seamless remote collaboration.
Enable Effective Collaboration in Operational Teams
All these challenges point towards digital solutions that enable teams to collaborate in a structured and effective manner regardless of physical or organizational distance. This also requires providing teams with enhanced visibility over supply chain operations and the capability to respond to changes and updates with agility.
DELMIA believes in leveraging Lean principles to connect the dots between people, ideas and data through DELMIA 3DLean, powered by the 3DEXPERIENCE platform. High-Tech teams will be able to take their collaborations one step further by leveraging 3D virtual worlds to model and optimize resources and work processes in order to enable flawless real-world execution. 3DLean also serves as a robust platform that captures, monitors and tracks operational meetings and problem solving so that teams are always kept up to date on relevant and key information from all areas of operations.
- Engage teams by adopting a modern, interactive environment on the cloud
- Enable teams to formalize issue management using rich content and problem-solving structures
- Capitalize on company knowledge by leveraging virtual models, processes and resources to develop plans for improvement
- Convert Lean principles into actions to address operational waste, variability and efficiency
- Guide team collaboration and manage actions