Dassault Systèmes and Ericsson are at the forefront of addressing these requirements for Industry 4.0 with their legacy of deep industry expertise in how to deliver the necessary capabilities.
How Dassault Systèmes and Ericsson Provide Industry 4.0 Solutions
Dassault Systèmes and Ericsson are helping to transform manufacturing and enable Industry 4.0 solutions. It is a partnership with circular benefits for the entire industry, the workforce and us, the consumers, who crave new products, experiences and connected lifestyles.
Ericsson is one of the leading global providers of Information and Communication Technology, their solutions are critical to modernizing manufacturing. At Dassault Systèmes, we are proud that our DELMIA manufacturing and scheduling solutions are the “heartbeat” of the Ericsson smart factories producing the advanced 5G systems that will unlock the potential of Industry 4.0 for other manufacturers.
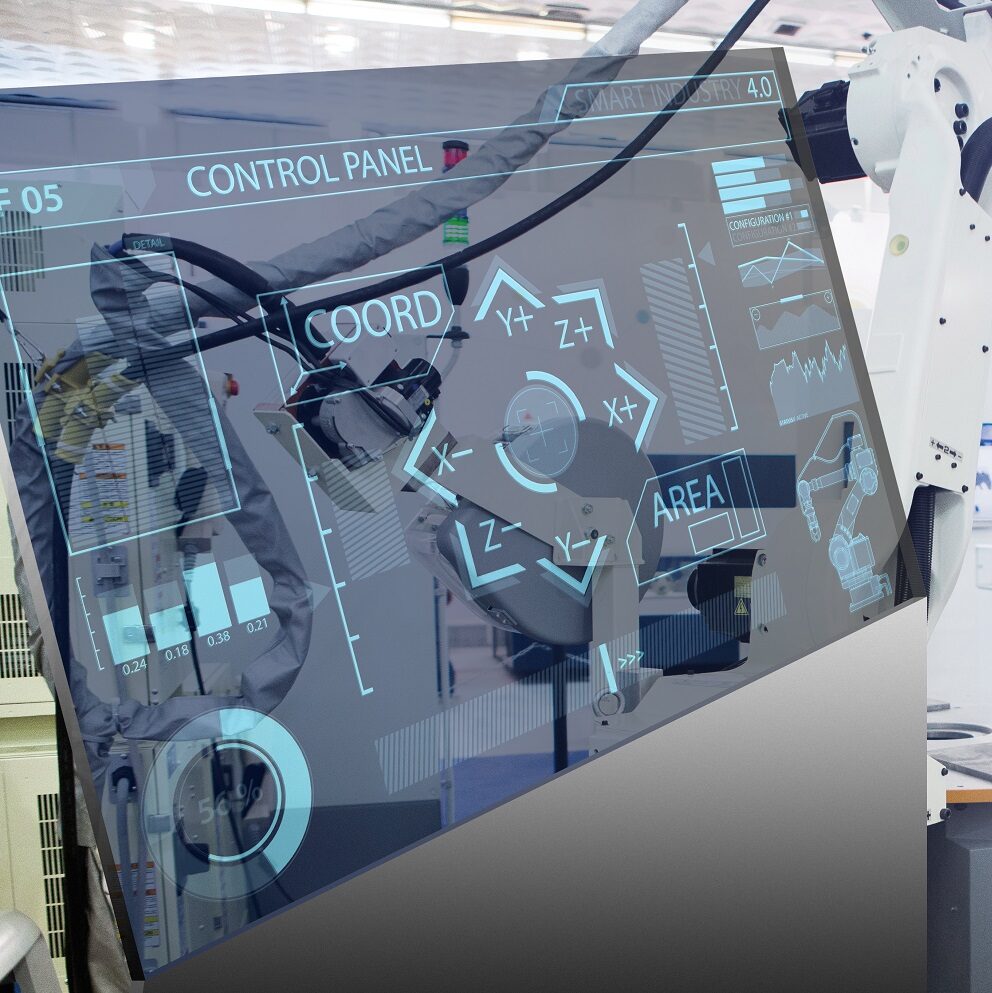
Intelligent, high-performance connectivity is a key requirement for digitalization and increased efficiency and flexibility on the shop floor. DELMIA solutions are the backbone for many traditional industries but they are in their element when leveraged with Industry 4.0 technology, such as digital twins, augmented reality for connected workers, cobots and other virtual world innovations. These innovations unlock immense value for manufacturing but they also require the right environment to be successful.
The key elements of connectivity that manufacturers should be considering
“Next-gen smart applications require absolute reliability with lowest and predictable latency to ensure production flows are seamless and uninterrupted. Add the requirement of flexibility in a facility where process layout can be quickly reconfigured, minimizing downtime, and automated vehicles can move unobstructed, we see that a wireless connectivity solution is needed – specifically 5G technology offering the performance required. 5G allows manufacturers to connect multiple Industry 4.0 solutions on a single network, with uncompromised reliability. And with the business-critical data created from connecting operations with IIoT (Industrial Internet of Things), we believe a private network is best suited, ensuring that critical data remains secured on-site.”
– Alastair Glover, Marketing Lead for Dedicated Networks from Ericsson
Leveraging Next-Generation Connectivity
DELMIA solutions can leverage these capabilities to significant effect with use cases enabled by next-generation connectivity.
For example:
- Live/interactive shop floor monitoring: real-time data collection from every critical workstation in use that provides greater visibility to WIP (work in progress) and resource status to increase flow and asset performance for improved OEE (Overall Equipment Effectiveness)..
- Augmented Reality training & production: high bandwidth, low latency connectivity allows workforce virtual operations to improve build quality and reduce training/assembly times.
- Virtual Twin Experiences: real-time data transfer between physical operations and virtual models of resources enables rapid validation of facility layout changes and virtual commissioning, increasing the overall agility of manufacturing thanks to our virtual factory software.
Ericsson Smart Factories
“End-to-end solutions are what drive efficiency and value in manufacturing. The Ericsson USA 5G Smart Factory is adopting many Industry 4.0 applications that are running off our Ericsson Private 5G network.
Some examples are:
- As driving sustainability and energy efficiency is an Ericsson priority, energy monitoring and management are important. Gathering data about machinery across the factory showing real-time energy consumption and turning off unused machinery resulting in energy savings.
- Augmented Reality in manufacturing for remote support. AR (Augmented Reality) headsets are used by maintenance teams to troubleshoot and repair equipment by connecting to support teams and getting step-by-step system-generated and knowledge-based guidance in real-time.
- Machine learning is based on visual inspection. Visual inspections are often time-consuming and come with an elevated risk of error. By using a high-resolution camera and machine learning algorithms for visual inspections, the accuracy of the inspection increases and inspection times are reduced.
- End-to-end digital thread for production. Machine downtime causes significant costs for manufacturers. Tracking component history, supplier information and test results accelerate root-cause analysis and can reduce repair costs by approximately 20%.”
With product complexity increasing across all industries, it is becoming imperative for manufacturers to increase the agility at which they need to adapt to change and disruption to remain competitive. Additionally, workforce challenges are forcing many companies to move towards higher levels of automation that further drives the need for connected and smart sustainable manufacturing.
Learn more about the possibilities and value offered by DELMIA in High-Tech and Ericsson Industry 4.0 solutions.
Authors:
Adrian Wood, DELMIA Strategy & Marketing Director, Dassault Systèmes
Alastair Glover, Marketing Lead for Dedicated Networks, Ericsson