What is a Composite Material?
A composite material is a material made from two or more constituent materials with significantly different physical or chemical properties. When combined, they produce a material with characteristics different from the individual components.
The first modern composite material was fiberglass. It is still widely used today for boat hulls, sports equipment, building panels and many car bodies. The matrix is a plastic and the reinforcement is fine glass threads woven into a sort of cloth. On its own, the glass is very strong but brittle and it will break if bent sharply. The plastic matrix holds the glass fibers together and protects them from damage by spreading out the forces acting on them.
We are now manufacturing some advanced composites using carbon fibers instead of glass. These materials are lighter and stronger than fiberglass but more expensive to produce. We use them in aircraft structures and expensive sports equipment such as golf clubs.
What Are the Advantages and Challenges?
The biggest advantage of modern composite materials is that they are light and strong. By choosing an appropriate combination of matrix and reinforcement material, one can make a new material that exactly meets the requirements of a particular application. Composites also provide design flexibility because one can mold many of them into complex shapes. The downside is often the cost. Although the resulting product is more efficient, the raw materials are often expensive.
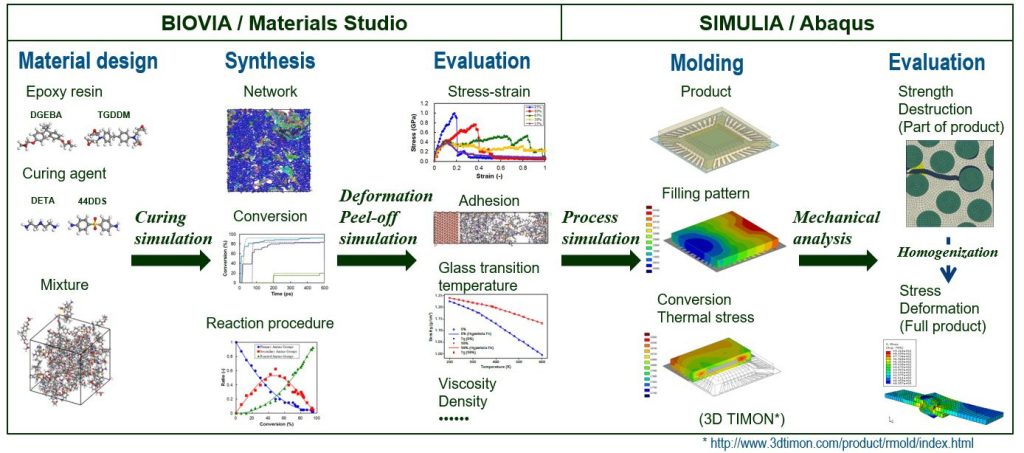
As shown in Figure 1, epoxy resins are a key material used in composites. The Figure depicts a workflow that calculates molecular properties from epoxy resins using molecular level modeling with BIOVIA Materials Studio and then passes the material-dependent properties like glass transition temperature and mechanical properties to SIMULIA’s Abaqus Finite Element Method. We use this class of thermosetting resins in a wide range of applications from adhesives to encapsulants to coating agents and many more.
Predicting Material Properties
A recent collaboration between BIOVIA scientists and academia has resulted in two interesting publications having to do with simulation and experimentation aimed at predicting a particular material property and to understand the intrinsic phenomenon of resin crosslinking. The publications provide two different perspectives on the role of cross-linking in material stability for epoxy resins.
The first publication describes the curing process, especially the dependence of heterogeneity on curing time. Coarse-grain modeling is the key process required to understand this phenomenon. The second publication addresses the adhesion of epoxy resins over metal surfaces. The key observation from that paper is that if the size and/or shape of the constituent molecules change, the aggregation states such as density, molecular orientation and concentration also change; which affects the deceleration of the curing reaction and results in change of adhesion strength.
This a priori-validated methodology can be used to screen new materials of interest. Chemistry-to-device connectivity is a big step in the virtual design of new functional materials. These two publications also provide guidance for those interested in virtual testing where molecular simulations generate properties that are usable at the macro-scale to improve the predictability of the device scale property.
A Simplified MD Methodology
The automated workflow shown in Figure 2 reduces the tedious process of calculating the properties required to understand the crosslinking, the glass transition temperature and stress strain curve, enhancing the productivity of the research scientist. The process also rationalizes the mechanical properties based on the primary confidence with the glass transition values obtained from the workflow. We have built a general workflow to calculate these properties using Molecular Dynamics methodology that makes the calculation process much simpler for the bench chemist. We wanted to make it possible for the bench chemist to screen these properties prior to experimentation, thereby reducing the time, effort, money and resources needed to develop functional composites for particular applications.
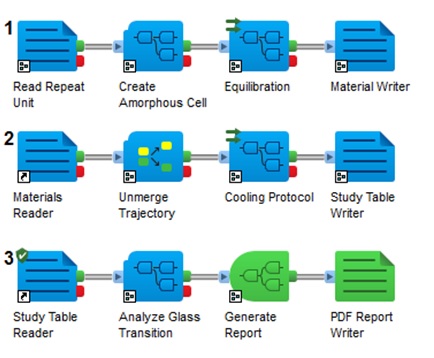
One can use the crosslinked amorphous structure built with the varying composition under examination to form a network structure, which is key for the design of the composite material. In this way, one can monitor the conversion of the crosslinking from 0% to 100% over time as shown in Figure 3.
References:
-
Mesoscopic Heterogeneity in the Curing Process of an Epoxy–Amine System, Mika Aoki, Atsuomi Shundo, Riichi Kuwahara, Satoru Yamamoto and Keiji Tanaka, Macromolecules 2019, 52, 5, 2075–2082
-
Molecular Events for an Epoxy−Amine System at a Copper Interface Satoru Yamamoto, Riichi Kuwahara, Mika Aoki, Atsuomi Shundo, and Keiji Tanaka ACS Appl. Polym. Mater. 2020, 2, 1474−1481