Habibi Husain Arifin, AP South Manufacturing – Industry Process Consultant, Dassault Systèmes
The aerospace and defense sectors are under increasing geopolitical pressure to deliver complex, high-performance systems faster, more securely and cost-effectively than ever before. To this end, Model-Based Systems Engineering (MBSE) as a digital-first approach to managing the complexity of modern engineering has become a crucial accelerator in defense and aerospace programs across the globe.
The goal of digital engineering, which originated as a strategic initiative by the US Department of Defense, is to connect all components of the defense ecosystem — from government and regulatory bodies to prime contractors, their suppliers, and manufacturers — through shared digital frameworks. Countries like the UK and Australia have since adopted similar strategies. In 2024, Australia introduced its own digital engineering standard, influenced and benchmarked against the US initiatives.
These frameworks emphasize four foundational pillars: digital twin, digital thread, digital artifact, and the digital model. Among these, the digital model that comprises requirement, structural, functional, and architectural representation lies at the heart of MBSE. It provides a shared language and more consistent and traceable “source of truth” that enhances collaboration across multiple engineering disciplines.
What is MBSE and why does it matter?
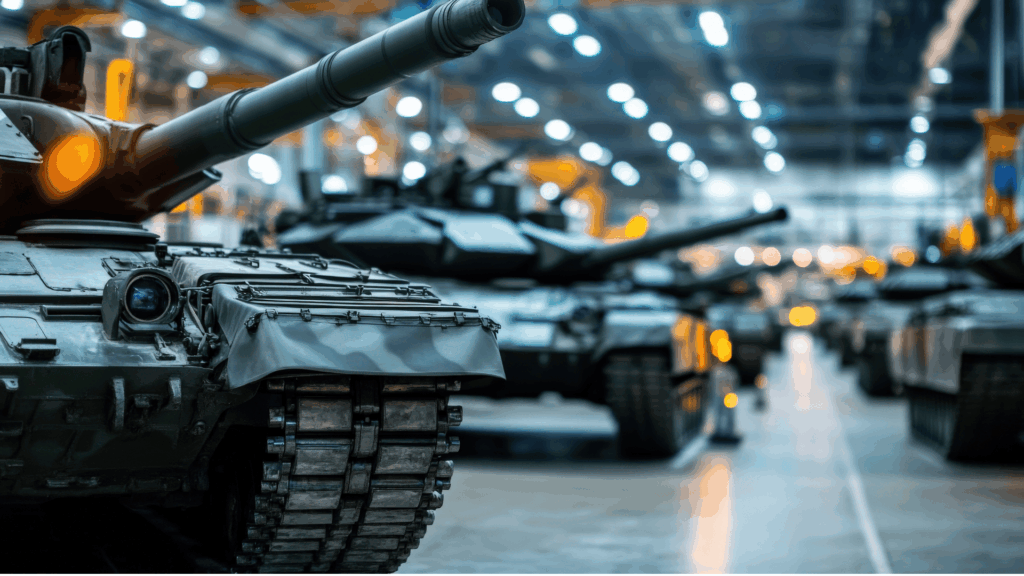
To understand MBSE, one must first grasp systems engineering. Systems engineering acts as a transdisciplinary umbrella connecting specialized fields such as mechanical, electrical, electronics and software engineering. It ensures that all subsystems and components of a system work in harmony.
MBSE takes this one step further.
Rather than relying on traditional documentation, MBSE captures all system requirements, designs, and validations through integrated models. These models are not just visual diagrams. They are dynamic, semantics-rich artifacts that enable data-driven decision making, reuse, validation, simulation, and traceability.
A paradigm shift is essential to implement MBSE. Organizations are required to transition from a document-based culture to one rooted in digital models. This shift enhances information continuity and traceability, reduces errors caused by miscommunication, and increases the velocity and accuracy of design iterations.
Why MBSE adoption is crucial in aerospace and defense
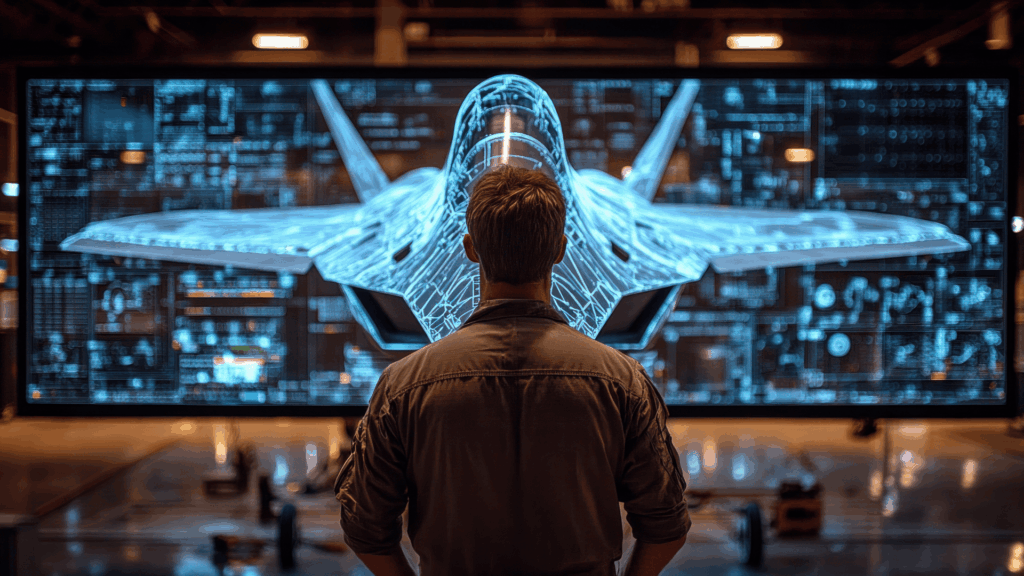
Aerospace and defense were among the first industries to adopt MBSE. These sectors operate in what is known as the “mission-critical” space — where system failures can result in collateral damage to life and property or compromise national security.
The complexity of defense and aerospace systems has grown exponentially. In the early 20th century, products were primarily mechanical. Today’s systems are integrated with electronics, software, and increasingly AI and autonomous capabilities. This evolution brings with it a surfeit of interfaces including mechanical, electrical, software, and network that are required to be meticulously managed.
Managing such complexity with document-based systems not only leads to inaccuracy but is also increasingly impractical.
MBSE offers a scalable solution by organizing, simulating, and validating multiple systems in a unified digital environment with clear benefits: better system integration, early error detection, streamlined compliance, and significantly improved collaboration across stakeholders.
Dassault Systèmes, through its CATIA Magic platform (previously known as MagicDraw or Cameo), is at the forefront of MBSE adoption in the defense and aerospace industry. CATIA Magic is one of the most standards-compliant tools on the market, supporting frameworks like UML and SysML, UAF, UPDM, DoDAF, MoDAF and NAF.
For many years, CATIA Magic has been globally referenced as a preferred industry solution. Countries across Australia and ASEAN aiming to replicate this success would benefit from deploying CATIA Magic — not as a mandated standard but as a preferred solution.
Key benefits of MBSE
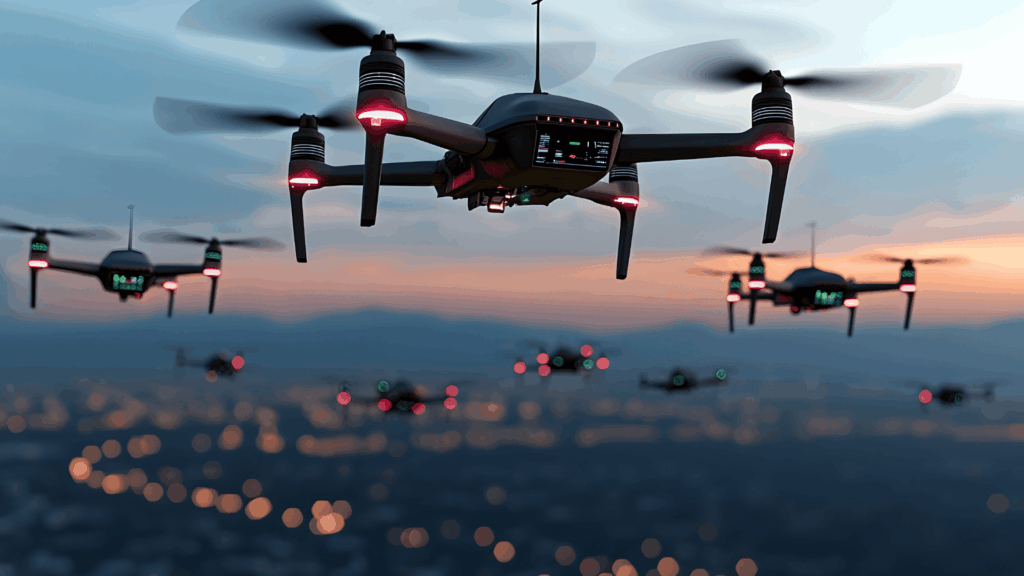
1. Managing complexity: MBSE excels at handling the growing complexity of modern systems. It offers a structured way to model interfaces and dependencies across hardware and software components, reducing the risk of integration failures.
2. Traceability and quality assurance: Every change in requirement is automatically propagated through the model with MBSE. This allows for real-time impact analysis and traceability across the development lifecycle, something extremely difficult to manage with static documents.
3. Enhanced reusability and cost efficiency: MBSE promotes modular design and reuse through model libraries. Organizations can create standardized components and design patterns that can be adapted across multiple projects, reducing cost and development time. It also supports product line engineering, enabling variants to be developed more efficiently.
4. Protecting intellectual property: In a collaborative digital ecosystem, IP protection is critical. MBSE platforms like CATIA Magic offer fine-grained control over projects and models access, including features like data markings and classification, filtering, and web-based viewing that prevent unauthorized access to sensitive model information and protected IP assets.
5. Enabling future-ready capabilities: MBSE supports early-stage design and architecture modeling that integrates the mechanical, electrical, and software domains. This ensures that downstream teams work from a common baseline, reducing the need to start from scratch and preserving design continuity all the way to manufacturing to easily support potential innovations in the future.
6. Higher Return on Investment in downstream processes: While MBSE may increase effort during early design phases, it significantly reduces downstream efforts in detailed design, implementation, testing, and support. Studies consistently show more effective and efficient efforts when MBSE is implemented across the full product lifecycle.
Industry challenges to MBSE adoption
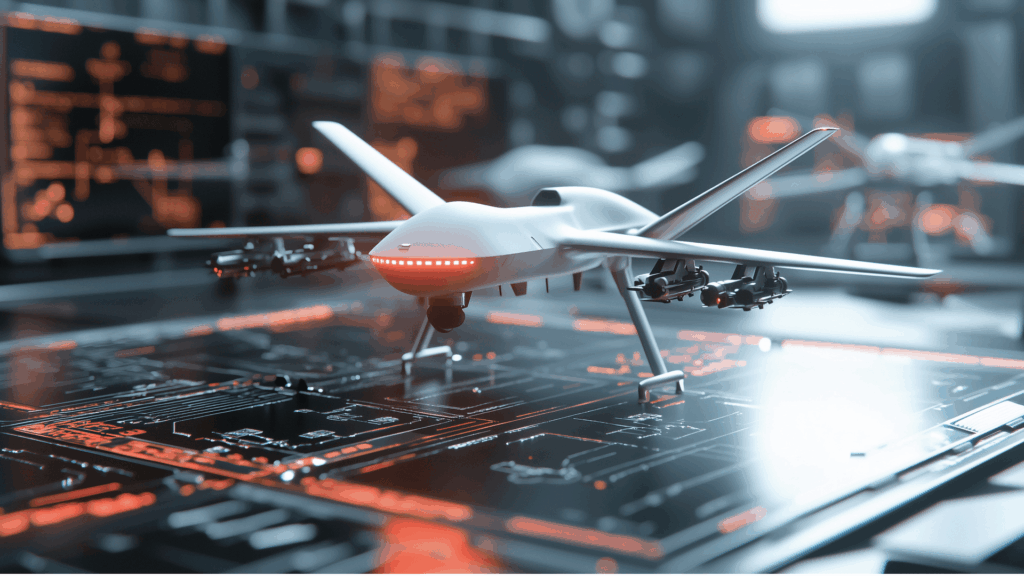
Despite its advantages, adopting MBSE isn’t without hurdles. The biggest challenge lies in shifting organizational mindset and culture. Teams accustomed to working with documents need to learn new tools and methodologies. Governments and companies alike are investing in workforce upskilling to bridge this gap.
Another barrier concerns the protection of proprietary information. However, MBSE platforms such as CATIA Magic now offer robust information or model exchanges, various features of access control, and data markings and classification mechanisms, making it easier to collaborate without compromising IP.
From system of systems to manufacturing and operations
In the defense supply chain, MBSE supports a multi-tiered ecosystem. At the top are government bodies defining mission-level capabilities. These are translated into system-level requirements (for example: a fighter jet or a submarine) and then decomposed further by OEMs and subcontractors. Finally, this information flows down to manufacturing.
MBSE provides a unified framework that supports this entire hierarchy from high-level capability modeling to detailed physical design and manufacturing to operational instructions. This end-to-end traceability ensures information integrity throughout the product lifecycle.
As aerospace and defense systems become more intelligent, interconnected, and autonomous, traditional engineering approaches are no longer sufficient. MBSE is now a strategic necessity. By embracing MBSE, organizations can accelerate development, improve quality, protect intellectual property, and ensure future-readiness in a complex and high-stakes development environment where speed, accuracy and quality have become crucial.