What is a digital twin?
A digital twin is a virtual representation of a physical object or system. Unlike traditional simulations, digital twins are continuously updated with real-time data, providing a dynamic and accurate reflection of their physical counterparts.
The key components of a digital twin include sensors on the physical object that collect data, a data processing system that analyzes this information, and the virtual model itself. This setup allows for predictive maintenance, improved performance, and more informed decision-making.
For example, in the automotive industry, digital twins can monitor vehicle performance and predict potential failures before they occur. This reduces downtime and enhances the overall efficiency of the manufacturing process.
By integrating advanced technologies like the Internet of Things (IoT) and artificial intelligence (AI), digital twins offer unparalleled accuracy and insights, enabling businesses to optimize their operations and innovate more effectively.
Understanding the virtual twin
Virtual twins, unlike digital twins, offer a broader scope for representing physical objects and systems. The Virtual Twin Experience takes you beyond the digital twin. They do not simply replicate the physical characteristics, but also provide a more immersive, interactive experience of the entire environment.
Virtual twins leverage an abundance of data from various sources, including sensor data, IoT devices, and historical records. This allows for a more comprehensive analysis and simulation of real-world scenarios.
For example, in urban planning, virtual twins can simulate weather conditions, traffic patterns, and infrastructure changes, providing valuable insights for city planners.
In the healthcare sector, virtual twins can model patient anatomy to predict outcomes of surgical procedures or treatments. This enhances patient outcomes by allowing doctors to plan and rehearse complex surgeries.
By integrating virtual twins into their operations, companies can achieve a competitive advantage, optimizing their processes and enhancing asset performance. This dynamic approach helps in identifying potential issues before they arise, ensuring smoother operations.
Digital vs. virtual twin models and applications
Digital twin technology represents a virtual form of a physical object. From detailed 3D prototypes to realistic organ models, the virtual twin technology pushes the limits of simulation and can provide reliable insights into various complex environments. Digital twins primarily focus on real-time data integration and continuous updates. They are deeply connected to their physical counterparts through sensors and IoT devices, offering real-time insights and predictive capabilities.
In contrast, a virtual twin goes beyond the digital replica by incorporating mechanical, electromagnetic, and microfluidic properties into the design. Virtual twins emphasize experience and simulation. They provide a comprehensive view of an entire system or environment, using data from multiple sources. This makes them ideal for modeling complex scenarios without real-world repercussions.
Virtual twins excel in immersive simulations. For instance, they can simulate an entire manufacturing plant, allowing for extensive testing and optimization. This capability helps manufacturers identify potential bottlenecks and improve efficiency.
While digital twins are more data-centric and tied to real-world objects, virtual twins are richer in context and scenario planning. They support broader use cases, such as urban planning and healthcare, by simulating various conditions and outcomes.
Why do I say virtual twin? IEEE, McKinsey, others: Digital Twins need to be interconnected, multi-purposed, and scalable for maximum effectiveness
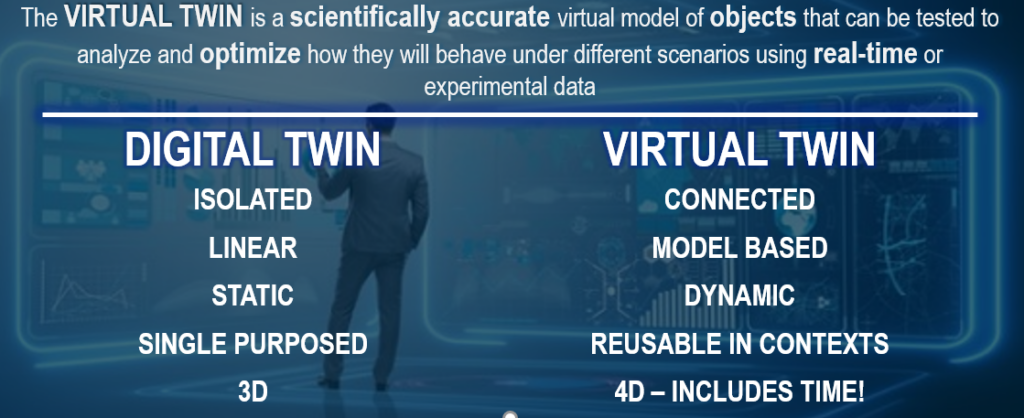
Role of virtual twin experience in manufacturing
Virtual twins play a transformative role in manufacturing by creating virtual replicas of entire production environments. These replicas allow manufacturers to visualize and optimize their operations without physical trials.
For instance, virtual twins can simulate the entire lifecycle of a product, from design to production to maintenance. This capability helps identify potential issues early, reducing delays and improving overall efficiency.
Manufacturers can also use virtual twins to perform real-time monitoring and predictive maintenance. This reduces downtime and extends the lifespan of machinery.
By leveraging virtual twin technology, manufacturers can stay competitive and agile, adapting quickly to market demands.
Gain insight into the virtual twin adoption
Virtual twin for manufacturing
Sustainable Innovation in High-Tech Manufacturing: Virtual Twin
Leveraging the Virtual Twin Experience in the Aerospace and Defense Industry