Big data can be a huge contributor to great supply chain planning and optimization, but it doesn’t translate to actual value unless you know what to do with it. To bridge the gap between big data and optimized planning decisions, companies are now turning to big calculations. Big calculations unlock the value of big data, resulting in real-time optimization aimed at achieving fast and efficient business results.
Last year, we presented the concept of big calculations at the first INTE-TRANSIT International Conference in Valencia, Spain. The conference provided container port operators with valuable insights on how strategic planning and modern logistics frameworks can enhance their competitiveness. In preparation for the conference, we created a special slide showing the planning decisions taken by container terminal planners on a daily basis.
Two things became obvious during this preparation. First, as the overwhelming number of lines show, container yard planning on its own is a very complex puzzle. Second, the yard – where all containers are stacked – is in between the waterside (where vessels arrive, get loaded and unloaded, and so on) and the landside of a terminal (where trucks and trains transport the containers farther in-land).
As you can see, the planning decisions taken for the container yard will impact all other operations at the terminal. So, how can big calculations ensure that yard capacity is planned optimally and that it will boost the performance in other parts of the terminal as well?
If you had the chance to see our keynote presentation at the Gartner Supply Chain Executive Conference in Arizona, you know that big calculations are implemented in 5 steps.
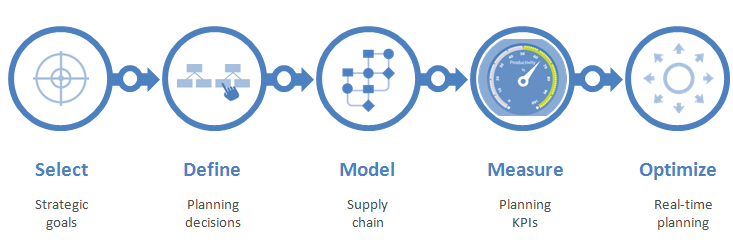
5 steps to deliver calculated decisions and BIG value
Step 1: Select strategic goals
Be clear about what you would like to improve. The ultimate question here is: What are the overall KPIs that will drive container terminal performance? The high-level goals of every container yard operation are to:
- Maximize efficiency and reduce congestion in the yard by aligning loading, discharge and gate operations
- Minimize turnaround time of vessels by ensuring containers are placed strategically for loading, and that there will be areas available for unloading
- Maintain haulier truck SLAs (service-level agreements) so that they can be served in a timely manner
Step 2: Define planning decisions
You need to determine the planning decisions carefully, as they will affect the above-mentioned high-level KPIs. Making planning decisions can be tough as it involves many considerations, such as:
- Which areas of the yard will be used for which types of services and containers?
- How high will the yard be stacked?
- Box distribution – how should the rules associated with placement of containers be configured?
Step 3: Model the container terminal “supply chain”
Next, you model the container terminal “supply chain” in the context of the planning decisions that you have identified in step 2. How can you make sure that yard capacity is planned and used at its best? The answer can be found in the flow chart below:
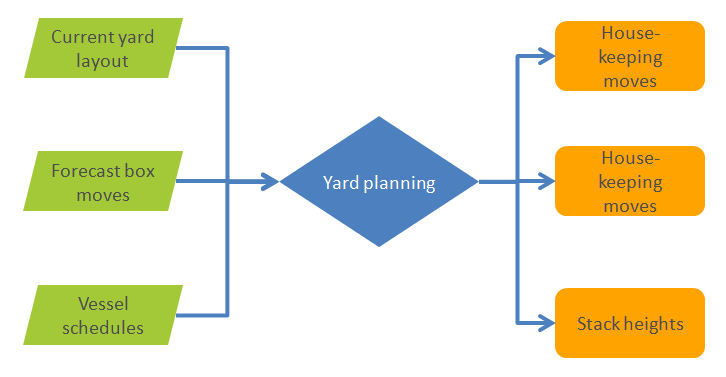
Current yard layout: What is the current yard layout and how dense is it?
Forecast box moves: How many containers will be loaded and discharged? How many are likely to be transhipped and to which destination? When are containers going to arrive and be collected through the gate?
Vessel schedules: When are vessels due to arrive in the terminal? Where will they be positioned in the berth? How long will they be in the terminal? What else will impact this – the schedules of other vessels?
Successful modeling depends on whether all the planning constraints are considered, namely:
- The yard’s dimensions
- The capability of rubber-tyred gantry (RTG) cranes to stack containers at certain heights
- The number of yard cranes that can work in a block at the same time
- And in some cases, the ownership of certain yard blocks (shipping lines usually own or rent parts of the yard)
Step 4: Measure planning KPIs
Once modeling is complete, certain planning KPIs need to be measured. Planning KPIs are different from the overall KPIs (identified in step 1). For example, if you would like to improve SLAs over time, you cannot afford to wait for several months to see the results. You should be able to evaluate this on a daily basis by viewing future scenarios based on a particular decision and act accordingly, before the decision is actually implemented. So what are the KPIs that should be measured for a yard plan?
- Distance traveled by yard tractors between
- the ship and the designated yard positions of the unloaded containers
- yard locations of the containers to be loaded and the ship
- Housekeeping moves of yard cranes (which is basically the number of moves needed to reach a particular container in a stack)
- Turnaround time of vessels
- Turnaround time of trucks
Step 5: Optimize
Finally, you would use optimization to create the best plan as defined by the KPIs in step 4. Yard optimization is just one part of efficient terminal planning. Big calculations can be used to optimize other parts of the container terminal as well. Discover more.
What you should know:
- Big calculations is about real-time optimization that can be applied to any supply chain in any industry.
- Container terminal yard planning is complex as it affects the performance of all logistics operations at the terminal.
- Using 5 discrete steps, we can arrive at a calculated decision on how to optimally plan the container yard capacity on a daily basis.
What challenges are you currently facing in your container terminal yard planning? Let us know in your comment below or drop us a tweet @Quintiq.