Over the past decade, the need for more sustainable practices in the manufacturing industry has grown substantially. As a consequence of rising temperatures—and the resulting storms, wildfires, droughts, and other severe climate events—both consumers and investors are looking to manufacturers to minimize their carbon emissions. And these essential stakeholders expect more than just lip service. They want to see tangible evidence that companies are not only setting meaningful sustainability goals but also putting the appropriate processes in place to meet them.
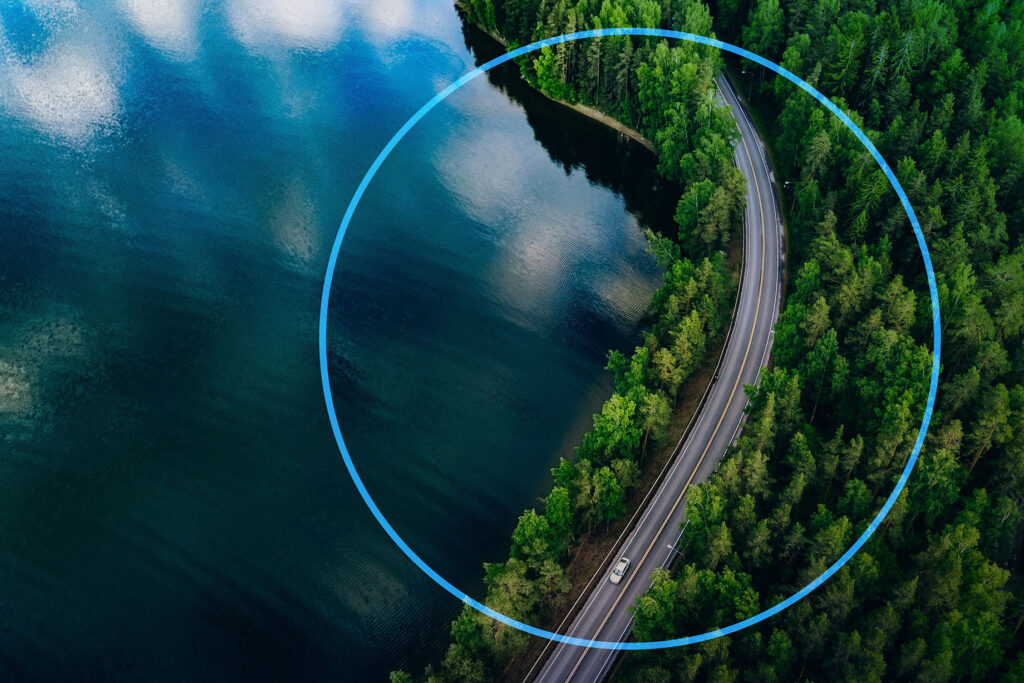
As a result, today’s manufacturing organizations must perform a remarkable balancing act to remain competitive in their respective markets. They must find a way to cut costs, manage risks, and meet these critical sustainability goals—but they must do so while still maximizing revenue. This requires not only more investment in sustainable practices but also more innovation. As companies look to build credibility and ethics into the DNA of their manufacturing efforts, they must find ways to align product innovation with ongoing business initiatives, including environmental, social, and governance (ESG) goals.
Traditionally, manufacturers have relied heavily on physical prototyping and assembly line validation methods to make process improvements. Unfortunately, these approaches not only cost significant money but take significant time. They can hinder progress to market, which is a huge problem and impacts an organization’s profitability. But these outdated methods also increase a product’s potential environmental burden.
Given that approximately 80% of a product’s environmental impact is set during the design phase, organizations benefit when they can determine eco-friendly material selection, energy efficiency, and manufacturing processes as early as possible in the product development timeline.
In this quest for a better balance of sustainability and design in alignment with business goals, companies will find value in tools that optimize the product lifecycle and, consequently, reduce environmental footprints and foster positive revenue growth. They can do so through Eco-design, an innovative approach to designing products and services that carefully considers the environmental impacts of a product throughout its lifecycle.
When engineering teams have tools that support Eco-design, they can more easily integrate sustainability into their development cycles. Early in the design process, they can find ways to reduce resource consumption, source renewable or recyclable materials, optimize energy requirements, reduce waste, and lower carbon emissions.
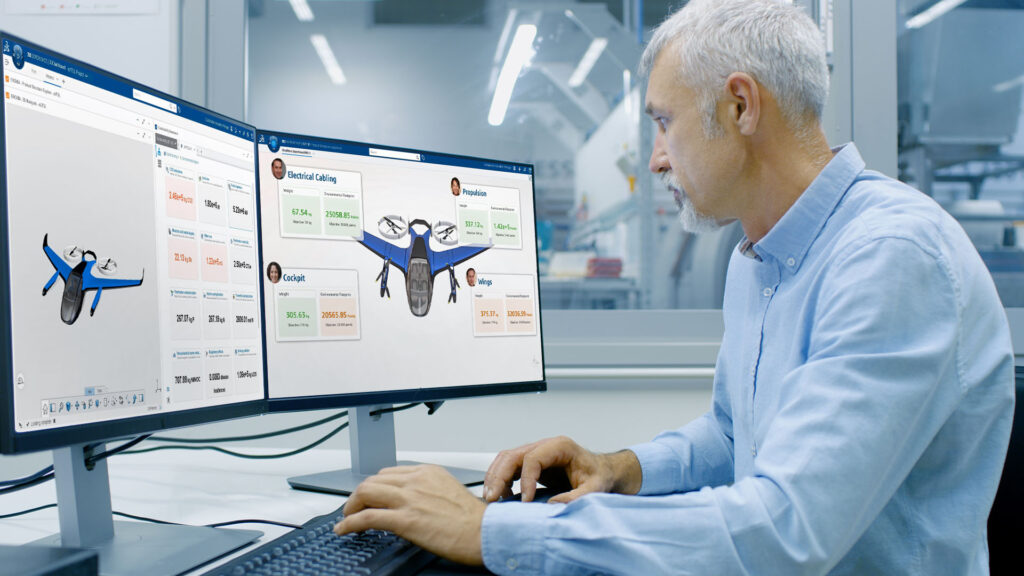
Moreover, the benefits of Eco-design go beyond managing and reducing environmental impact. In fact, they also help organizations decrease development and production costs, foster customer and investor loyalty, avoid unnecessary rework or retrofitting, and stick to strict development schedules. By seamlessly integrating virtual twin solutions into their processes, organizations can take a significant leap forward. These solutions allow them to create digital replicas that provide critical insights into manufacturing, materials, and operations.
When they integrate those virtual twins with Eco-design practices, engineers are empowered. They gain access to critical, real-time data to help them understand a product’s energy consumption and overall environmental impact. The combination of Eco-design and virtual twins also allows for the modification of computer-aided design (CAD) models, helping engineers create efficient products that are validated by simulation analysis during virtual tests. As a result, when engineering teams can integrate Eco-design early into the product development process, they will see a snowball effect across all downstream efforts.
In an era where sustainability is no longer an option but a necessity, the manufacturing industry faces the challenge of meeting eco-conscious demands while maintaining competitiveness. Fortunately, by embracing innovative approaches like eco-design and virtual twin solutions, companies can pave the way for a more sustainable future. These methods not only reduce environmental impact but also streamline product development, ultimately maximizing profitability.
To dive deeper into these transformative strategies, explore our comprehensive ebook and join the movement towards a greener, more competitive manufacturing landscape.