Time-to-Market affects Aerospace in its own commercial methodology. Digitalization has the potential to create substantially more value for customers in the form of more innovative, reliable, and affordable offerings that get to market quicker.
Yet, delivering this value will not be easy.
Across the global A&D sector, $20 billion in incremental annual EBITDA (an approximately 10 percent improvement based on 2018 global sector EBITDA of $200 billion) can be created through digital. This value will come from both OEMs and suppliers, and from expanding revenue and reducing costs across the value stream: engineering, supply chain and procurement, manufacturing, aftermarket services, and support functions (Source: McKinsey report)
From an Indian perspective, the Aerospace (A&D) market is estimated to reach around $70 billion by 2030. The Digital Services transactions themselves are expected to reach $4 billion by 2025.
Immense value will be captured on a global scale!
A recent study reports services & digital experience as being the least digitally mature element of the value stream. It cites only 12 percent of companies using digital experience and analytics services to build new service offerings tailored to customers’ needs.
Still, digital experiences can open tremendous opportunities in this domain. Several companies have realized this and are taking action. For instance, Boeing and Airbus are both pioneering ways to unlock the power of digital experiences & data analytic services for customers. Engine OEMs have also been trailblazers in applying digital tools / digital training & maintenance experiences and analytical methods to improve customer value.
The value opportunity from integrating digital experiences right in A&D is immense. As one executive said, “Properly sustaining an aircraft results in seven times the value over the initial sale.”
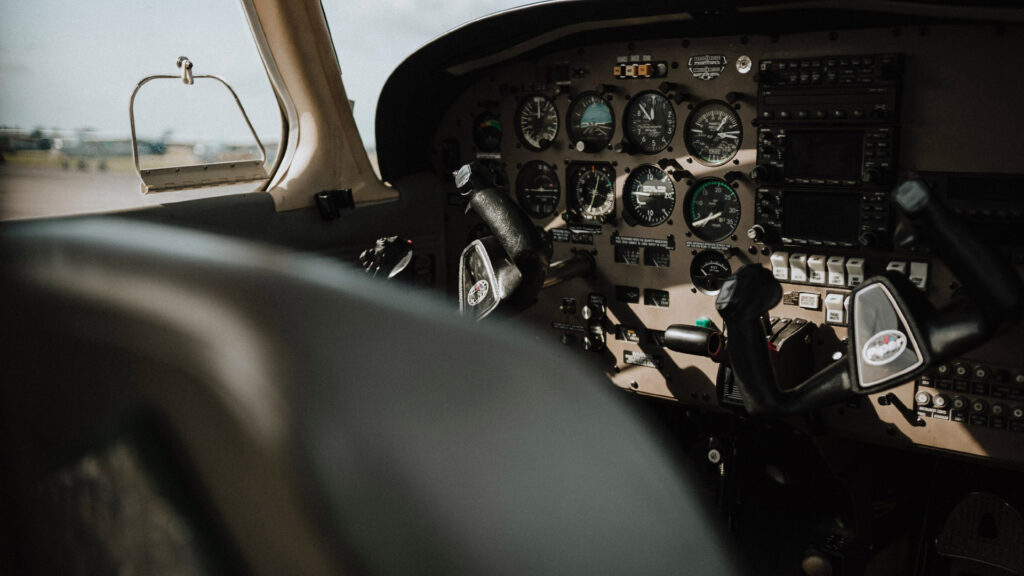
What also stands out is the key factor to reach digital experiences : Virtual Twins
Virtual Twin technology not only enables to create curated digital experiences but also improves collaboration between facilities and suppliers — it allows customers to test concepts and designs in real-time, from anywhere, in the most true-to-life format possible & provide custom training and explorative virtual experiences. This helps to improve communication while also driving innovation and helping to ensure that expectations are met.
But is this the only approach that can benefit Aerospace? – No.
According to a 2022 report by Ian Land, Senior Director, Aerospace and Government Vertical Solutions.
A fundamental question that teams ask when utilizing virtual twins is: What system level is being considered? Is it for a subsystem like the braking system in an aircraft? Is it for a printed circuit board in the cockpit? Or is it for an underlying chip and its software that drives critical control functions with an aircraft? While the principles remain the same across different system levels, virrtual twins are important in aerospace and government because they can augment or replace the physical systems which were required for prototyping in the past. They are also valuable for developers in multiple locations or for demonstration to a customer or user.
For example, the Joint Strike Fighter has over 25 million lines of code and has 30,000 pounds dry weight: Imagine the challenge to modify the software code and physical computer hardware as the aircraft control processing and surfaces are changed during development. The cost and time involved is enormous, let alone the possibility of achieving a healthy failure-to-success ratio. Additionally, prototyping provides the most benefit when it is utilized early in the development stage and adds significant value post hardware availability, when critical design decisions such as CI/CD flow and fault injection methodologies are being made — an impossible feat to achieve without actual hardware. This is where virtual twins play a crucial role in testing, validating, and verifying both the hardware and software in real-world conditions.
With a digital twin, businesses in aerospace can unlock more potential out of future and current parts by obtaining the necessary data to understand what’s working, what’s not, and what can be done better in the future.
Moving forward, the wave of Aerospace digitalization is growing and will keep growing. It’s time for a collaborative effort to champion towards a common goal of a more sustainable & faster time-to-market future.