Imagine a factory floor. There might be machines with levers and conveyor belts, sifting and sorting through raw materials and objects, hairnetted employees or workers in coveralls and industrial protection. You might hear the ring of an old-timey alarm signaling a lunch break or the end of a workday.
Manufacturing doesn’t look the way it once did — and that’s a good thing. With the complexity of goods and consumer demand both skyrocketing, it needs to change with the times. That also means that manufacturing efficiency looks different, too.
Today, many factories — if not most — have replaced individual workers with machines and automation. The sorting and sifting that previously required human attention and interaction is now done via technology. The nature of consumerism demands peak productivity 24/7, making reliance on automated machinery practically a necessity.
As shoppers, we might not necessarily realize all the ways we benefit from manufacturing efficiency. Take something like monogramming, for example: a task that not long ago required stitching or embossing by a tailor and took valuable time can now be completed by a machine. There’s also next-day shipping, which relies on precise processes running perfectly to be able to deliver products on-demand.
But there’s a lot at stake when it comes to manufacturing. A company might be a single entity, or contain a number of subsidiaries, all producing different goods. They might have a group of manufacturing sites concentrated in one area, or they may be spread out across different geographies. They might produce 50 types of items, or 500, each with its own unique formula, specification and workflow.
Keeping track of all this, particularly on a global scale where there’s competition to build and retain loyalty among customers, is increasingly difficult to do manually. So companies around the world are turning to digitization for maintaining excellence and efficiency in their manufacturing operations.
Particularly for companies producing consumer goods, the ability to quickly and efficiently manufacture high-quality goods at scale is an important measure of success. By leveraging technology, companies can do this by planning, scheduling and executing their manufacturing processes with ease and agility.
The secret three-part sauce to manufacturing efficiency
If you think of manufacturing as a recipe, then you can understand precise planning, scheduling and execution as necessary steps to produce the optimal result. If one is out of whack, the end product will be flawed, so striking the right balance is critical.
But what exactly does manufacturing efficiency look like? For most companies, it’s the ability to produce uniform quality goods at a specific pace and at the lowest possible cost. Achieving this sort of equilibrium can only happen with digital programs like virtual twins, which enable digital mapping of all the variables associated with a product, product line, or a company’s entire product offering.
Planning
Nothing in life is possible without proper planning, and manufacturing is no exception.
Planning can help companies avoid complications, optimize decision-making, save money, forecast accurately and simply be more efficient overall. It requires companies to be aware of all the possible variables that exist for their goods, workflows and production sites. It necessitates constant awareness of resources and requirements.
Understanding those variables means also understanding what influences them. A supply chain disruption can be disastrous for a manufacturer that hasn’t planned for potential hiccups. Knowing all the ways in which quick substitutions can be made, shipping routes can be changed or any other type of last-minute adjustment can be applied will make a world of difference when manufacturing under some sort of pressure.
When LAVIGNE, a stationary company, needed to introduce a system to streamline their planning processes, they turned to the DELMIA Ortems solution. By implementing it, they were able to increase their capacity for orders by 30% and even deliver more than a third of their orders ahead of schedule. They needed increased visibility for production schedules to up their manufacturing efficiency during peak production season, and DELMIA helped them accomplish this.
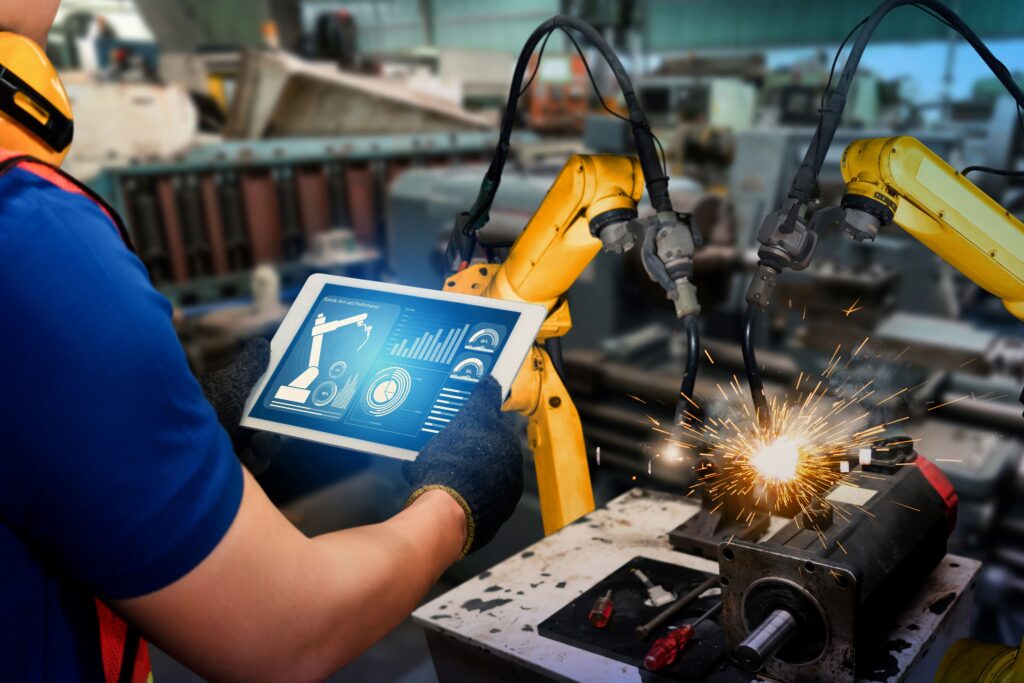
Scheduling
Scheduling is the next key component. For every product a company manufactures, there are unique workflows — sometimes multiple — that must be carried out in a specific timeframe. The planning phase gives the roadmap, but the scheduling phase dictates exactly what can be done, when, and where.
Knowing all the potential variables involved in a product’s formula is a necessity for its production, but true manufacturing efficiency also takes into account the capability of the site where goods are produced. Understanding every site’s capacity is crucial for preventing bottlenecks, and can be the determinant in a company’s ability to produce goods at pace and introduce new ones.
By implementing a short-term production scheduling software tool, manufacturers can achieve synchronicity within and between production lines. If a machine’s functionality changes, the scheduling system dynamically recalculates production dates, timelines and workflows.
Execution
Proper manufacturing execution, enabled by the DELMIA Apriso’s Manufacturing Operations Management (MOM) software, gives companies the ability to standardize, centrally manage, scale and optimize processes.
Having this sort of unity allows identical goods to be produced across production sites simultaneously. This synchronicity is bolstered by the agility achieved when using a system that maintains a digital finger on the pulse of all a site’s operations. Pivoting and optimizing become simpler matters, not obstacles.
While planning, scheduling and execution all require some level of human interaction, removing reliance on individuals can be a net positive for companies and consumers alike. Products can be produced uniformly and quickly, with a lowered likelihood for buyers receiving something defective. For shoppers particularly concerned with ethical business practices, putting the labor on machines creates better conditions for workers and relieves labor constraints. Bolstering this is the fact that technology-led manufacturing that’s powered by virtual twins empowers more sustainable practices, making the process not only time efficient and cost effective, but good for the planet as well.
LIXIL: Putting opportunity into action
Putting all of these tenets together can be an involved process. But it becomes even more complex when they’re applied to multiple companies within an enterprise. That’s exactly the challenge that LIXIL needed to tackle when it merged 5 Japanese companies in 2011 to become a larger corporate entity.
With all the potential success that can come from such a large business transition, there are also plenty of pain points that companies tend to experience. For LIXIL, those included standardizing operations across these now-united businesses and implementing business management operations that would work for all of them individually and as an enterprise.
By implementing DELMIA’s Apriso, they were able to standardize all the goings-on throughout their subsidiaries. Doing so allowed them to maintain operational standards and excellence across the board. With dozens of plants around the world producing millions of individual pieces and products every day, unification was a necessity for reaching efficiency in their manufacturing scheme.
Technological manufacturing systems are fantastic in the way they enable scalability, but offering this in conjunction with the flexibility for customizable goods is less common. Because so many of LIXIL’s goods, like faucets and other bathroom fittings, require significant customization, this wasn’t something they could skimp on. DELMIA’s Manufacturing Execution System (MES) software, which bolsters synchronicity in the execution phase of manufacturing, offered them the best of both worlds. The MES is like an on-the-go control panel for every aspect of a product’s workflow, giving companies real-time visibility to make adjustments and optimizations as needed.
If you’ve ever renovated a house — or dreamed of doing so — you understand the need for access to hyper-specific fittings for specific spaces. LIXIL, then, needed a system that would be perfectly compatible with all the options that could be exercised in their production. By deploying the MOM and MES, the company was able to cohesively manage the production of their wide-ranging product line.
The manufacturing industry needed to make the transition to the tech-powered version we know it as today. Consumers want products to be readily available, easily customizable, quickly shippable and of consistent quality. For companies to be able meet those expectations, the implementation of manufacturing efficiency programs is imperative.
In the fast-paced manufacturing space, excellence is achievable if goods are produced of a consistent quality, at a consistent pace, and increasingly, at scale. This task, while large, is achievable with the right tools. Companies can ensure success by implementing systems and leveraging technologies that streamline the necessary elements of proper planning, scheduling and execution.