How Augmented Reality (AR) Transforms Operator Training and Adaptation in Manufacturing
Introduction
In today’s fast-paced manufacturing world, getting operators up to speed quickly and safely is more important than ever. Whether onboarding new hires or shifting experienced workers to a new product line, the faster they can perform tasks accurately, the better for productivity, quality and safety. Traditional training approaches, while helpful, often struggle to keep pace with evolving processes, especially in complex or high-mix manufacturing environments.
This is where Augmented Reality (AR) is changing the game—not just as a classroom tool, but as an integrated part of daily operations on the production line. AR-guided work instructions help workers perform real tasks from day one, accelerating their learning curve and drastically reducing the risks of errors or safety issues.
Let’s dive into how AR enables faster skills ramp-up on the shop floor.
Augmented Reality (AR) as an On-the-Job Skills Accelerator
From Theory to Practice—In Real Time
Unlike traditional training methods that require memorization or simulations, AR provides contextual, real-time guidance directly on the job. Operators—whether newcomers or experienced staff assigned to new programs—can follow step-by-step instructions overlaid onto the real environment, guiding them through complex assembly or inspection tasks with confidence.
This approach drastically shortens the time required for operators to become autonomous and reduces reliance on mentors or supervisors for constant oversight.
Helping Newcomers and Cross-Program Operators
With AR instructions available on smart glasses, tablets, or projectors, new workers can:
- Begin contributing from day one, even with minimal prior experience.
- Learn tasks through visual, interactive cues instead of reading manuals or shadowing others.
- Gain familiarity with product-specific procedures and critical points instantly.
For trained operators switching to a new program or product, AR ensures they:
- Don’t skip steps due to overconfidence or confusion.
- Understand the variations between products or configurations without additional classroom training.
- Receive updates or changes in procedures instantly through updated AR content.
Built-In Safety for Non-Trained Staff
AR isn’t just about boosting speed and performance—it also enhances safety. When companies adapt AR work instructions for less experienced users, they can:
- Highlight potential hazards or mandatory protective equipment at the right moment and location.
- Provide warnings and contextual safety tips tailored for novices.
- Reduce the risk of injury or damage caused by inexperience or misunderstanding.
Best Practices for Using AR to Accelerate Shop Floor Training
To maximize the benefits of AR for ramp-up and operator support, consider the following best practices:
- Create tailored role-specific AR instructions: Customize the guidance according to the operator’s experience level. For new workers, include more detailed instructions, safety notes and feedback loops. For advanced users, streamline content to focus on key changes or new steps.
- Make AR part of the real work—not separate from it: AR works best when it’s used in actual production conditions. Integrate it directly into the operator’s environment, whether via smart glasses, tablets or projection systems.
- Ensure flexibility and device compatibility: Use an AR solution that works across different hardware types (smart glasses, tablets, projectors) and can be reused across multiple lines or plants.
- Keep content updated and modular: As processes evolve or new products are introduced, update AR instructions without having to start from scratch. Modular content makes it easy to adapt instructions quickly.
- Start small and scale: Begin with high-impact areas like complex assembly steps or quality control tasks, then expand as ROI becomes clear.
Key Benefits of Augmented Reality for On-the-Job Training and Skills Ramp-Up
- Faster Autonomy: New operators become self-sufficient much quicker—sometimes in half the time—thanks to real-time visual guidance.
- Lower Error Rates: With step-by-step support, even less experienced workers can perform complex tasks with high accuracy, reducing rework and quality issues.
- Improved Safety: AR can display safety messages, hazard zones and reminders contextually, reducing accidents and injuries for untrained staff.
- Higher Confidence: Workers feel more confident taking on new tasks when they have clear, in-the-moment support, leading to better performance and retention.
- Scalability and Consistency: Whether training one person or a global team, AR ensures everyone learns the same way, reducing variability and onboarding time.
- Reduced Dependency on Mentorship: With AR acting as a digital coach, there’s less need for constant supervision or buddy systems, allowing experienced workers to focus on more critical tasks.
Real-World Example: BAE Systems’ Use of AR for Onboarding and Learning
Since 2020, BAE Systems Air has been using the DELMIA Augmented Experience solution to support operators directly on the shop floor. Integrated into their intelligent workstations, by Fairfield Control Systems, this AR solution improves both productivity and quality on the Eurofighter Typhoon line.
More recently, as part of their CanDLE (Digital Learning Environment) initiative, BAE Systems implemented AR to help operators learn how to use intelligent workstations. This approach provides on-the-job training with real-time support, allowing new operators to learn by doing, directly on the production line.
Discover how operators thrive with AR-enhanced guidance on the shop floor. Learn more on BAE Systems’ website
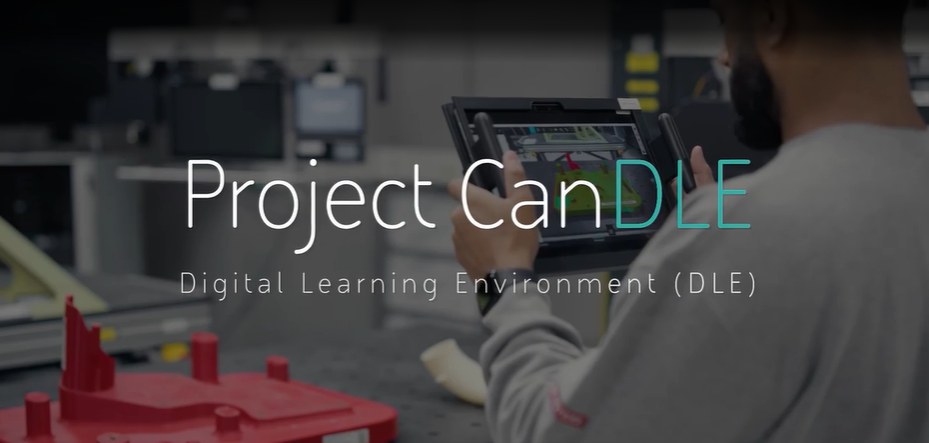
Considerations and Challenges
Implementing Augmented Reality (AR) in manufacturing isn’t without its challenges. Companies must ensure they have the right infrastructure in place, including AR-capable devices such as smart glasses, tablets or projectors, as well as reliable connectivity to deliver real-time content.
There is also a need for thoughtful content design. Poorly structured or cluttered AR instructions can overwhelm rather than help, so it’s essential to keep content intuitive and modular. Integration with existing systems, such as MES or PLM, may also require technical planning and coordination.
Finally, change management is key. Employees may be unfamiliar with or hesitant about adopting new technology. Involving them early, demonstrating value through small pilots, and gradually building confidence can make the transition much smoother.
Although these considerations require an initial investment of time and resources, the long-term benefits—such as faster ramp-up, reduced errors, and safer operations—more than justify the adoption of AR on the shop floor.
Conclusion
AR isn’t just a training tool—it’s a powerful enabler for real-time performance and rapid skills development. By embedding AR into the production environment, manufacturers empower their workforce to learn and adapt faster, reduce the risk of errors, and stay safe—all while keeping operations efficient and consistent.
Whether it’s onboarding new hires or helping experienced operators master a new program, AR bridges the gap between learning and doing—right where it matters most. In fact, users of DELMIA Augmented Experience have reported up to 50% faster skills ramp-up, demonstrating the tangible impact of AR on workforce readiness and productivity.
Want to see how AR can accelerate skills ramp-up in your factory?
Explore how DELMIA’s AR solutions can drive faster onboarding, improve accuracy, and support workers at every level.
📘 Download our white paper: Transforming the Workforce with AR/VR in Manufacturing