Layers upon layers upon layers…
Diapers, bandages, feminine hygiene products, paper towels. What do all these things have in common? Yes, they are all consumer products, but more accurately, they are all layered products. A layered product is developed by adding layers of material on top of each other in the manufacturing process. It’s particularly tricky as many of the layers needs to adhere to one another via glue or stitching or other means of adhesion. The product designers behind these products? Their job is particularly tricky as well.
Manufacturers know all too well the complexities of working with soft layered product stacking. The pace of products in these massive categories is high, putting pressure on designers to accelerate the innovation process. Their goals are to deliver multi-discipline engineered products with high-quality product designs at a low cost.
It’s all about the weight
When dealing with different layers of material that will go into a product, it’s critical the each material is used efficiently. This means utilizing the material to minimize the amount that is ‘trimmed’ off and disposed of during the manufacturing process. This is called ‘trim weight’. Trim weight is important because it is a cost….the material is an expense and some of it ends up being discarded through the cutting and production process. Minimizing the trim weight keeps costs down.
It’s important to have design tools that accurately measure area and weight values associated with:
- Net area and net weight
- Gross area and gross weight
- Trim area and trim weight
The good news is that with the right digital design solution, managing all this complexity and weight doesn’t have to be so daunting.
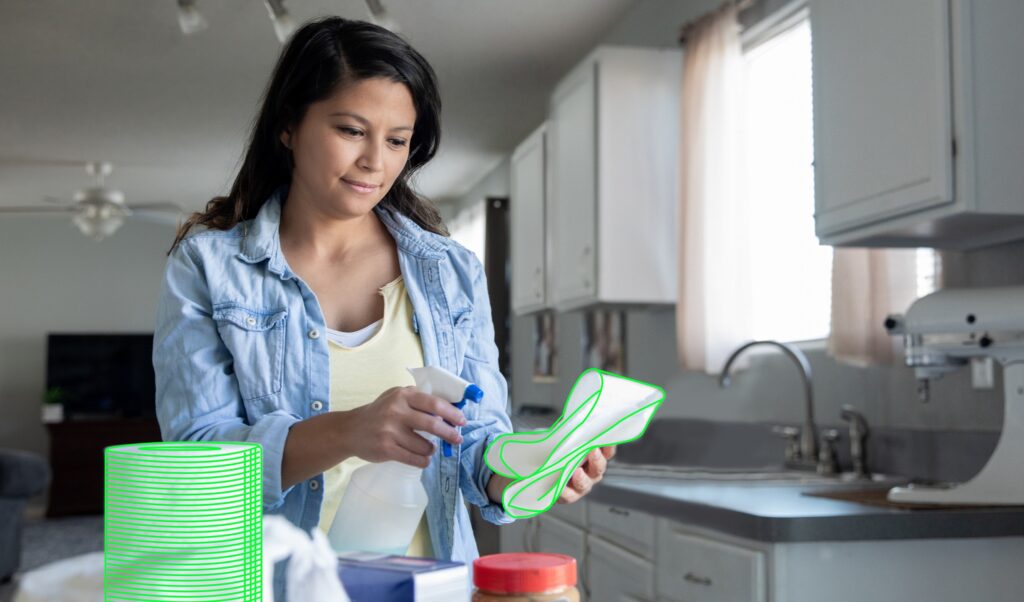
Optimizing layered product design
New design capabilities from Dassault Systemes’ 3DEXPERIENCE® platform can accelerate layered product development. The solution, called ‘Layered Product Designer’, enables designers to create the complex soft layered product stacking with ad-hoc representations and accurate weight monitoring. Designers using the solution can create their innovative designs with an immediate assessment of the weight computations based on net, trim and gross formulas. The solution is powered by CATIA, providing a powerful and easy-to-use set of capabilities to design models assembled by several layers and materials. The solution addresses the products manufactured through production lines by capturing different transformations such as fold, cut perforation and bonding actions.
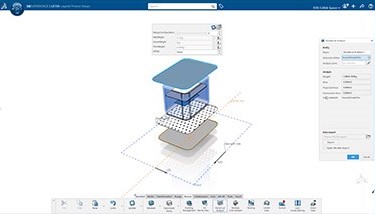
Traditionally, these products are made with an extensive amount of manual file transfers between designers and simulation specialists. With up to hundreds of simulations per product, this manual process is time consuming and costly. By using a collaborative platform, this data transfer is seamless, enabling swift action between all stakeholders involved. Unifying modeling and simulation enables faster optimization of products, and swifter time-to-market.
Cost is critical in categories of this size
Layered products help give the ‘fast moving consumer goods (FMCG)’ industry its name. The diapers market is expected to grow from $63.2 billion in 2023 to $110.0 billion in 2033, a 5.7% compound annual growth rate over that time. The global feminine hygiene products market is anticipated from grow from $43.2 billion in 2024 to $73.1 billion in 2032, a 7.8% CAGR. This means that even a small reduction in material for a product can translate into enormous cost savings.
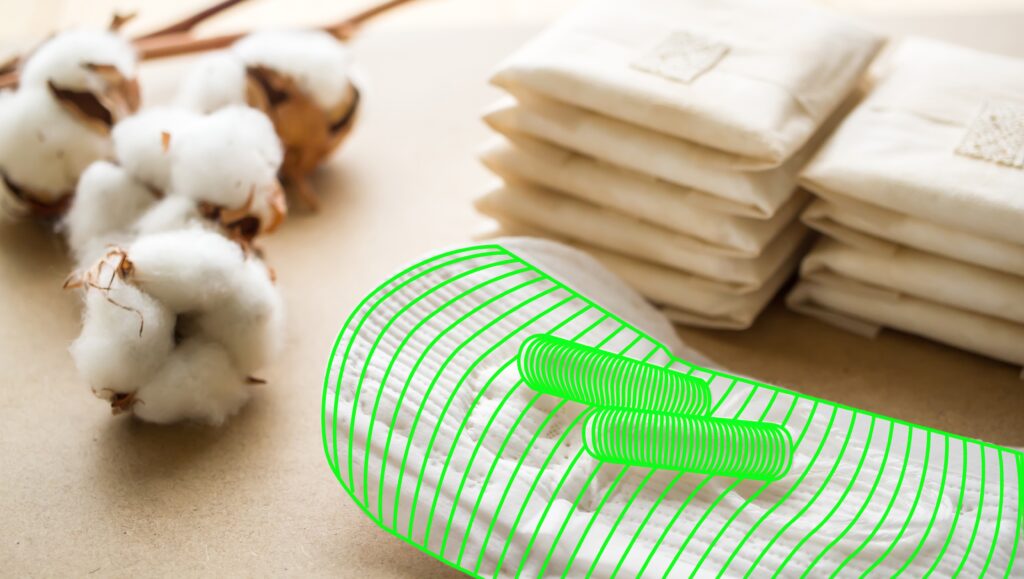
Moving forward with the right solution for your needs
The exacting nature of layered product development and the critical importance of product quality and weight efficiency makes choosing a specialized design solution vital to the future growth of beauty companies.
Please visit our site where we detail the solution being used by leaders in the layered product categories and watch a demo on how the solution works. While you’re at it, feel free to download our ebook and solution brochure.